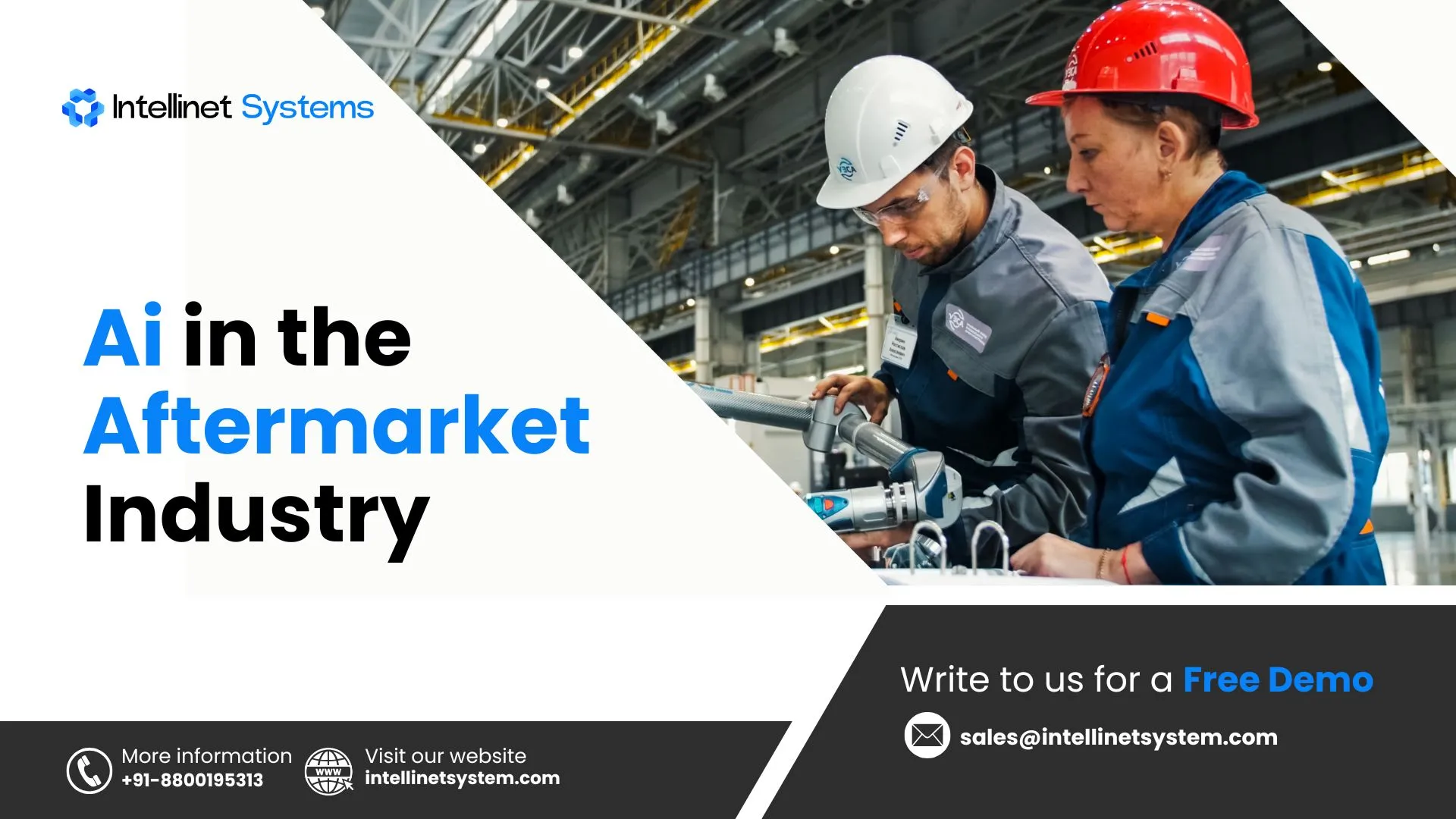
The aftermarket industry is a broad marketplace for accessories, parts, and services used once the product is already sold. This industry involves several complex aspects, including inventory management, quality control, and supply chain management.
OEMs are consistently looking for ways to improve their aftermarket operations to reduce equipment downtime and increase efficiency. The rapid evolution of advanced technologies like Artificial Intelligence (AI) has enabled manufacturers to automate processes and streamline operations. AI modules such as machine learning and natural language processing have simplified complex processes.
This article will discuss how implementing AI proactively allows OEMs to mutate their operations while maximizing efficiency. We will also explore the future opportunities in AI that shall empower manufacturers and help them maintain competency in the evolving aftermarket sector.
How AI Revolutionizes Major Aftermarket Functions
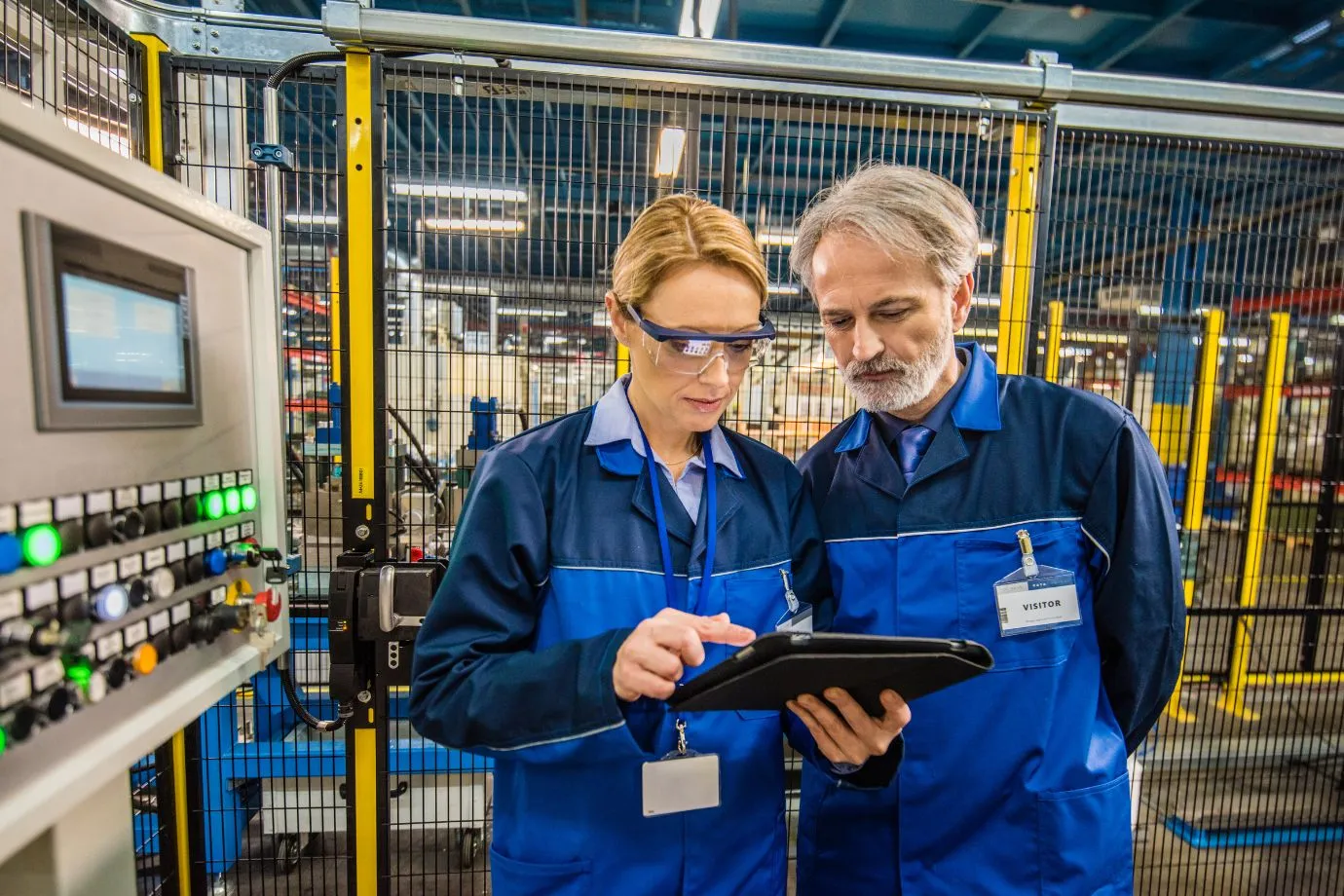
Artificial intelligence extensively analyzes data from multiple sources such as sales, warranty, customer support, and customer behavior patterns. This analysis enables OEMs to extract valuable insights, identify key shortcomings, and curate possible corrective measures.
Advanced AI modules simplify complex processes through automation, allowing OEMs to focus on more essential work while reducing processing time and maximizing efficiency. AI-enabled analytics also helps in forecasting future trends such as parts demand and equipment breakdown, making OEMs future ready.
Let’s discuss the role of AI in transforming several aftermarket processes below:
Product Functionality and Design
AI-based modules help OEMs streamline research, automate graphic-related tasks, and improve the design process. Right from collecting and interpreting information to customizing designs as per user needs, AI helps in pipelining product functionality.
AI analyzes large data including surveys, social media, and user feedback to identify patterns, trends, and derive insights. It also enables designers to automate repetitive tasks such as resizing or color-correcting images.
AI-empowered design tools can automatically generate product prototypes, layouts, and designs, accelerating the process while minimizing errors. This helps in improving overall design efficiency, allowing OEMs to make informed decisions for enhancing product design and enhancing user experience.
Technical Documentation
Modern interactive manuals provide smart search capabilities that enable OEMs to access product or service related information quickly. When powered with AI tools, these interactive manuals provide features such as system-generated FAQs, AI chatbot, and text summarization.
Intelli Manual is one such AI-powered interactive manual that integrates AI to provide smart search capabilities. Its speech-to-text and text-to-speech feature helps users to search for required information quickly and with precision.
The system-embedded AI chatbot allows users to make searches in their natural language while choosing their preferred mode of search (voice or text). It's machine learning algorithms analyze user queries and automatically suggest relevant questions related to a specific manual. This advancement accelerates the search process and reduces downtime.
Additionally, Intelli Manual also provides a feedback loop allowing users to provide feedback after every response. This not only helps in enhancing user satisfaction but enables OEMs to facilitate continuous improvement.
Spare Parts Catalog Management
Advanced catalog management system has streamlined how OEMs organize, store, and access details of spare parts. With interactive features such as detailed parts analysis and 3D-visualization, spare parts catalog software enables dealers to accurately identify the required spare parts.
Intelli Catalog is an advanced parts catalog software that uses AI to streamline parts catalog management. Its AI-powered features like image cleansing enhance the visual quality of images, helping technicians and dealers to identify parts easily and accurately. Another useful feature is the text-to-speech and speech-to-text conversion that allows technicians to search the required part using natural language. This enables them to reduce search time while minimizing the risk of ordering incorrect parts.
Parts Planning and Inventory Prediction
Advanced AI modules help OEMs by significantly contributing to managing spare parts and optimizing parts planning. AI analyzes historical sales data, product usage patterns, and ongoing market trends to accurately forecast spare parts demand.
It also leverages machine and deep learning to study any patterns of seasonal fluctuations, enabling OEMs to strategize corrective measures.
Inventory Management
Maintaining optimal spare parts inventory consistently is crucial for aftermarket OEMs to ensure smooth operations and retain customers. AI-enabled modules such as computer vision automate crucial processes such as stock inspection and provide valuable insights.
These insights derived from stock inspection enable OEMs to determine damage and defects. By automating this process, AI allows quicker, more accurate quality evaluation while reducing the risk of selling faulty parts.
Parts Pricing
By analyzing real-market conditions and competitor pricing, manufacturers can adjust the prices of specific spare parts dynamically. It not only maximizes profitability but also helps in adapting to changing market fluctuations quickly. This provides OEMs with a competitive advantage in the dynamically-growing market.
Additionally, this AI-enabled analytical approach helps OEMs to segmentize their customers based on factors like demographics, purchase history, and behavior patterns. This helps in curating personalized strategies to various customer types and executing promotions and discounts to specific customer divisions.
Supply Chain Management
AI-enabled tools enable OEMs to transform their supply chain, right from sourcing to production. These innovative tools analyze data from multiple sources to predict possible disruptions, establish streamlined operational processes, and optimize logistics.
Technologies like deep learning evaluate data and regulate various aspects of the supply chain, including production, route optimization, and supplier management. This helps OEMs efficiently manage supply chain operations while reducing costs significantly.
Predictive Maintenance
One of the most significant features of AI in aftermarket operations is predictive maintenance. AI systems analyze large volumes of data to predict equipment break downs and suggest maintenance requirements. This data often consists of historical sales records, warranty guidelines, and any ongoing trends in the market.
AI algorithms not only help in identifying patterns in equipment failure but also recommend suitable maintenance tasks and help OEMs in scheduling them. It also allows manufacturers to detect deviations in data, helping them forecast potential equipment failure early and take preventive measures. With smart learning abilities, AI also refines its predictions over time and improves accuracy.
Field Service
AI uses machine learning to analyze data patterns, helping OEMs streamline their field services. This analysis helps in ensuring that the most suitable technician is available at the site and at the scheduled time.
AI-enabled modules automate the routine field tasks such as scheduling and routing. This helps technicians face less distractions and focus on more important tasks, saving time and boosting their efficiency.
Furthermore, AI in field service also facilitates technicians with modules like augmented reality (AR). This technology is a game changer for technicians working on complex maintenance and repair settings.
It helps them overlay visual representations including diagrams, equipment layout, and 3D models directly on the real site objects they are working on. This enables them to diagnose issues and perform repairs more efficiently.
Quality Control
By accurately detecting product defects in production, AI allows OEMs to regulate quality control processes. Advanced AI tools such as machine learning and computer vision automate inspection processes, ensuring consistent high-quality production. Practices like predictive monitoring further facilitate quality checks by identifying quality issues in production even before they occur.
This automated and futuristic quality analysis approach minimizes human intervention while eliminating possible errors involved in manual handling. It enables OEMs to improve quality control efficiency while also cutting on unnecessary costs. This not only enhances product quality and reliability but helps OEMs strengthen brand reputation.
Warranty Management
Warranty management is a crucial element of aftermarket operations that directly affects a brand’s reliability and sales. Advanced warranty management system helps OEMs to streamline their warranty claims and resolve them proactively.
AI-enabled warranty management systems further automate processes such as claim processing, helping OEMs reduce manual errors and enhance accuracy. By integrating technologies such as natural language processing (NLP), AI helps OEMs to generate insights from warranty claims data and streamline data entry.
AI tools analyze warranty data to identify patterns in recurring claims, detect any fraudulent claims, and help in preventing unnecessary costs. These tools also forecast potential equipment failures, allowing OEMs to work on repair strategies much in advance.
Customer Support
AI tools help in automating routine tasks and customize customer interactions, improving the aftermarket customer support. Machine learning algorithms analyze data to predict issues customers are likely to register, identify problem trends, and streamline inquiries to the most suitable support agent.
Additionally, AI-powered intelligent search features enable support teams to instantly access required information from the knowledge base. This helps in significantly reducing resolution time and enhances efficiency.
Knowledge Base Management
By providing functionalities such as natural language processing (NLP) and real-time knowledge updates, AI makes managing knowledge base seamless for OEMs. NLP modules enable support teams and technicians to access information in common languages, easing the search process. This helps them solve complex queries easily while also enhancing their efficiency.
AI-powered features such as semantic search and personalization go beyond keyword research to interpret the context of a query. This enables users to find a relevant solution even when they don’t know the exact keyword or phrase of information they are looking for.
At the OEM end, AI modules analyze customer support tickets to identify any prevailing content gaps. Based on new queries and customer feedback, AI also helps in automatically updating the knowledge base by publishing relevant query-focused articles.
Future AI Trends in the Aftermarket Industry

With frequent advancements in technology, artificial intelligence is evolving how OEMs handle spare parts, reduce warranty claims, and build customer loyalty. Future trends in AI such as AI-assisted customization and integration with tools like blockchain and IoT are expected to accelerate this advancement further.
Let’s explore these future AI trends in the aftermarket sector below:
Blockchain
Blockchain provides a decentralized, distributed system that allows instant sharing of important information across a network. By providing sealed records of parts and components throughout their lifecycle, blockchain shall improve traceability, security, and transparency among AI-enabled systems.
Internet of Things (IoT)
Integrating Internet of Things sensors on future AI applications shall help OEMs collect real-time data from connected devices. This will provide data-driven insights, enabling manufacturers to make quick adaptations to changing market demands, regulate inventory supply, and enhance customer service.
AI-Powered Customization
Analyzing consumer data such as purchase history, equipment usage, and behavior patterns helps in understanding consumer needs more efficiently. This will allow OEMs to personalize customer experiences and build unwavering loyalty towards the brand.
Advanced Automation
Exceptional automation practices such as robots in repair processes shall improve precision and overall efficiency. It can be used in performing repetitive tasks such as component removal and installation, reducing manual processing.
Conclusion
The rapid evolution of advanced technologies such as Artificial Intelligence has brought about a transformation in the aftermarket industry. With significant enhancements in domains such as parts cataloging, quality control, and field services, AI has slipped into multiple areas of aftermarket operations.
Adopting AI-powered aftermarket solutions with progressive technologies such as natural language processing and machine learning enables manufacturers to automate processes and enhance operational efficiency.
This not only helps in maximizing profit margins but also adds a competitive edge to their business goals in the highly-competitive aftermarket space.
To explore more about how AI can transform your aftermarket operations, connect with our experts today!