.webp)
Efficient spare parts ordering and fulfillment play a crucial role for OEMs in maintaining continuous operations and enhancing customer satisfaction. Industries such as Original Equipment Manufacturers (OEMs) depend heavily on a systematic and streamlined supply chain of spare parts. The traditional spare parts supply chain practices often include challenges, hindering timely order fulfillment and inventory optimization. The introduction of Artificial Intelligence (AI) in the process revolutionized how OEMs manage spare parts.
AI in the spare parts ordering and fulfillment process utilizes the latest technologies like machine learning, advanced analytics, and natural language processing (NLP). By improving spare parts identification and optimizing inventory management, these features help streamline the entire aftermarket supply chain. This article will explore the role of AI in overcoming the challenges in traditional practices, the benefits it offers, and the upcoming trends. We will also share actionable insights and best practices for implementing AI in spare parts ordering and fulfillment.
Common Challenges in Traditional Spare Parts Ordering and Fulfillment
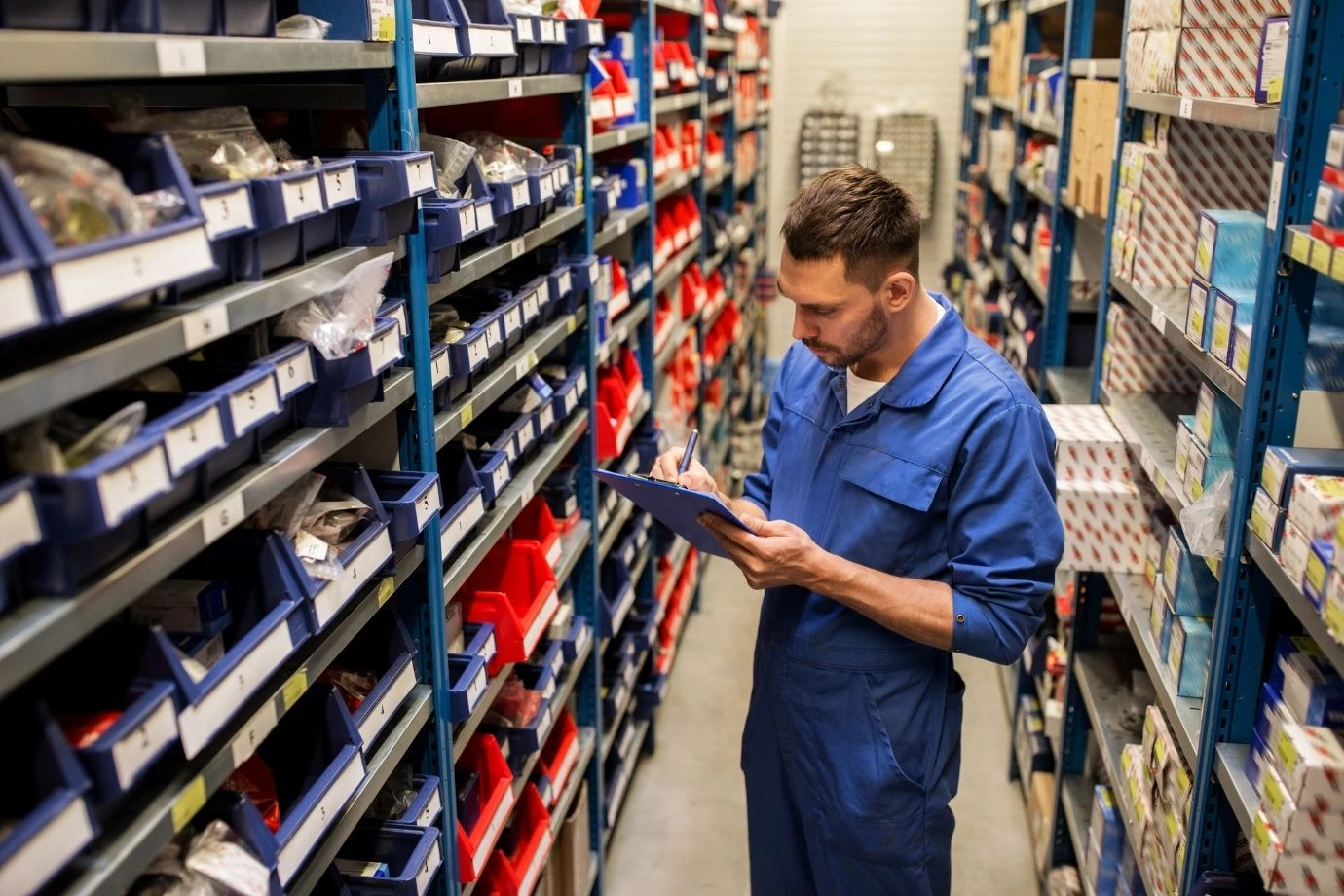
The traditional processes of spare parts ordering and fulfillment usually involve multiple challenges, hindering operational efficacy and customer satisfaction. These methods entail supply chain challenges like inefficiency in accurate parts identification, mismanaged inventory levels, and frequent manual errors. Such challenges often lead to incorrect orders, frequent fulfillment delays, and higher operational costs.
Let’s explore these challenges involved in conventional methods of spare parts ordering and fulfillment below:
1. Manual Errors and Inefficiencies
Manual intervention in parts ordering processes commonly causes errors of various types like the selection of incorrect parts or data entry mistakes. The errors lead to delays, misplaced orders, multiple operational disruptions, and revenue leakages. For instance, an incorrect part selection may hamper repair operations until the correct part is sourced, causing higher downtime and operational losses. Errors made during data entry can further lead to the shipping of wrong components and complicate the process. This makes it crucial to implement automated parts ordering system in integration with inventory management software.
2. Difficulty in Parts Identification
Identification of correct spare parts from an extensive catalog is often an error-prone and time-consuming process. Industries with customized or specialized machinery or those where components may not always be regulated are often more prone to this issue. Poor operational handling like inadequate labels or incomplete part data may further complicate the identification process. Manual searching through part numbers and descriptions is also time-consuming, increasing equipment downtime.
3. Inventory Mismanagement
Conventional inventory management processes often struggle with forecasting accurate demand for spare parts. This may result in parts stockouts or overstocking, both causing hindrances in smooth operations. While stockouts cause delays in essential maintenance and obstruct production slots, overstocking leads to high storage costs. Overstocked parts may also get outdated with time, contributing to operational waste. The lack of data-driven forecasting and real-time tracking systems is a major cause of these issues.
4. Supply Chain Disruptions
Fulfillment of spare parts orders may sometimes get hampered due to complexities in global supply chains and unexpected events like pandemics and natural disasters, or geopolitical tensions. These disruptions cause extended downtime and a halt in equipment production. Several industries encounter these pervasive effects of delays in the supply chain, right from manufacturing and construction to healthcare.
5. Reverse Logistics Complexities
Operating spare parts returns and reverse logistics involves multiple stakeholders and is generally a disintegrated and inefficient process. This complexity causes delays, difficulties in tracking the return status, and increased operational costs. Inefficient reverse logistics may also result in high part wastage as returned parts may not be rapidly inspected, refurbished, or restored into inventory.
How AI Transforms Spare Parts Ordering and Fulfillment
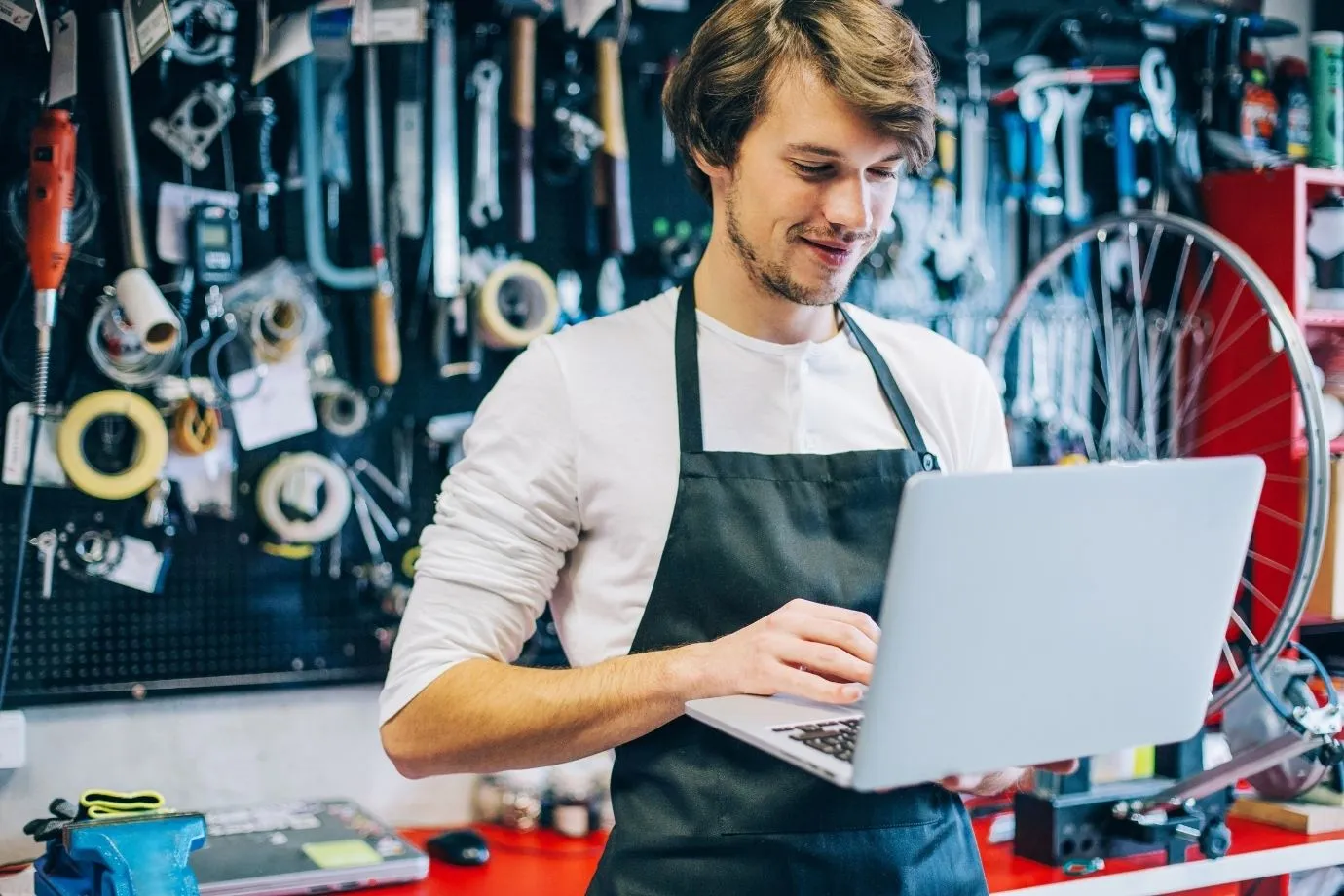
With the integration of Artificial Intelligence into spare parts management, OEMs have transformed their order handling, fulfillment, and overall spare parts operations. Implementing AI-driven spare parts catalog software enables OEMs to improve efficiency, accuracy, and responsiveness in parts ordering processes.
Let’s have a look at significant approaches to how AI reshapes spare parts ordering and fulfillment.
1. Parts Identification and Search Optimization
Identifying parts accurately is a crucial step in managing spare parts. AI provides exceptional opportunities like image recognition and voice-assisted search to assist individuals with limited technological knowledge. This helps OEMs streamline processes and reduce operational costs. Advanced AI-enabled spare parts catalog software provides the following modern features:
a. AI-Powered Image Recognition
Identifying components accurately is often one of the major challenges in spare parts management, especially with incomplete, distorted, or unclear visual data. Once a picture is clicked and uploaded on the parts catalog software, AI-driven image recognition systems analyze spare parts photographs and determine their identity with significant precision. It helps in eliminating frequently occurring errors during manual identification, significantly reducing time spent on searching for spare parts. By automating this process, AI helps in identifying and sourcing correct parts quickly and efficiently.
b. Natural Language and Voice Search
Natural Language Processing (NLP) is an advanced technology that allows users to search for parts using their everyday language rather than typical technical dialects. This particularly simplifies the search process for less technical staff while improving overall user experience. Voice search also offers hand-free convenience, allowing technicians to search for spare parts without barging on their work. These evolutions reduce search time and enable more accurate identification of spare parts.
c. AI-Powered Image Cleaning
By using modern cleaning and enhancement tools, AI can also enhance poor-quality images. These tools automatically rectify distortions, adjust lighting, and remove background noise, enabling ease for image recognition systems to identify and categorize parts accurately. This allows OEMs to maintain more accurate and detailed spare parts databases.
2. Inventory Prediction and Management
By implementing advanced data analytics, AI-powered tools help in keeping track of inventory and manage stock levels efficiently. Data-driven analytics also helps in identifying demands, enabling prediction of future demand and dynamic stock recovery.
a. Demand Forecasting
AI-driven predictive analysis significantly helps in forecasting demands for spare parts. To generate accurate demand predictions, AI systems analyze historical sales data, current market trends, and external factors like seasonal fluctuations. These insights help OEMs maintain optimal inventory flow, preventing both stockouts and excessive stocks that freeze capital.
b. Dynamic Inventory Retrieval
Real-time tracking and AI-powered insights allow OEMs to dynamically modify their inventory recovery strategies. This approach ensures continuous optimization of inventory based on changing demand patterns. By minimizing the risk of stock shortages or overstocking, manufacturers can save costs while achieving higher operational efficiency.
3. Supply Chain and Reverse Logistics
Limited data tracking of supplier performance and lack of transparency in the supply chain often turn order fulfillment throbbing for OEMs. AI helps in addressing these pain points and enables smoother spare parts operations.
a. Supply Chain Optimization
By analyzing data from multiple sources like supplier performance, transportation logistics, and market conditions, AI improves supply chain visibility and decision-making. OEMs can utilize this detailed analysis to foresee possible disruptions and strategize accordingly.
b. Efficient Reverse Logistics
Handling returns and managing refurbished spare parts are crucial aspects of spare parts management. By identifying return purposes, optimizing return dispatch chains, and managing the refurbishment process, AI automates various return processes. This automation reduces processing durations and improves cost efficiency.
4. Smart Routing and Fulfillment
AI algorithms analyze distribution center locations, delivery partner proficiency, and customer requirements to optimize order fulfillment. This helps determine the fastest and most cost-effective routes for order delivery, ensuring timely order fulfillment. With this feature, OEMs effectively reduce shipping costs while also improving delivery speed and customer satisfaction.
Key Benefits of AI in Spare Parts Ordering and Fulfillment
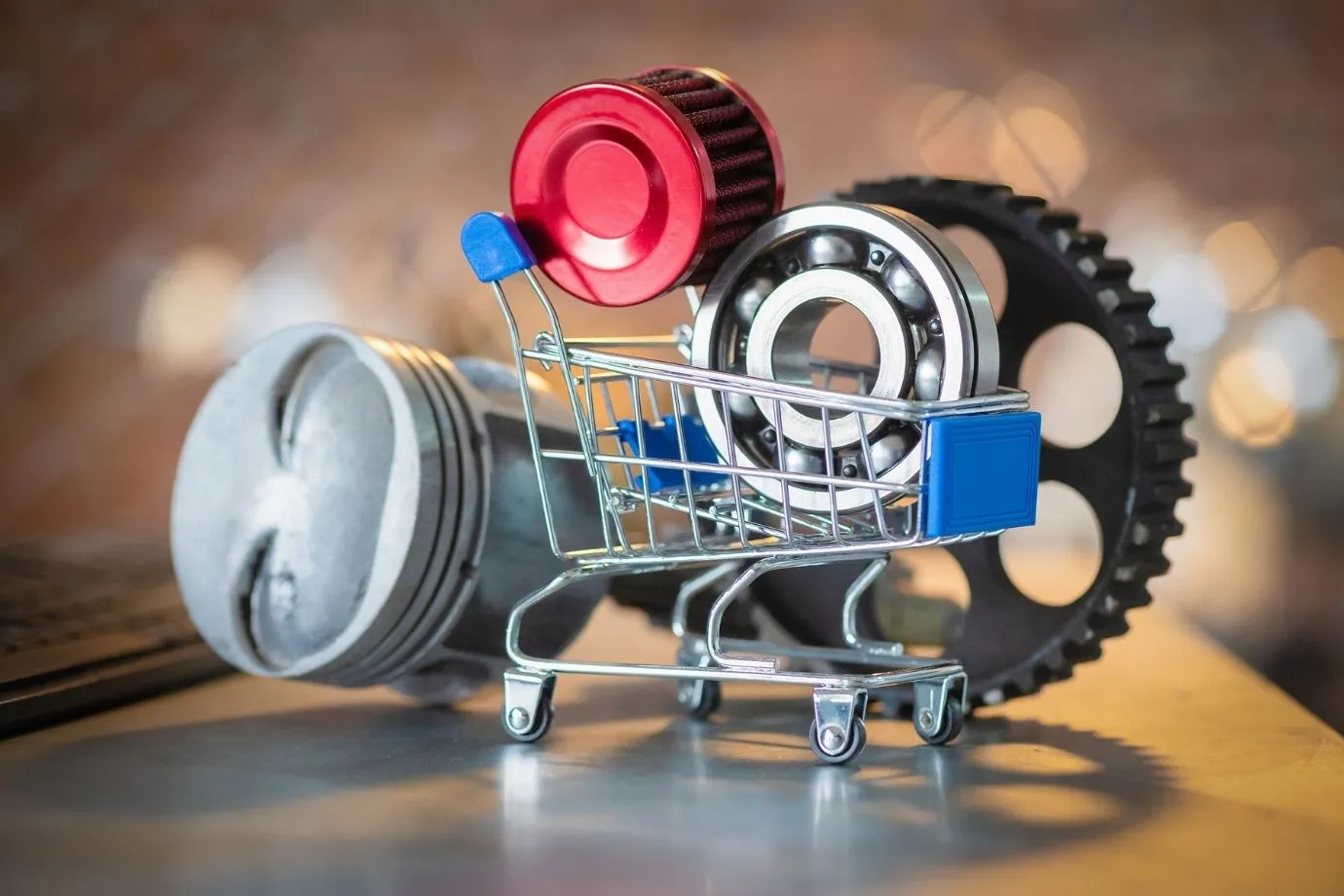
Integrating AI in spare parts ordering and fulfillment provides several benefits to the OEMs. These primarily include cost savings, data-driven decision-making, and enhanced operational efficiency. Let’s explore these benefits in detail below:
1. Enhanced Accuracy and Speed
One of the most significant advantages of AI in spare parts ordering and fulfillment is the notable refinement in speed and accuracy. Conventional manual methods depended heavily on human input, leading to frequent errors in parts identification, order processing, and delivery tracking. These errors cause delays, misdeliveries, and a recurring need for returns and reorders.
Implementation of AI-driven systems enables OEMs to identify patterns and forecast demands with noticeable precision. These systems use advanced algorithms and machine learning models to analyze extensive data superficially. AI technologies like visual recognition help in the accurate identification of specific spare parts, preventing misidentification. Also, by automating the order processing, AI tools speed up fulfillment while ensuring efficiency and accuracy.
2. Cost Savings
Implementing AI in spare parts management helps OEMs in inventory optimization, enabling them to substantially save costs. AI systems can analyze historical data and current market trends to predict demand accurately, facilitating optimal inventory maintenance. This helps prevent overstocking, which incurs storage costs, and also understocking which leads to lost sales and customer dissatisfaction.
Additionally, AI-enabled automation smoothens labor-intensive processes like order processing and tracking. These tools also analyze equipment usage and wear patterns, facilitating predictive maintenance and reducing the risk of abrupt machine failures and costly downtimes.
3. Improved Customer Satisfaction
One of the primary goals of spare parts management for OEMs is achieving customer satisfaction. By ensuring faster and highly accurate order fulfillment, AI considerably enhances the customer experience. AI-enabled chatbots and virtual assistants provide 24/7 support and handle common queries like guides on order processes and real-time order status updates. Furthermore, AI streamlines processes like returned parts verification, processing refunds, and arranging replacements. This helps in better return handling, contributing further to enhanced customer satisfaction.
4. Data-Driven Decision Making
AI analyzes large volumes of data across sales trends, inventory levels, supplier performance, and customer preferences and facilitates OEMs with actionable insights. These insights enable managers to frame strategic decisions related to procurement, inventory management, and supply chain strategies.
For example, OEMs can identify parts with the highest demands in specific regions or seasons and plan stock accordingly. Additionally, AI can enhance predictive analysis to predict future challenges and opportunities, cultivating a more active and flexible supply chain.
5. Improved Operational Efficiency
AI-powered systems automate routine and repetitive tasks, allowing human resources to concentrate on more value-adding activities. AI handles several tasks like order entry, tracking, and elementary customer support, liberating employees to work on complex problem-solving and improvement strategies.
By guiding the choosing and packaging processes, AI also optimizes warehouse operations. This enables staff to locate and retrieve required parts efficiently. This enhances overall operational efficiency while also reducing the risk of workplace errors and accidents.
Implementing AI in Spare Parts Ordering and Fulfillment
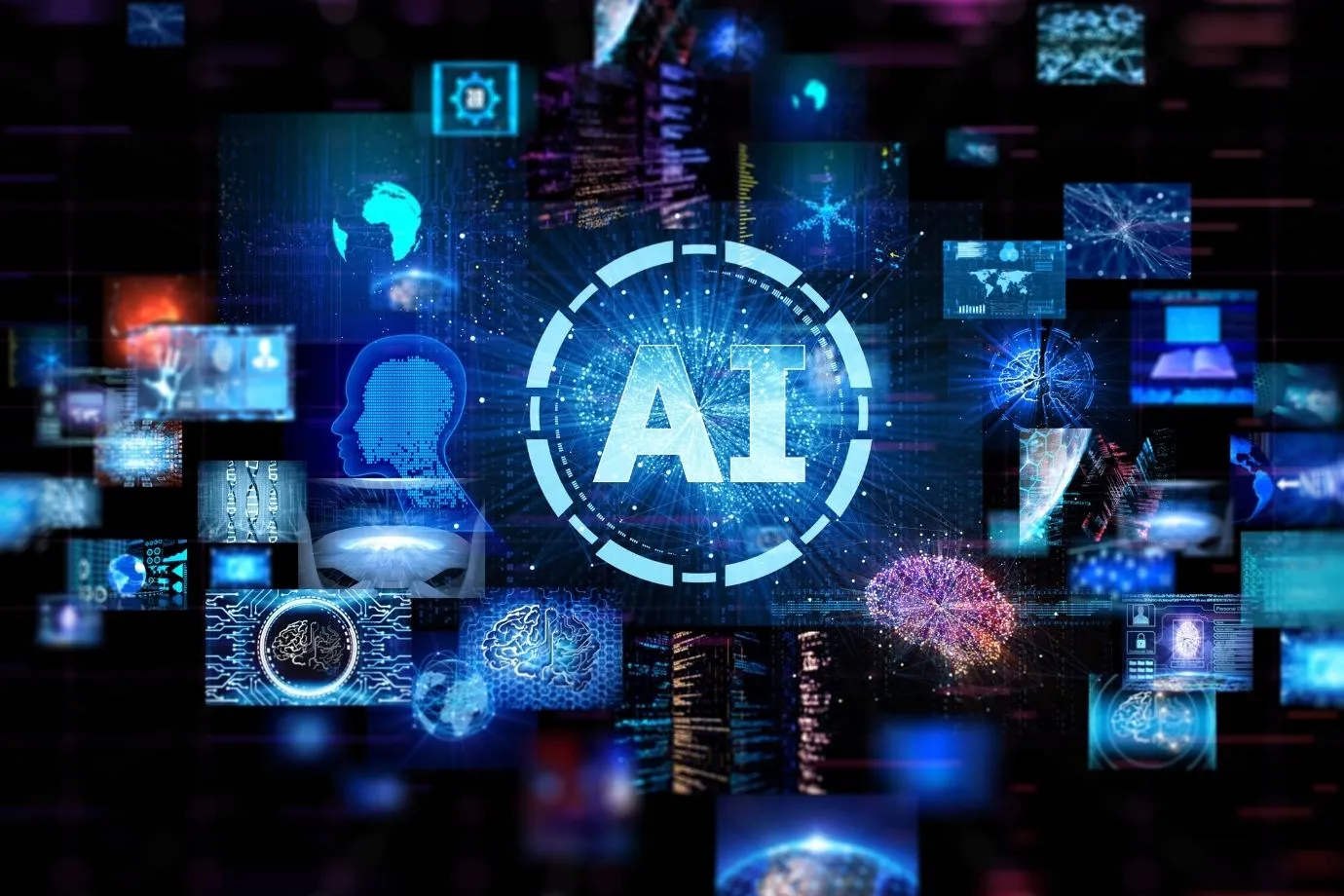
Considerable planning and strategic execution are crucial for OEMs when implementing AI for successful results. Adopting tactical and result-oriented measures helps streamline processes and achieve forecasted outcomes. Here are a few practices to consider for integrating AI effectively into spare parts ordering and fulfillment.
1. Conduct Data Audits
Access to high-quality data is the basis of implementing any successful AI tool. Without reliable and accurate data, AI systems cannot deliver accurate forecasts or actionable insights. This makes it crucial for OEMs to prioritize data integrity maintenance.
Conducting detailed data audits ensures its clarity, accuracy, and well-organized classification. This process involves identifying data sources, removing outdated or duplicate information, and checking for inconsistencies. Data audits also help OEMs discover gaps and shortcomings that may hamper AI performance.
To manage data effectively, establish clear governance policies, and organize data formats and collection methods. Furthermore, update and validate regularly to address any gaps or inconsistencies.
2. Invest in Employee Training
Before implementing AI into spare parts ordering and fulfillment, it's essential to transcend the basics of new technologies to your team members. OEMs should invest in employee training to ensure that their workforce adapts to changing workflows and can use these AI tools efficiently.
An effective training program will help educate employees about the benefits and capabilities of AI and provide hands-on training. It also offers continuous support and learning opportunities across the teams. Once your employees understand how AI can simplify their tasks, they are more likely to adopt and make the best use of this technology.
3. Choose the Right AI Solutions
Since each AI tool has its benefits, selecting the one that fits your requirements and solves your business’s unique problems is essential. Choosing the right solution requires a detailed understanding of your business goals and identifying technologies aligning with those needs.
To overcome operational disruptions, the chosen AI tool should allow seamless integration with your existing systems. Check for the following features when finalizing an AI solution:
- Scalability: Whether the solution can grow with your evolving business
- Compatibility: If the solution integrates with your current platforms and systems
- Flexibility: Does the software support customization for your unique business requirements?
- Vendor Support: If the provider offers enough technical support and guidance
Checking for these features helps OEMs choose the right AI tools and maximize returns on investment.
4. Start Small and Scale Gradually
While AI streamlines processes and enhances efficiency, its implementation on a large scale can be risky and overwhelming. OEMs should initially start with trial projects that allow testing AI solutions and gathering valuable insights. These small projects help in identifying potential challenges and improvement measures before escalating it widely.
To begin with, select a process to run the trial on. Once you draft the objective and success metrics of the project clearly, involve your team or stakeholders to gain practical insights and feedback. Starting small allows OEMs to refine AI strategies and identify their potential before scaling it across the organization.
5. Align AI Initiatives with Business Goals
To gain maximum benefits, ensure your AI implementations align with strategic business goals. This ensures AI initiatives contribute to OEM’s growth and efficiency directly. Begin by ensuring that AI projects address crucial business challenges and define Key Performance Indicators (KPIs) for each project. Based on performance, review and adapt AI strategies regularly to gain the best returns.
AI Capabilities in Intelli Catalog
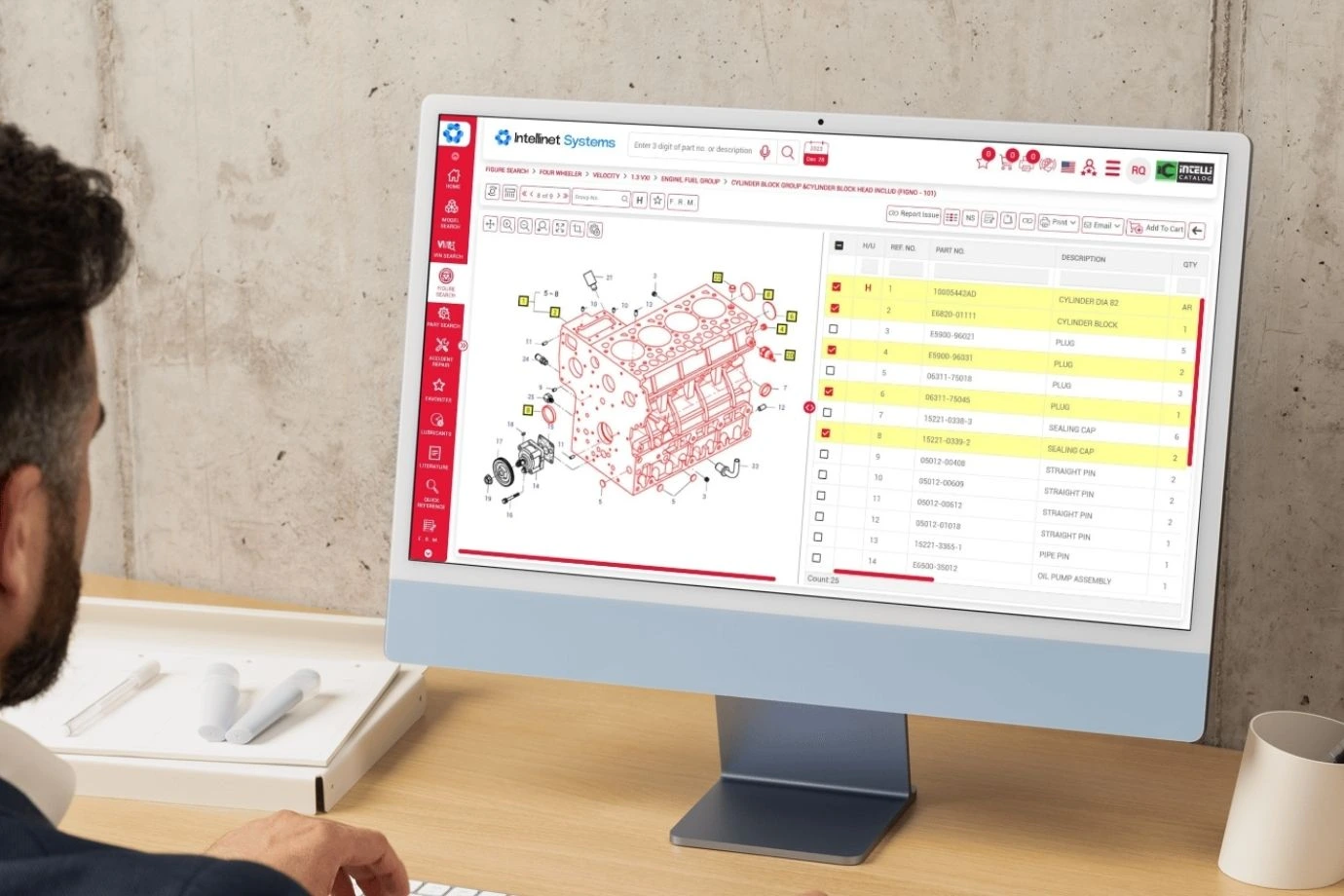
Intelli Catalog is a cutting-edge AI-powered platform developed to mutate how OEMs manage their spare parts inventory. Our platform leverages AI to enhance operational efficiency, optimize supply chain processes, and reduce costs. Here are the significant features that make the Intelli Catalog a requisite tool for OEMs:
1. Advanced Parts Identification
One of the significant features of Intelli Catalog is its capability to identify spare parts accurately and quickly. The platform uses modern image recognition technology to identify spare parts through uploaded images. It also utilizes natural language processing (NLP) to understand textual descriptions, enabling accurate and effective identification of even the complex components.
Intelli Catalog also offers an AI-enabled image-cleaning feature that helps OEMs clean poor-quality images. By significantly minimizing the time and effort involved in manual identification, Intelli Catalog helps OEMs maintain a continuous workflow.
2. AI-Driven Predictive Analytics
Intelli Catalog imparts AI-driven predictive analytics, providing OEMs with actionable insights into demand trends. Our platform analyzes historical data and current market patterns and generates forecasts on future demand for spare parts.
These insights allow OEMs to make data-informed decisions, preventing overstocking and understocking, and maintaining optimal inventory levels. This ability is crucial for businesses looking to enhance their overall inventory efficiency and cost management.
Takeaways
By enhancing efficiency, accuracy, and responsiveness, Artificial Intelligence is transforming the spare parts ordering and fulfillment process. Implementation of AI-driven technologies helps OEMs streamline operations, reduce errors, and optimize supply chain management. These advancements enable cost savings, help in data-based decision-making, and improve overall user experience.
For successful implementation of AI in spare parts ordering and fulfillment, OEMs should initiate descriptive content audits to ensure clear, usable, and accurate information. Employee training programs help the workforce to understand AI and its capabilities, enabling a smoother adaptation. Additionally, orienting AI advantage with broader business goals ensures the technology drives measurable and profitable results.
Cutting-edge platforms like Intelli Catalog demonstrate how AI can transform spare parts management by automating processes and improving user experiences. With the successful implementation of AI-driven solutions, OEMs can boost operational efficiency and address evolving customer demands. Adopting AI technologies and updating them regularly is crucial to streamlining spare parts management and staying ahead in the competitive market.
To learn more about how Intelli Catalog can fulfill your business needs or request a free demo, connect with us today.