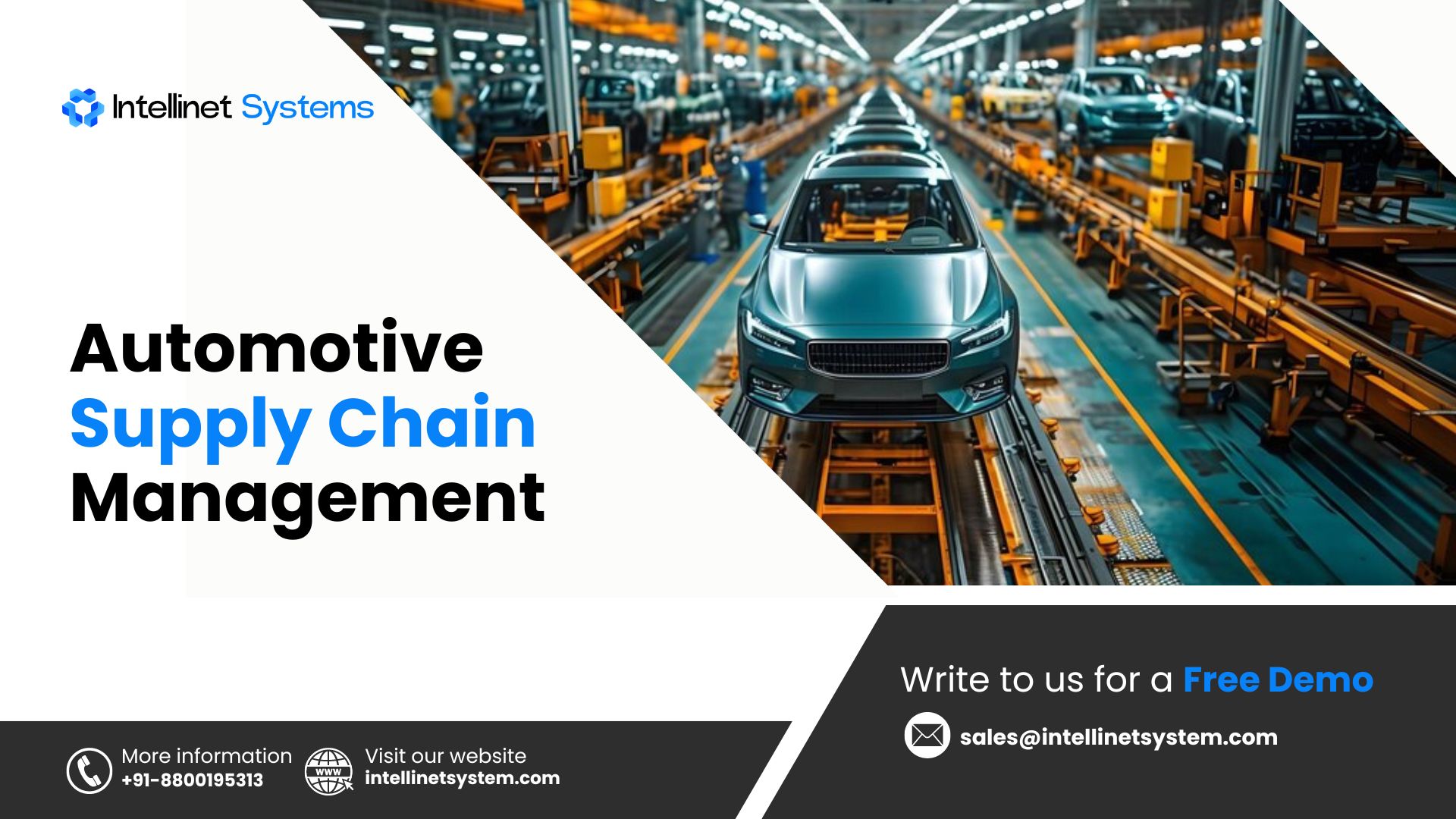
The automotive supply chain industry has seen significant development in terms of technology, demand, and global economic shifts. The automotive supply chain plays a crucial role in the whole dynamic of maintaining the flow of raw materials to manufacturers and the finished product to customers. This industry comes with its own challenges surrounding the transition from fuel to electric vehicles.
Despite the rapid changes in the economic factors associated with the industry, the automotive supply chain has adapted rather swiftly. In an ever-evolving world, change is the real constant, which is why supply chain management with the help of traditional methods is far too outdated. New technology in the industry has managed to change the dynamic of automotive supply chain management with AI, blockchain, and the Internet of Things (IoT).
These have not just been fancy words in the automotive industry but have managed to reshape the visibility, efficiency, and traceability of supply chains across the world. As the world of manufacturing transitions towards a more sustainable future, more electric vehicles are entering the market. The automotive industry has started utilizing eco-friendly and sustainable materials to minimize their carbon footprint.
This green transformation has pushed supply chain managers to change their strategies and ensure sustainability at every stage with minimal waste. In this blog, we will explore how the automotive supply chain industry has transitioned to this change, the different challenges they faced, and what the future of the industry looks like.
What is Automotive Supply Chain Management?
Supply Chain Management (SCM) is an umbrella term used to denote the process as well as the raw materials involved in creating a product (in this case, automotive) from scratch. Imagine building a car. The most basic raw materials, such as metal, rubber, plastic, etc., need to be extracted, processed, and molded before being assembled.
Each of these raw materials is sourced, processed, and assembled in different parts of the world and brought together to form the finished product. This process of keeping track of the raw materials, information, finances, and finally making sure all these arrive at the right time for assembly can be summed up as SCM.
The automotive supply chain is one of the most complex in all supply chains, as on average, the automotive industry must manage the supply and production of about 30,000 parts, including the tiniest of nuts and bolts. In the aftermarket, once the product reaches the customer, dealers usually have a hard time keeping track of parts and managing replacements.
Recognizing this gap in the market, several spare parts catalog software solutions were introduced to smooth out the process and improve efficiency between OEMs and dealers. The automotive supply chain, in simple terms, is like leading a parade, where coordination and timing can make or break the deal, and in this case, the overall production cost.
How Does An Automotive Supply Chain Management Function?
The sourcing of raw materials to the delivery of finished products is a long path with several steps:
- Sourcing raw materials
- Manufacturing of parts and components
- Assembly and production
- Quality control
- Distribution and logistics
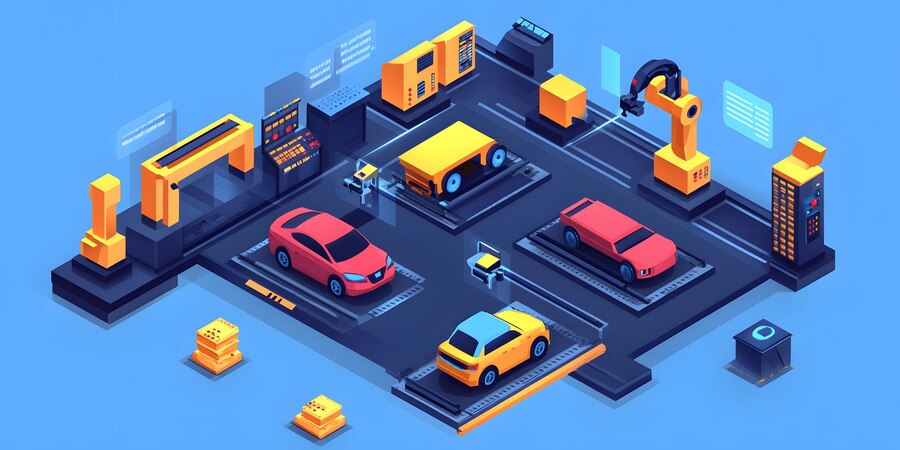
1. Sourcing Raw Materials
This is the foundational step in the automotive supply chain. It begins with the essential materials that are required for manufacturing different components. The most common raw materials include aluminum, plastic, glass, rubber, etc. The price, quality, and durability of these raw materials have a major effect on the overall efficiency of the supply chain.
Raw materials are sourced from around the world based on their availability; this step is crucial as the manufacturer must select the right supplier who meets their needs. Some of the basic requirements that every manufacturer has from their suppliers are the ability to provide the right quality, consistent delivery, timely shipment, and best pricing.
2. Manufacturing of Parts and Components
After the raw materials are sourced and ready, they are then transformed into the parts that are needed in the assembly. In this stage, the network of suppliers is categorized into three tiers. Each supplier carries out their production to fulfill the demands for parts ordered by the manufacturers.
a. Tier 1
Tier 1 suppliers are major players in the supply chain of the automotive industry, supplying directly to the original equipment manufacturers. These suppliers are primarily engaged in producing complex assemblies such as transmissions, braking systems, and engines.
In turn, such components imply complexity by nature and hence need close coordination between the Tier 1 suppliers and the concerned OEMs on minute details to reduce the chances of error in production.
The responsibility carried by Tier 1 suppliers is great in the sense that if this part of the component is flawed or late, it will significantly delay or hinder the production timeline—in essence, it might bring everything to a grinding halt. At this stage, the Tier 1 supplier is one of the largest enterprises that can handle a full-fledged quality control program.
The OEMs and Tier 1 suppliers are very collaborative, working together to improve efficiency and see where they can cut costs yet still turn out high-performance machines. This is a very important collaboration in the invention of reliable and powerful machinery; it allows room for continuous improvement and innovation within the automotive industry.
b. Tier 2
Tier 2 suppliers form the backbone of any automotive supply chain since they supply the subassemblies necessary to Tier 1 suppliers for making complex systems. Such subassemblies would include electronic modules and precision-machined parts at the high end and simple screw-nut bolts at the bottom.
Given the diversity and specialty of such components, it is quite common for Tier 1 suppliers to work with numerous Tier 2 suppliers to meet their diversified requirements. The Tier 2 suppliers themselves are highly specialized in the parts they make, which allows them to produce high-quality parts at quite competitive prices.
Even though they never deal directly with any of the car OEMs, they are still very important for the production process. Their main objective is to supply parts that meet all the requirements and specifications that Tier 1 suppliers have bottled up.
What is expected of the Tier 2 supplier is to have quality and production standards, as even a trace defect may introduce discrete changes in performance and reliability in the product. Top-tier quality should be ensured in their components, as any fault at this level might have a snowball effect through the automotive supply chain and ultimately affect the end consumer.
c. Tier 3
This tier acts as the foundation of the supply chain, providing the raw materials necessary for the rest of the tiers to function properly. They might operate far away from the finished product, but they are not irrelevant; on the contrary, they are key players because they provide the very basis required for production.
The usual raw materials supplied include metals, plastics, rubber, and any other important substances. The main objective of the Tier 3 suppliers is to process these raw materials in bulk, keeping the processes cost-effective while maintaining quality standards.
Their operations include chemical processing, mining, and material refining, depending on the state in which the materials are extracted or used. For example, a Tier 3 supplier may produce steel that is delivered to a Tier 2 supplier, who fabricates formation components like gears or bolts from the steel supplied by the Tier 3 supplier.
Clearly, these kinds of raw materials are fundamental to the product not being compromised in terms of quality, so it is important that Tier 3 suppliers develop their production lines to extremely high standards. These defects at this stage will have a cascading effect on the whole automotive supply chain, which could severely impact the performance and reliability of the product.
Responsibilities in inventory management and demand fulfillment are also vast for the supply base of Tier 3 suppliers.
3. Assembly and Production
As the name suggests, it is where different parts are assembled and form the finished product. These parts are assembled in large manufacturing plants that are operated and run by OEMs. The process of assembly is crucial and is followed sequentially to minimize error or damage.
The initial step is the construction of the outer body of an automobile, where large metal pieces are welded together to form the basic outer structure. After this, the outer shell of the vehicle is moved to different stations within the plant, where different components are then welded in. Each part, including the engine, transmission, suspension, glass, seats, and other interiors, is placed and secured.
Every station included in the line of assembly has a specialized robot that performs the set tasks assigned to it. Most manufacturers follow just-in-time (JIT) manufacturing, where the part is created or ordered only when it is needed. With the help of the JIT method, most manufacturers cut down on inventory costs without disrupting the supply chain cycle.
Although this method sounds perfect in textbooks, it comes with its challenges, such as the fact that every part needs to be created and delivered with perfect coordination, as even the slightest delay can put the whole process on hold, resulting in a delay and unnecessary increase in cost.
Every step of assembly is coordinated with a quality check to ensure that only top-quality products reach the dealers or other tier manufacturers. The quality check includes minimizing energy consumption at every stage.
4. Quality Control
Quality is to be ensured, and all the products are subjected to vigorous testing for damages before they hit the market. Many tests and inspection processes are conducted in the production phase to ensure the reliability and durability of every element produced.
The stages of inspection start with the parts arriving from multiple suppliers before being assembled. Every detail, however small, is checked for quality, and the ones with minute defects or inconsistencies are rejected, fixed, or changed completely.
During manufacture, at each point of assembly, there are several tests that the product goes through, including checks for the alignment of various parts, evaluation of the strength or endurance of welds, and testing of electronics.
The last testing is done after the assembly of the whole product, which involves both static and dynamic assessments. These are very significant certifications for reliability in the automotive supply chain industry. Static testing involves the appearance of the vehicle, its finish, functionality, lighting, etc.
Dynamic testing, on the other hand, tests the vehicle for the worst possible real-life situations. Testing a vehicle in extreme temperatures, humidity, rain, etc. is also part of it. It also includes the testing of the engine, brakes, suspension, wheel alignment, steering, and transmission.
The manufacturers test and audit everything at all stages to ensure quality is maintained. Should any quality issue be raised on such checks, the whole batch may be subjected to fixing, replacement, or rejection. These instances are highly prioritized since a faulty product will reflect negatively if it finds its way into the market. A faulty product poses severe threats to customer safety and the company's reputation, which directly affect trust and reliability.
The critical test at this stage would be crashworthiness. Several crash tests would be conducted to ensure the vehicle could withstand bad accidents and protect passengers with the least damage. It would include airbags, brakes, seat belts, and other safety features.
Reliability and safety are key differentiators in the highly competitive market for consumers in the automotive supply chain industry. It can also be seen that brand reputation is important; firms that are older in the industry are treated with more trust.
5. Distribution and Logistics
This is the final stage of any supply chain, where finished products are handed over from manufacturing plants to dealers. This is initiated after the product has passed through quality checks successfully. The condition in which the products arrive at dealerships is as important as this stage.
The condition of the products on delivery, the time taken, and the amount of damage should be as low as possible. In this phase, the manufacturers, in collaboration with the dealers, find the shortest and most effective routes to transport the vehicles.
Depending on the destination for delivery, there is sea, truck, and even train transportation for the vehicles. Among the major challenges of logistics in the automotive industry is the demand for and transport of vehicles.
There must be a proper coordination and management system to decrease the delivery time. It also facilitates the tracking of every shipment with the help of real-time tracking systems and manages the vehicle flow as well.
There is always some risk associated with the transportation of vehicles to dealerships due to the chances of damage, accidents, and even theft. Due to the involved risks, special vehicles and loading methods are used to minimize the potential damage.
These precautions are further supported by regular inspections of the vehicles to ensure that they are in the best condition when they reach their destination and provide the best experience to the customers.
Also important is compliance with each country's import regulations. This means shipments are subject to all rules and regulations governing the shipment to avoid delays or problems in delivery.
Trends in the Automotive Supply Chain
- Reshoring
- More transparency
- Shift to EVs
- Sustainable measures
- Autonomous vehicles
- Risk management and resilience
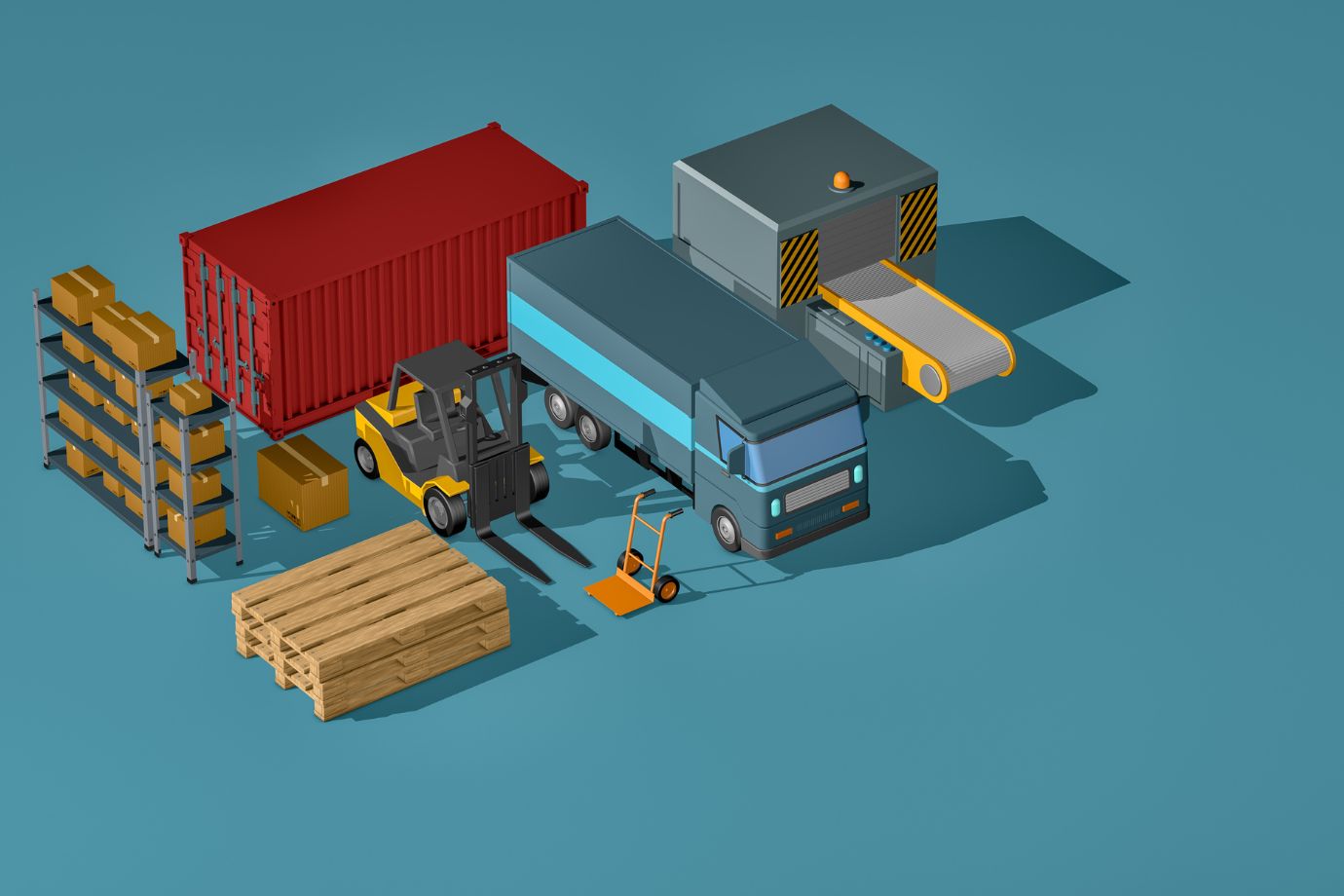
1. Reshoring: Strengthening OEMs
This minimizes dependence on external offshore-based suppliers, largely enhancing resilience in supply chains. The global pandemic has exposed the vulnerabilities and dependencies that exist within the automotive industry with respect to overseas production.
This disruption pointed to the need for reshoring, which became a solution. Reshoring not only shortens the supply chain, but manufacturers are also able to strengthen quality controls over their products. Hence, it paved the way for more effective SCM and created more jobs within domestic markets. Besides, reshoring contributes to the reduction of carbon emissions associated with long-distance transportation.
2. Better Transparency in the Automotive Supply Chain
In recent years, the automotive industry has become more and more transparent about its supply chains and manufacturing processes, as they have major environmental effects. It has not only reduced the impact on the environment but also given manufacturers a chance to be more mindful of their production processes. Here are some benefits of how transparency has been a great trend in the automotive supply chain.
- Changed Reputation: Customers tend to trust more transparent companies as they find them more reliable.
- Risk Mitigation: Violations, supply chain disruptions, and any unwanted instances can be easily foreseen and taken care of.
- Increased Efficiency: With a better understanding of the supply chain, different companies can implement measures to improve their production, decrease time, and save on production costs.
- Improved Quality: With transparency, companies can ensure that their products are of top quality and are produced in the most efficient manner.
- Accountability: companies that are more transparent are considered more accountable since they have nothing to hide. It comes with the belief that the methods followed in the manufacturing of their product are completely safe and ethical.
3. Shift to Electrical Vehicles (EVs)
The shift to internal combustion engines in electric vehicles has reduced ecological impact but posed other problems for automotive supply chains across the world. The most obvious difference between EVs and traditional ICE vehicles is that they are equipped with an electric motor and a battery rather than a conventional engine.
This changes the nature of the components used and the sourcing partners. This brings along the problem related to the procurement of new raw materials like lithium, nickel, and cobalt. Many companies have allied themselves with mining companies to secure a stable supply of these raw materials.
With these batteries, new logistical problems have been created. These batteries are fragile and dangerous to handle, so they require special handling when being transported. Safe disposal and recycling of components like the one in question have become an even more serious problem with an ever-growing demand for EVs.
4. Sustainable Measures
Resource efficiency was always pursued, and waste was suppressed in every way possible in the history of the automotive industry. Material sourcing observes environmentally responsible methods—from metal and plastic to rare earth elements.
Today, to significantly reduce their carbon footprints and engage in sustainable practices, manufacturers have become increasingly dependent on suppliers. In addition, manufacturers are going to be more sustainable by operating with suppliers who are geographically closer to the manufacturing facilities. This will help in cutting down on carbon emissions used in transporting raw materials and components without disrupting the automotive supply chain.
5. Autonomous Vehicles
The advent of autonomous vehicles brought about a new evolutionary avenue for the automotive industry. Just as electric vehicles impose several needs and add complexities that are not well extrapolated from conventional models, so do autonomous vehicles.
Unlike conventional vehicles and EVs, AVs are built from exacting parts, including sensors, radar, cameras, LiDAR, and high-end computing performance. These components are essential for the various functionalities executed by the AVs, which help in allowing the decisions and control systems of the vehicle to be based on the data they collect.
Apart from physical components, AVs also rely heavily on complex software elements that collect and analyze real-time data to control the vehicle's functions. This reliance on software has given birth to collaborations between automobile companies and software development corporations.
The integration of software into AVs has equally amplified the importance of cybersecurity, considering the sensitivity of the information that must remain confidential and the regular updates that the software must have to ensure accurate performance of the cyber-physical AV system.
The advent of technology, coupled with the rise of autonomous vehicles in the automotive supply chain, has moved the industry from peaceably mechanical to one highly entwined with advanced software and digital innovation.
6. Risk Management and Resilience
In recent years, manufacturing companies have come up with many effective ways of managing risk. With the active entrance of technology into the automobile industry, potential risk and damage prediction can be made efficiently. Many firms can be saved from the possible disruption and financial loss just in time.
This has resulted in efficient performance. The manufacturer companies have taken several measures, like relocating the manufacturing plants, that reduce the overall cost of transportation. The companies have invested a lot in manufacturing flexibility.
With new guidelines and developments coming into the market every day, this opens up room for rapid changes. These changes can be brought into manufacturing as well as the aftermarket with the help of modern software in accordance with the changing market.
Aftermarket Trends in the Automotive Supply Chain
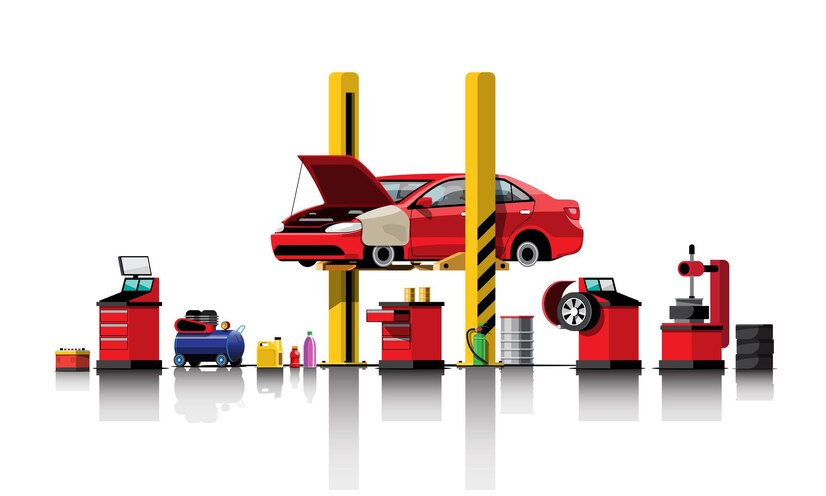
The aftermarket is a large industry, especially for the automotive industry, as automobiles have thousands of spare parts. Here are different trends in the aftermarket of the automotive supply chain industry:
1. Increased Digitization and E-Commerce
With more and more industries shifting to the online market, there has been a growing demand for efficient online software. Companies are investing in software for different tasks to meet the demand and supply of the aftermarket industry. With the help of aftermarket software solutions, dealers and OEMs can conveniently manage their databases.
2. Importance of Sustainability
Regulatory bodies have strict policies when it comes to sustainability. Companies are trying to reduce their carbon footprint to their full potential by implementing efficient programs. One such important step is refurbishing old or faulty parts, repairing them, and reselling them to reduce waste.
3. Adapting Advanced Technological Solutions
The aftermarket supply chain has been increasingly changing with trends and adopting new ways. AI, IoT, and blockchain have been a highlight of this change, helping in manufacturing and dealing roles. These new and advanced technological changes are helping the aftermarket supply chain by increasing efficiency and reducing time and errors.
4. Focus on Customer Satisfaction
Customer experience has always been a top priority in the industry, but with digitization, businesses are now focusing on customer retention. This includes how customers are catered to for after-sales support and in terms of flexible deliveries. A dedicated focus on customer experience does not just create customer loyalty but also helps in adapting to the ever-changing market.
What Is the Future of Automotive Supply Chain Management?
That advanced technology in the automobile industry, with a new arrival in the form of AI, is a very good change that has been taking place. It prepares the industry for further change and more change as it weathers the sea change from EVs into AVs.
Traditional methods are being replaced with technology-driven approaches that are a sure-shot way of changing the face of supply chain management. Today, an overwhelming majority of manufacturers are increasingly shifting back or reshoring to reduce carbon footprints by reducing the number of offshore suppliers and, in turn, simplifying the processes to become more efficient.
The future of automotive supply chain management, therefore, is marked by innovations, sustainability, and resilience. With the fast-changing nature of the industry due to rapid technological changes, the only plausible scenario for more changes is when technology rules our lives in every way.
That technology affects the employment standings in any industry is, for all practical purposes, a truism, though one would have to admit it holds out to be devastatingly accurate and efficient. AI, blockchain, and IoT—all these technologies are changing the industry from its status to one with sustainability at its core.
Software applications going beyond the traditional functionality of spare parts inventory control help OEMs increase their logistical efficiency. To learn more about how OEMs smoothly carry out their aftermarket operations, book a free demo today!