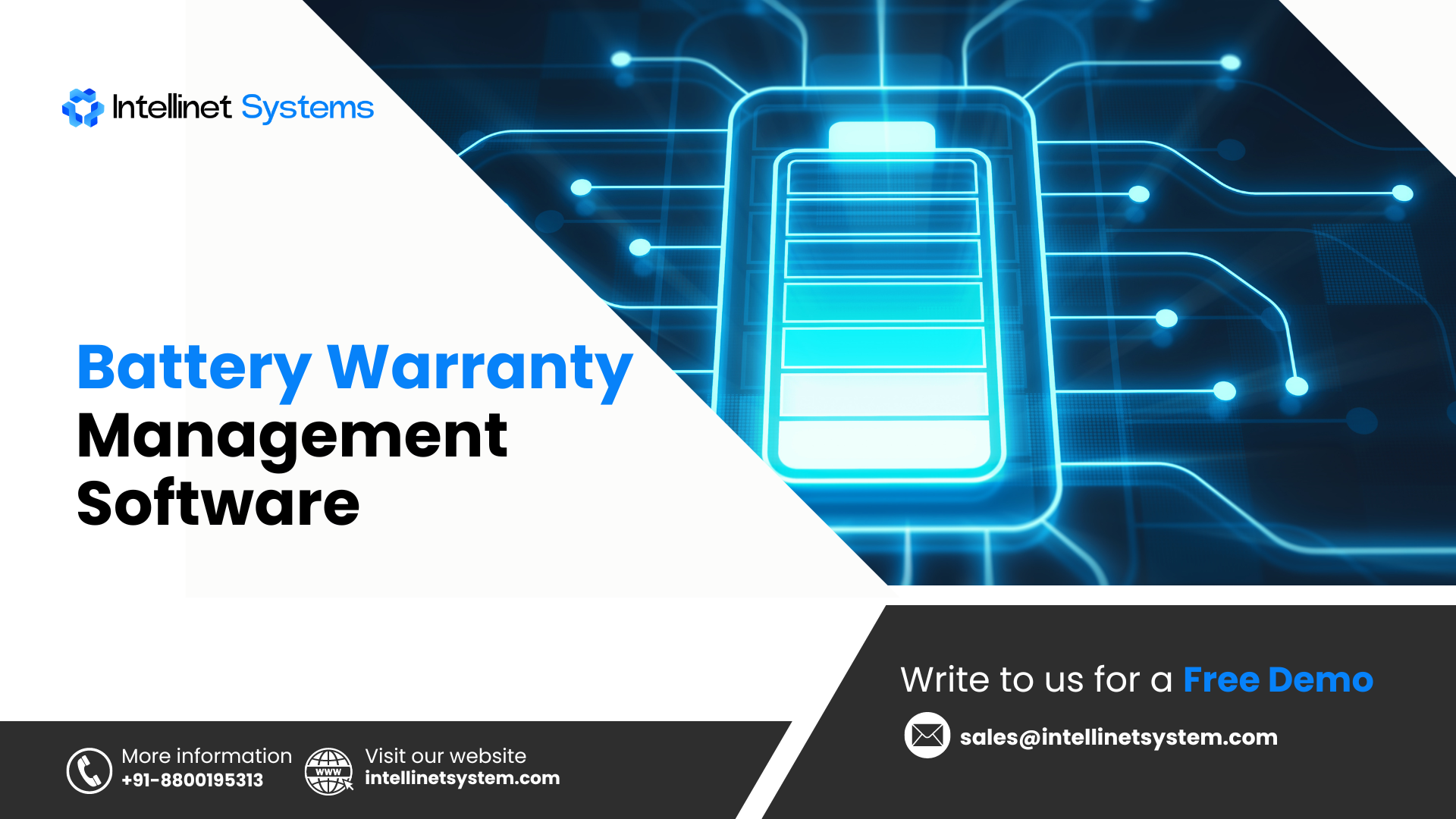
Every year, small-scale manufacturers tend to lose a major share of their investments in managing warranty claims and ensuring customer satisfaction. As small-scale manufacturers function on a small profit margin and, in most cases, no profit at all, they face warranty fraud. With the introduction of battery warranty management software, small-scale battery manufacturers, and most EV manufacturers, can streamline their warranty claim process and save time and cost accordingly.
In today’s fast-paced, ever-evolving world, it is essential to maintain a smooth warranty management system to win the trust of existing customers. As the world is transitioning towards a digital era with everything electric, batteries will always be in demand. Hence, ensuring customer retention becomes paramount.
Through this blog, let us understand the process of battery warranty management, the challenges faced by small-scale manufacturers, and understand why warranty management software is essential.
What is the Process of Battery Warranty Management?
Every manufacturer has different terms, coverage options, and warranty features for different components. Keeping accurate and real-time documentation of each part is a tiring and time-taking process. With limited resources and an underdeveloped working structure, chances of error and mismanagement are high. Let us understand the process of battery warranty management.
- Warranty Registration
- Stock-In
- Stock-Out
- Dealer Claim Process
- Claim Review
- RMA Initiated if Opted
1. Warranty Registration
When a product is sold, the customer can easily register the product and its components through the website or a physical card. Different components of a product have different sets of rules and specifications for warranty periods. Such is the case for batteries, where different manufacturers have different warranty guidelines for batteries.
In the warranty registration stage, the customer is made aware of the different parameters of the warranty. This includes the duration, the different parts that are covered, and what kind of damages or defects are not included in the warranty.
2. Stock-In
After a warranty claim has been registered, the defective battery is sent back to the manufacturer. After it is received, it is stocked. Through this process, the returned battery and the claim are verified by the manufacturer through the registered serial number, most often created by the battery warranty management software, along with the details of the purchase.
After verification, the same battery is tested for any existing faults, defects, and performance delays that could be the cause of the issue. During this process, it is also necessary to check that the defect comes under the warranty terms.
3. Stock-Out
After the claim is checked and validated, it is either replaced or repaired. The repaired or new battery is prepared for dispatch along with proper packaging to ensure safe transportation and meet industry standards. The required logistics are then arranged for safe transportation, and it is then shipped to either the customer directly or to the dealership.
4. Dealer Claim Process
After the problem is diagnosed and confirmed, the required documentation is completed along with proof, and a claim is raised with the manufacturer through a common portal. This claim consists of all the essential details of the defect or fault along with proof for complete transparency. The defective battery is then checked according to the claim and is then sent back to the OEM for further processing.
5. Claim Review
a. If the Claim Is Accepted: If the claim is accepted by the OEM, the dealership is credited with a replacement of the product, the repair cost is covered by the OEM, or equivalent credit is issued.
b. If the Claim Is Rejected: An inspection is conducted post-the claim, and if the claim is not coinciding with the issue, then the claim is rejected along with the reason.
6. RMA Initiated if Opted
After a claim is submitted, a (Return Merchandise Authorization) RMA is automatically generated by the warranty management software for returning the part to the OEM warehouse. After this, further processing of the warranty request begins.
What Are The Challenges Faced by Manufacturers in Battery Warranty Claim Management?
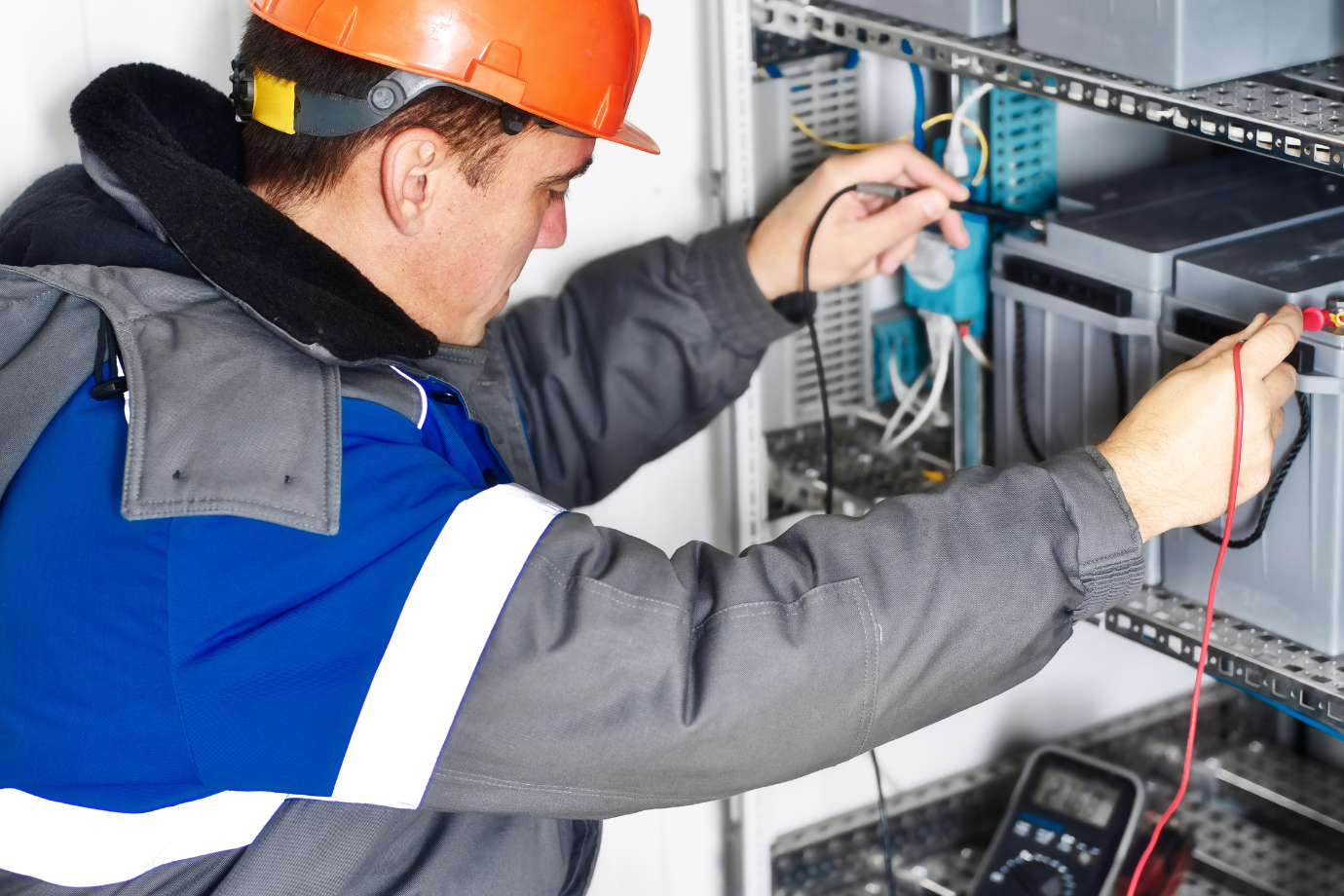
- Claims Falling Through Cracks
- Recurring Issues Going Unrecognized
- Controlling Cost And Mismanagement
- Limited Resources
- Warranty Fraud
1. Claims Falling Through Cracks
The warranty management process highly influences customer services and brand reputation. Most OEMs with small-scale businesses struggle to provide the best services to their customers with their warranty claims due to a lack of resources. As customer service is all about constant communication and coordination of the team, small-scale businesses are usually left behind due to limited staff in each department.
If the dealership does not respond within a stipulated time with a valid explanation regarding the claim, the customer experience will be hampered. During the process of getting connected with customer representatives and getting a convincing response to their warranty claim, the customer tends to get bitter. If the response is not timely, the claim is likely to get misplaced or delayed through different departments and eventually not get updated at all.
In such cases, the customer has to speak to different representatives every time they call and start with their problem all over again. In such situations, the claim tends to fall through the cracks and never make it to the customer. Hence affecting customer retention.
2. Recurring Issues Going Unrecognized
More and more companies are now investing in battery warranty management software and means to streamline their process of recognizing recurring issues. Multiple companies and manufacturers face similar issues time and again due to the absence of a standard operating procedure. Most manufacturers invest in the wrong software or tools that do not accurately identify the cracks and are often met with heavy losses.
This not only drains the revenue of the company but also damages customer retention in the aftermarket. The aftermarket industry is much more than just a service industry today and has transitioned into a revenue-generating industry. To stay relevant in this industry, businesses must invest in efficient software that can browse through large amounts of data and recognize patterns to contribute to making informed decisions.
3. Controlling Cost and Mismanagement
In well-established companies, there are dedicated teams taking care of the warranty management system and ensuring that nothing is missed or delayed. Small and midsize manufacturers lack an automated system, due to which frequent disruptions in the supply chain and frequent financial strain are common.
Without a standard process in place, low-quality or defective batteries may make it to the market and affect brand reputation, leading to expensive warranty claims. Small manufacturers have to tackle this issue along with the expectation of meeting the demands of the market and compliance standards. This negatively impacts the sustainability of the small-scale battery manufacturer.
4. Limited Resources
Inefficient stock management, delays in processing claims, frequent disputes, and increased warranty costs are some of the challenges faced by small and medium-sized battery manufacturers. The majority of these challenges originate due to a lack of resources and a trained team.
Inefficient inspections of returned batteries result in higher claim disputes and incorrect diagnoses. These are some of the challenges that battery manufacturers have to face due to manual operations and following traditional methods of warranty management.
5. Warranty Fraud
Another major crack in the battery warranty management process is warranty fraud that goes undetected. There are frequent instances and chances of fraud warranty claims from customers or dealerships, blaming the product for being faulty or defective. Whereas the true damage is caused by the user. In such cases, efficient software is essential to be able to detect any traces of tampering with the product to get accurate data of what exactly went wrong.
Most small-scale battery manufacturers have limited resources and are unable to do so, due to which they tend to lose huge amounts of money repeatedly. Frequent battery claims can tamper with the trust of the customers and eventually affect the future sales of the company.
Now that we understand the process of battery warranty management, and the challenges faced by medium, and small-scale manufacturers, let us understand how warranty management software Intelli Warranty Lite solves these gaps in the aftermarket.
Importance of Battery Warranty Claim Management Software
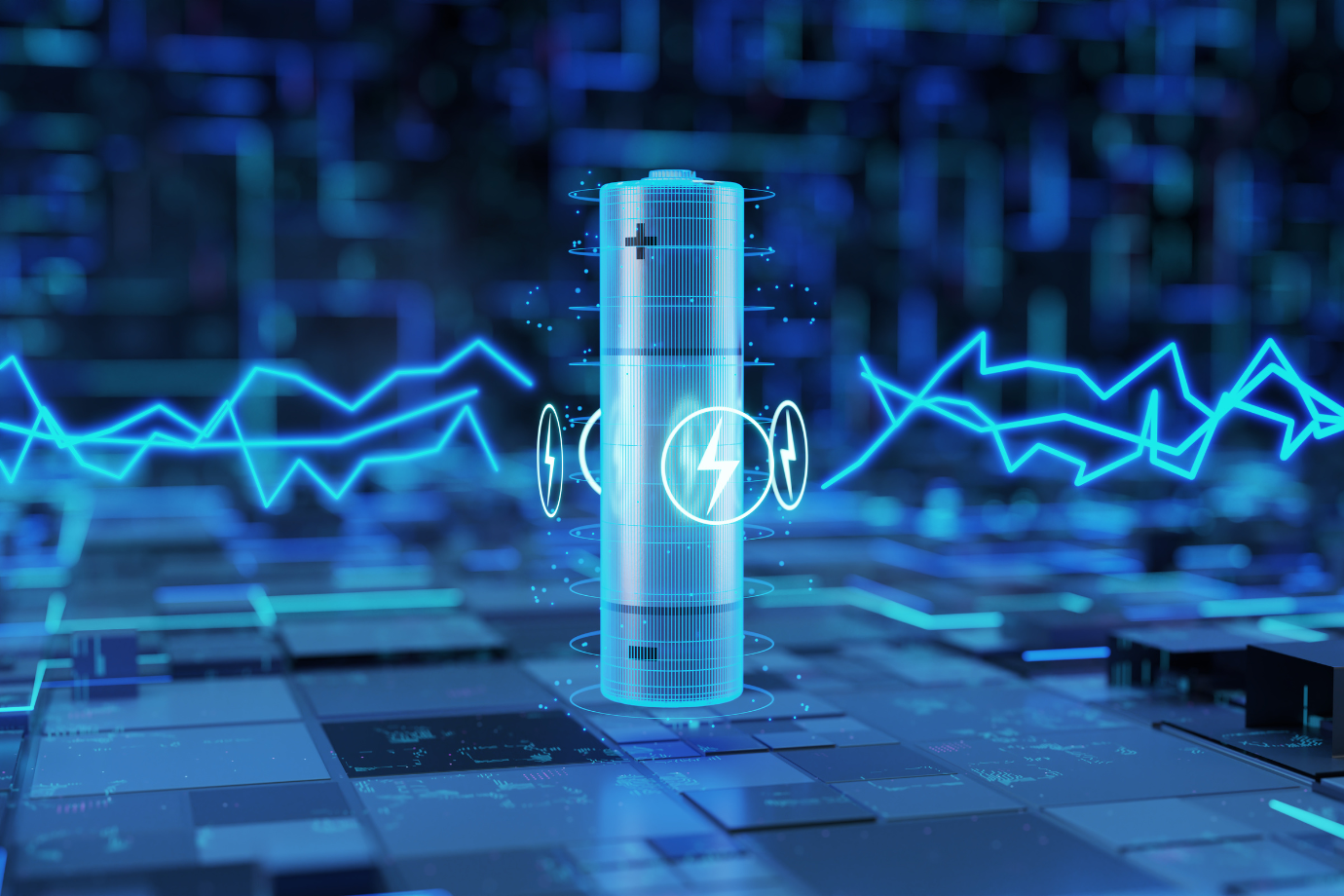
Intelli Warranty Lite is an efficient and economical warranty claim management system customized for midsize and small-size manufacturers. It ensures that the warranty lifecycle from claim submission, warranty registration, and customer satisfaction to replacement or reimbursement is conducted smoothly without error.
1. Policy Administration & Configuration
This feature increases flexibility in defining the parts, component coverage, payment reimbursement terms, warranty terms, and other policy-related parameters. This makes the process of administration and configuration simpler and more systematic, therefore minimizing error.
2. Efficient Claim Process for Dealers
This feature enables manufacturers to streamline the claim process for dealers with options such as readymade templates for claim creation, uploading supporting documents, validation checks, and integrating various systems.
3. Multiple Claim Types
The software allows manufacturers to integrate any type of claim format, including OEM PDI, Post-Sale, Campaign, Good Will, Spare Parts, and Dealer PDI. This accurately addresses the need for warranty management effectively.
4. Multi-Channel Reporting
The software provides the convenience of reporting and communicating through multiple languages in any format including Excel, PDF, and Microsoft SSRS. This enables efficient data analysis and representation between teams operating from different parts of the world.
5. Parts Management and Integration
It integrates easily with SAP and other systems that maintain parts prices and information related to supplier information. It also facilitates seamless validation through EPC integration.
6. Claim Administration with Audit Trail
It maintains transparency throughout the claim process along with an audit trail, auto-approval, and partial approval based on flexibility for better currency management.
7. Barcode and Serial Number Generation
There are multiple cases where certain parts do not have serial numbers of their own. Smart warranty management software usually has an inbuilt feature where the dealership can generate a serial number and barcode.
8. Work Que, Campaign, and User Management
Warranty management software supports a variety of claim types, such as OEM PDI, Dealer PDI, Post-Sale, Campaign, Good Will, and Spare Parts. Through this, the software ensures to address the diverse needs of warranty management.
9. Easy Accessibility
Warranty management software today has great accessibility across various electronic devices for maximum convenience, including native Android, native iOS, and other web platforms.
Conclusion
Manufacturers are shifting towards a future with maximum technological integration, this will not only shape the manufacturing industry but will also improve the customer experience. The traditional methods of warranty management were chaotic and had multiple cracks in them, which made it inefficient in the long run. The manual methods in the past did not just cost the manufacturers more money and time but also hampered the reputation of the company.
Constantly losing loyal customers over warranty disputes costs midsize and small-size manufacturers more than their profits. Eventually, small-scale battery manufacturers integrated efficient battery warranty management software into their operation process. With real-time data, identification of warranty fraud, and a streamlined approach for addressing warranty claims and supplier recovery, it becomes a lot easier for OEMs to channel their investments toward the growth of the company.
To know more about Intelli Warranty Lite and its features, get in touch with us today and receive a free demo!