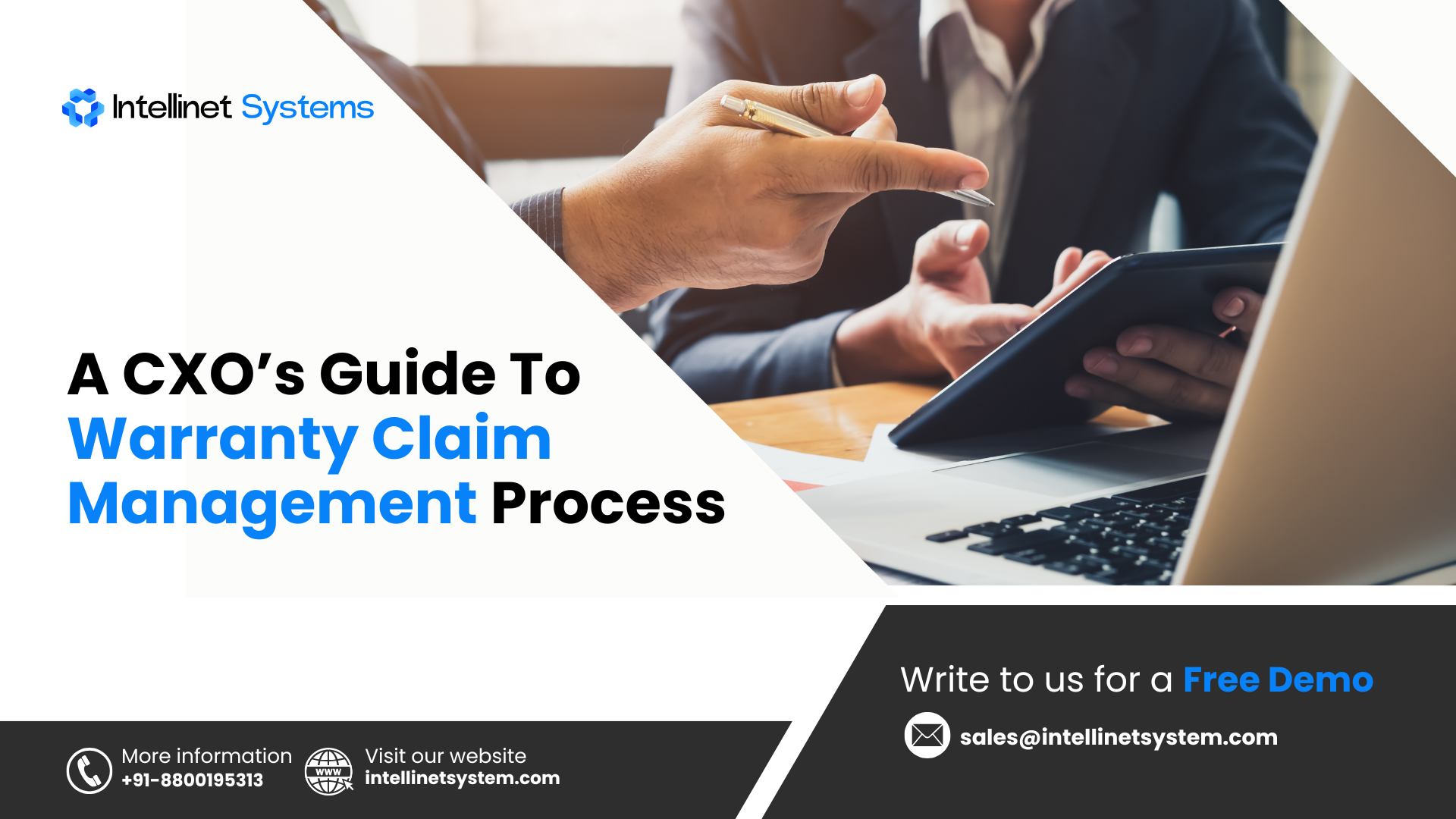
An inefficient warranty claim process can drain up to 3% of a company’s expected revenue. This is why warranty claim management is an unavoidable part of the job for CXOs of different manufacturing companies. This money can be better utilized for innovation, growth, and expansion.
Poor warranty management is associated with several other challenges, including financial drain and poor brand image. In this blog, we will analyze the role of CXOs of manufacturing industries in warranty management, the challenges present in the market, and why warranty management is the need of the hour.
Why Warranty Claims Management Should Be Prioritized by CXOs
- Increasing Complexity of Equipment
- Competition
- Product Improvement Through Data Insights
- Risk Management & Financial Impact
1. Increasing Complexity of Equipment
Traditional warranty management systems took a toll when manufacturing industries merged with the latest technology and changed the warranty curve of different equipment and parts. This added to the number of parts and increased the risk of manufacturing defects, malfunctions, and even design inefficiency.
As the parts became more advanced, single parts required sourcing from multiple suppliers which further complicated the process of warranty management. Software and manufacturing companies’ collaboration has triggered more warranty claims as software needs more maintenance and has a higher chance of malfunctioning than mechanical parts.
CXOs who have evolved through the transition have adopted automation and predictive analysis to forecast upcoming repairs and often prevent costly mishaps. Keeping warranty management as a priority has resulted in a drastic reduction in the cost associated with frequent repairs and prevented any uncalled damage.
2. Competition
CXO possesses the power to turn warranty management into a strategic advantage for their company by proactively addressing potential product failures. When a product tends to malfunction, the manufacturer or the dealership is expected to swiftly take over the matter reducing the downtime and inefficiencies experienced by the customer.
This ensures that the customer continues to trust the services of the OEM and fosters long-term loyalty. Real-time response to warranty products, along with diagnosis and substantial updates in the design and model, ensures that the product does not face the same issues again.
3. Product Improvement Through Data Insights
Every warranty claim contains unique information about a product’s reason for failure which can be used as an insight for improving future products. With this information, OEMs can efficiently track the issue back to the manufacturer, supplier, production process, or the specific components that resulted in recurring issues. By reclaiming the parts returned under warranty, CXOs can efficiently inspect the part and re-engineer or change the methods to make product quality better and reduce future losses.
4. Risk Management & Financial Impact
Risk Management is crucial for CXOs as warranty claims tend to directly affect the reputation of the company. When a particular component shows consistent complaints or defects it is essential to analyze the root cause through emerging patterns and improve the quality of the product. Efficient warranty management ensures compliance with the changing regulatory standards. This helps manufacturers avoid fines and legal risks associated with non-compliance.
Common Challenges in Warranty Claims Management
1. High Operational Cost Due to Inefficient Process
Operational costs have always been at the top of the list of challenges faced by CXOs during warranty claim management. Manual data entry, inefficient processes, the absence of automation, and cracks in the system lead to claims being lost in the process.
Manufacturers often lose more money due to additional administrative tasks, delays in resolution, and high labor costs. The process's high dependence on manual tasks often increases the chances of error and leads to escalation, costing the manufacturer more money.
2. Complexity In Handling Multiple Products and Regions
In the manufacturing industry, navigating and keeping track of warranty claims processes for multiple products across multiple regions has always been a significant challenge for CXOs. Having standardized policies for all equipment is often difficult as different parts have unique warranty terms, compliance requirements, and regulations specific to regions.
The lack of a systematic process for addressing warranty claims often affects the reputation of the company due to high processing time, lack of coordination between different departments, and low customer satisfaction. Companies spread across different regions of the world always pose a threat exposing the business to potential legal risks along with fines.
3. Inaccessible and Inconsistent Data
Warranty information is often buried in documentation with different departments which makes it challenging for other departments to access. Recent market surveys suggest that inaccessible data management costs manufacturers millions of dollars. The circulation of inconsistent data across different departments tends to cause inaccuracy in the resolution of the claim and affects customer satisfaction.
CXOs have to ensure the accuracy of data along with updated information to decrease errors, and potential delays in the claim process. In circumstances where a team cannot access important information, there is a major chance of confusion and inaccuracy.
4. Identifying and Preventing Fraud Claims
Manufacturers and businesses still choose to rely on traditional methods of warranty claim management. The traditional methods of managing warranty claim fraud include inefficiency, lack of automation, or fraud detection.
Such cracks in the traditional system of warranty claim management pose a major challenge for CXOs to keep up in the market. CXOs need to proactively find an innovative solution that accommodates all the manufacturer’s unique needs into a single solution.
5. High Chances of Human Error
When warranty claims are manually handled and maintained, there is a high chance of human error. Data entry, assessment of claims, and updating the information manually are some of the challenges that CXOs in manufacturing have to actively solve. When claims are mishandled at the early stage, all other processes associated with warranty management are delayed.
Key Strategies to Improve Warranty Claims Management Process
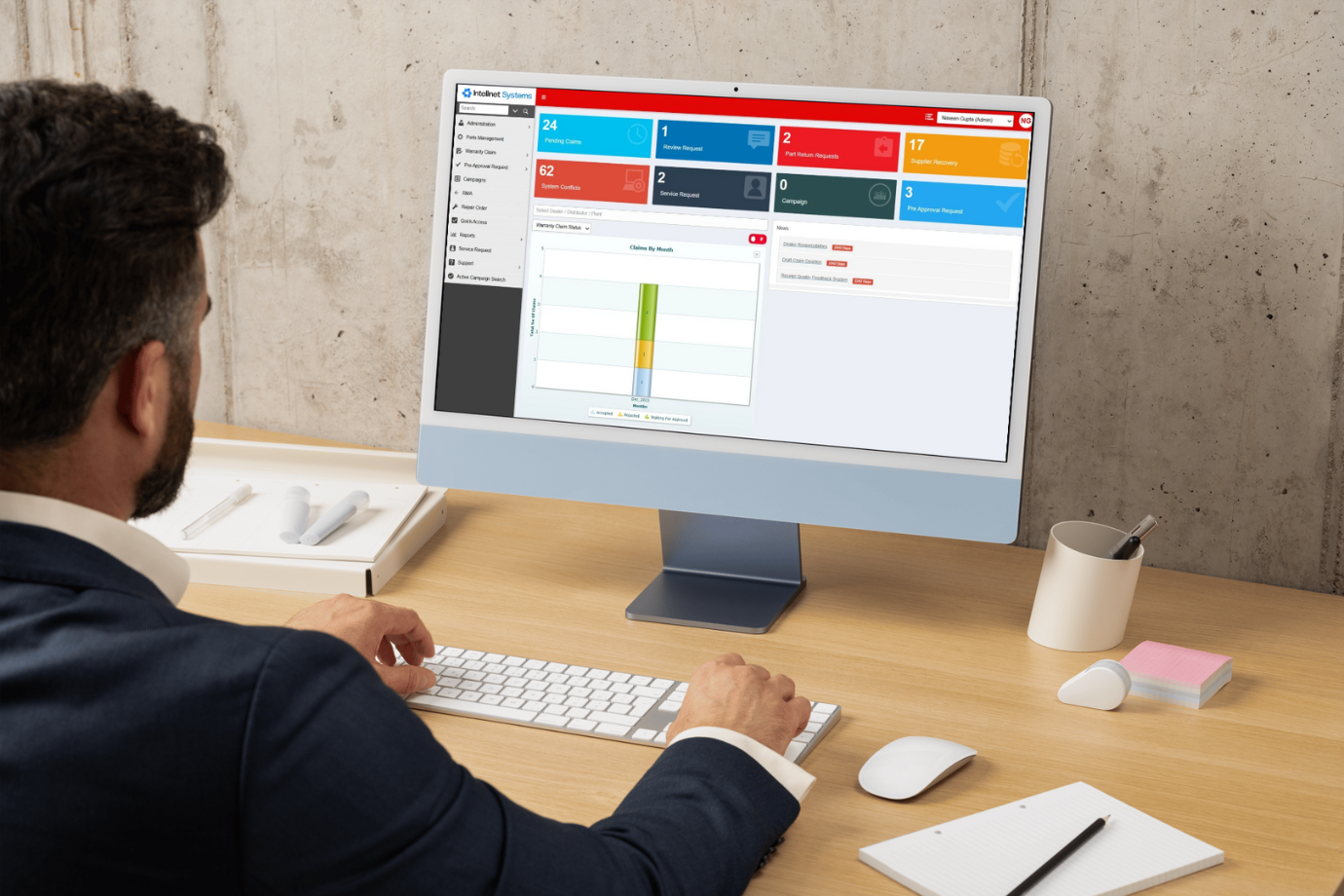
- Automate Important Processes
- Implement Mobile-Based Remote Accessibility
- Data-Driven Decision Making
- Leveraging AI
- Utilizing Cloud-Based Solutions For Flexibility
1. Automate Important Processes
With a better understanding of the process, CXO can easily identify the most time-consuming tasks and automate them. Data entry, verification of claims, approval process, etc are some of the most time-consuming tasks in the process. Switching from traditional methods of warranty management to a software-centric approach has helped several manufacturers in the last decade.
It helps minimize human-caused errors and takes less than half of the time taken by the traditional approach. CXOs should make sure that the processes involved in warranty management software are in regular compliance with the existing market standards along with accurate information.
2. Implement Mobile-Based Remote Accessibility for Field Technicians
With an innovative solution in place, CXOs can analyze the competition in the market and choose efficient software. That not only allows complete access but also provides the convenience of accessing the data from any device including smartphones, tablets, etc.
For example, a technician providing door-to-door service for a customer will have to access the warranty information from a compatible device such as a smartphone or a tablet. Choosing software that provides this flexibility is essential for the business to scale easily.
3. Data-Driven Decision Making
Efficient warranty management software is capable of analyzing large amounts of data quickly. Integrating the software into the existing system can contribute to making better-informed decisions here’s how. CXOs can analyze the data collected through various sources, claim histories, customer feedback, and product performance.
By leveraging these data, they can form an insightful structure of how to tackle the upcoming common defects, cost drivers, and inefficient processes. Utilizing past data efficiently helps manufacturers and CXOs in implementing continuous developments across all departments. CXOs must encourage a culture of learning from previous data and maintaining up-to-date information about every claim.
4. Leveraging AI
Warranty management software solutions such as Intelli Warranty utilize AI-driven analytics to identify repetitive patterns and trends in warranty claims. This single-handedly identifies a specific defect in a part or component and this data can then be utilized by CXOs to bring improvements to the product.
It is essential to choose software that has a well-trained AI technology that delivers data with accuracy and operates at high quality. A majority of processing time can be reduced by half, errors can be minimized and fraudulent claims can be identified easily by implementing AI in the process.
5. Utilizing Cloud-Based Solutions For Flexibility
Integrating a cloud-based warranty management system can significantly improve the overall performance of the manufacturing company. The CXO must prioritize features such as growth, flexibility, data security, compliance with regulations, and real-time access while selecting the right warranty management software for their OEMs.
They must also ensure that the selected cloud-based software will be compatible with the company’s future expansion goals. Such software solutions can be customized according to the needs of the OEMs and also have easy integration features.
Why Trust Intelli Warranty?
CXOs play a greater responsibility than just managing the products manufactured by the company. But to also manage how the product performs in the market among customers and bring in improvements. CXOs can handle current challenges in warranty claims management such as dependency on manual labor, inaccuracies, lack of systematic procedure, inefficient identification of fraudulent claims, and much more with the help of Intelli Warranty.
Must Check: A Complete Guide to Warranty Management Software
Innovative solutions provided by our software offer CXOs with an opportunity to make their manufacturing companies thrive in the aftermarket. Automation, integration of AI, error-free operations, and streamlined process execution are some of the features provided by Intelli Warranty that promote business growth and overall success. To know more about warranty management software and choose the right one for your manufacturing company, reach out to us and get a free demo today.