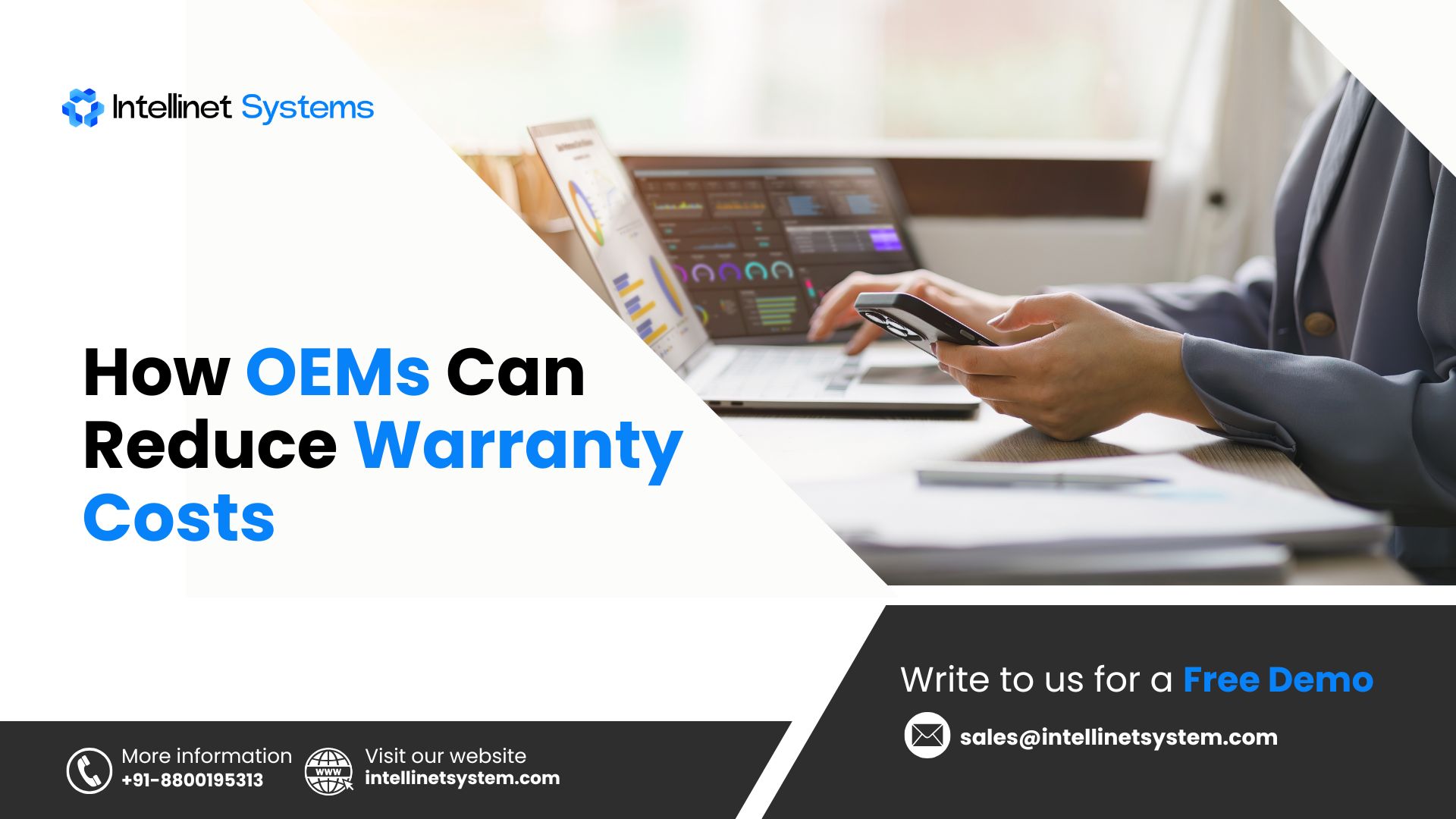
The growing demand for technology and machinery across industries worldwide is fueling the steady growth of OEMs. However, as sales rise, boosting profitability is an equally important concern, for which lowering costs is essential. Warranty cost control is an effective means to lower expenses for an OEM without sacrificing quality or expansion.
Utilizing warranty management solutions can significantly enhance the overall management of warranties, thereby reducing warranty costs and providing a boost to profitability. Moreover, warranty management software can aid in reducing the chances of warranty fraud, improve inventory management, and supplement overall product development.
Importance of Reducing Warranty Costs
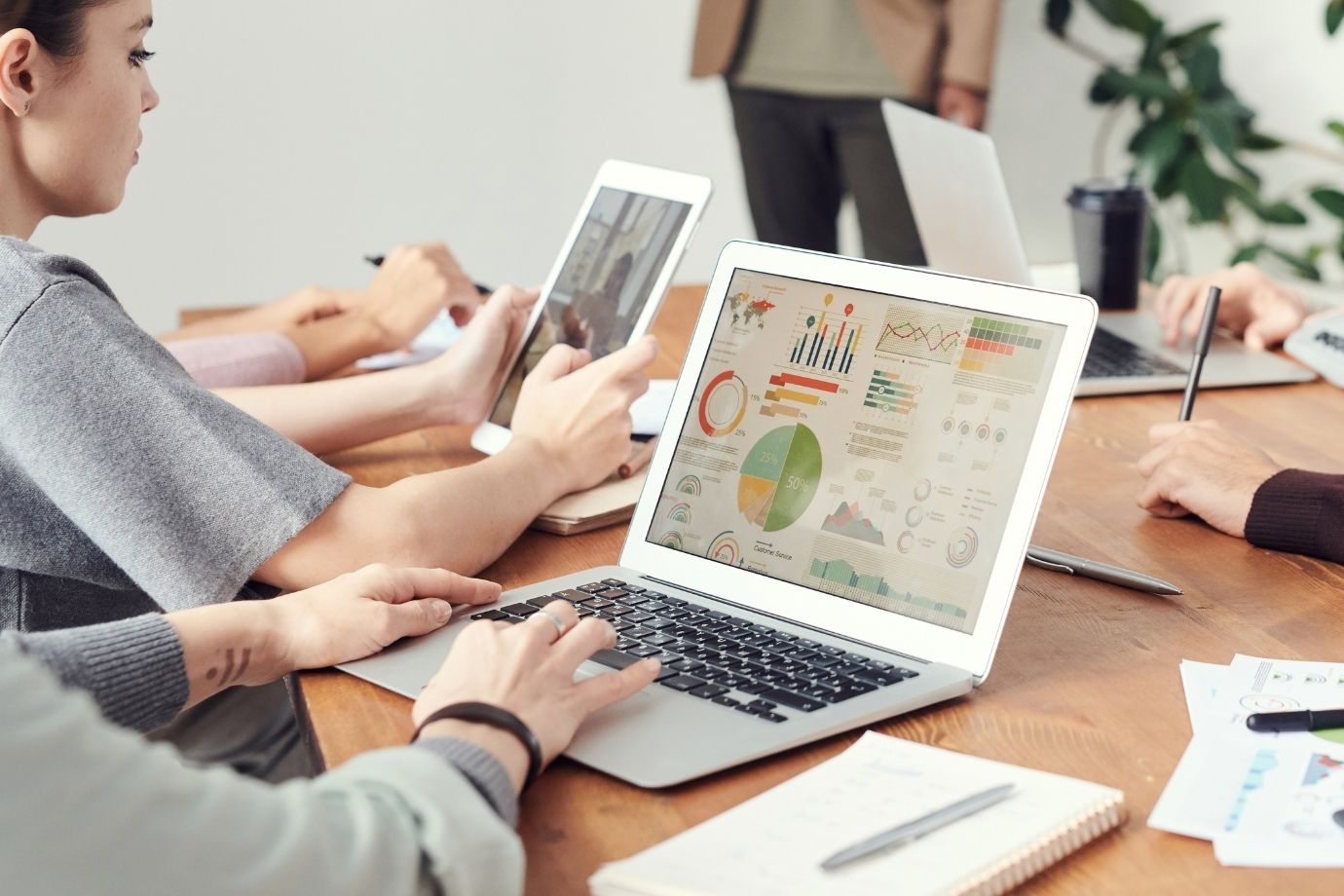
Annually, warranty claims can account for around 2% of revenue for OEMs, and while the percentage may seem small, in overall terms, the numbers add up. Apart from the loss in revenue, increased warranty claims can have an even higher detrimental impact on the brand image of an OEM. If a particular OEM is frequently facing warranty claims, that can bring into question the quality of products and production, leading to a reduction in sales.
Another concern in reducing warranty claims is to be able to prevent fraudulent claims. Such claims increase overheads in processing and can result in overall losses if they are not identified, flagged, and dealt with. Reducing warranty fraud aids in lowering costs and improving brand image.
Depending upon the specific OEM and industry, the source of warranty expenses can vary significantly. Identifying the core cause of warranty expenses is an integral step toward warranty cost control. By finding the source of most of the warranty expenses, a suitable strategy and protocol can be implemented to target the causes in a comprehensive manner, thereby boosting profits and improving customer satisfaction.
An effective approach to target and reduce warranty costs is by implementing warranty management solutions. By using software for warranty management, there is a great deal more accountability throughout the process. OEMs can also use these software solutions to conduct an accurate warranty data analysis. Data insights can provide valuable information that can be used to improve OEM operations overall, thereby reducing warranty claims and associated costs.
As OEMs continue to grow and expand, having a scalable solution in place to manage warranty claims is becoming a necessity. For high-volume warranties, tracking claims manually can be a substantial overhead in costs and human resources while also increasing the risk of errors. While warranties may be a relatively smaller component of the operations of OEMs overall, the value of warranty cost control is manifold.
How to Reduce Warranty Costs and Boost Profitability
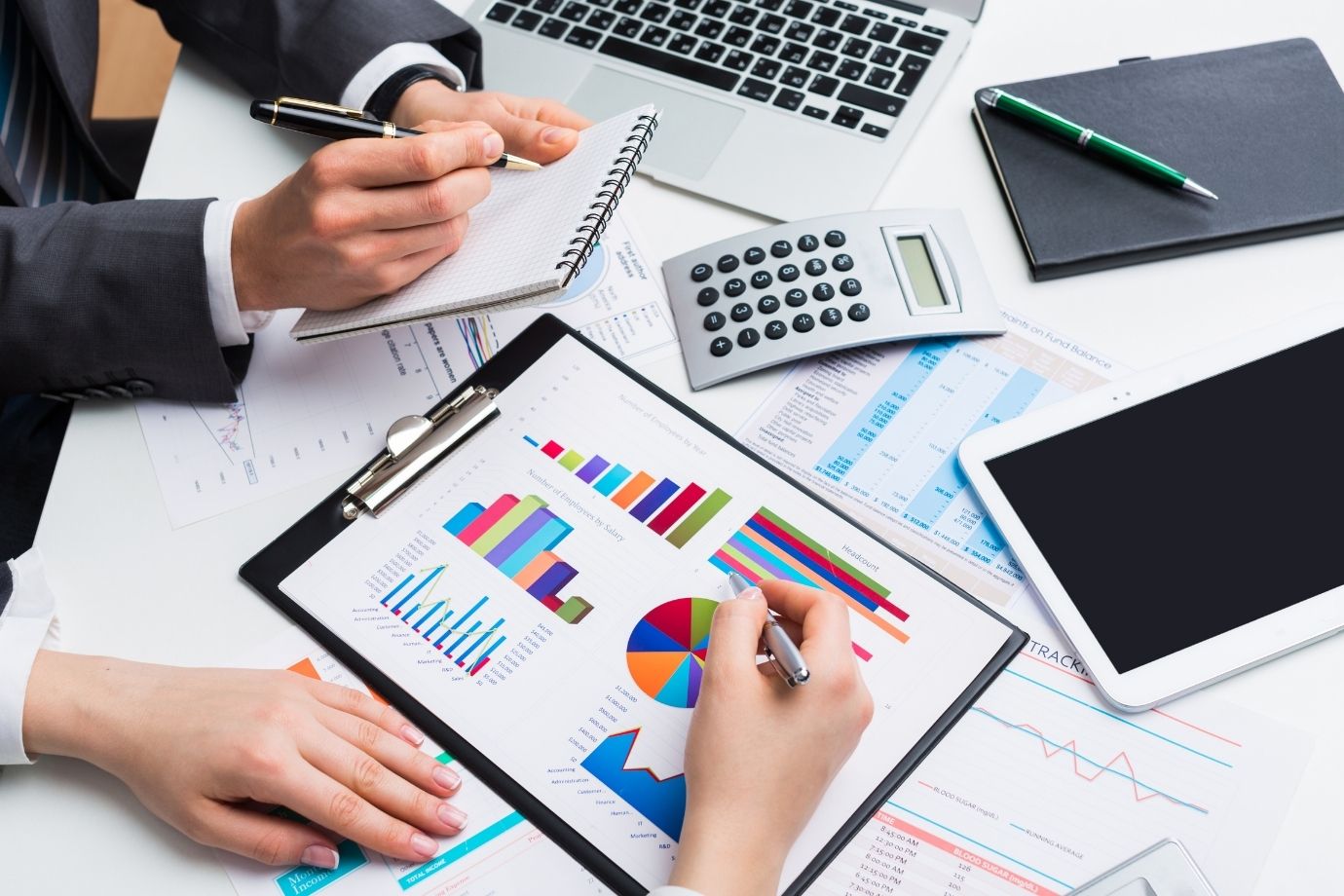
Warranties have become standardized across industries, and accordingly, are an integral part of OEM offerings. However, inadequate management of warranty policies and lack of warranty process optimization can result in a substantial increase in warranty costs and more frequent warranty claims.
Although there are several warranty cost reduction strategies that OEMs can consider, warranty management software such as Intelli Warranty offers a targeted approach toward cost-saving strategies.
Some of the ways to reduce warranty costs and boost profitability include:
1. Warranty Process Optimization
Optimizing the entire warranty process through smart, integrated warranty management systems such as Intelli Warranty aids in improving the overall warranty lifecycle. Each individual stage is simplified, tracked, and monitored for overall results. Large volumes of warranties can be managed from a singular system and incoming warranty claims can be processed directly, thereby improving warranty cost control.
Setting in place a system and protocols on how to deal with specific warranty claims through warranty process optimization results in a seamless and faster system overall. As per preference, OEMs can define rules on how to respond to particular warranty claims, either based on part, type of warranty, response type, duration of warranty, or any other desired parameter.
Users authorized to file warranty claims can be added to the system, providing them with an easy-to-access and user-friendly interface to file warranty claims. With warranty process optimization, incoming warranty claims can be sorted, automatically approved, flagged, or forwarded as desired.
A streamlined process for warranty management also helps in reducing overhead costs as well as operational expenses. With technology providing an overview of the warranty process, there is a reduced need for manual oversight, thereby lowering operational costs.
The supplier recovery process can also be further streamlined by automating forwards for supplier recovery claims. This can enhance the supplier recovery process, aiding OEMs in increasing their recovery rates and amounts from suppliers, and overall boosting profitability.
2. Warranty Fraud Prevention
Warranty fraud is unfortunately rather common with OEMs, ranging from between 3 percent and 15 percent of all warranty costs. These can include both customer and dealer-related frauds can cause financial losses as well as operational losses and damage the reputation of OEMs. Once fraud successfully happens, it’s likely to continue to rise as fraudsters identify weak points in the existing warranty management system.
An effective means of targeting and preventing warranty fraud is the use of warranty management software such as Intelli Warranty. Features such as automating warranty management, increasing transparency, and requiring verification all help with reducing warranty fraud.
Insights provided by warranty analytics can also be beneficial in preventing warranty fraud by identifying any suspicious patterns in warranty claims. A centralized and automated system for warranty-related data and claims enables easy identification of inconsistencies such as repeated warranty claims filed from specific users or for particular parts. Such inconsistencies may be related to potential fraud and can be flagged for further action.
The thorough system of tracking all claims and further steps taken also help in warranty fraud prevention throughout the process. While internal company involvement in warranty fraud is rarely expected, having increased transparency aids in preventing employee-based warranty fraud from occurring.
Capabilities of automated validation and verification of warranty management software can aid in preventing fraud by restricting and reporting claims that do not meet set parameters. Warranty claims can be checked for authenticity by verifying details such as product serial numbers, warranty durations, warranty holders, service history, and purchase dates. Additional protocols for filing and approving warranty claims can aid in reducing warranty fraud in the long term.
3. Product Quality Improvement
The most reliable, effective, and long-term means of reducing warranty costs is by directly improving the quality of products. With better quality products, the need for replacements or repairs, and correspondingly warranties, is reduced overall. Moreover, better quality products also improve brand image and customer satisfaction, further boosting long-term sales and success.
For OEMs, good quality products are a goal from the start, so as to minimize warranty claims from the start. However, even with the most comprehensive research and development initiatives, some problems with products are only visible after extended usage. By utilizing warranty management as a feedback loop, OEMs can boost their product quality improvement based on warranty claims filed.
Warranty management solutions provide complete tracking of the various warranty claims filed, specific parts involved, user feedback, and common complaints. This centralized data collection and warranty analytics can be used to identify trends and common pain points faced by users. The increased traceability of different components in machinery can also help OEMs focus on specific parts causing issues. Based on this data, products can be improved with a more targeted approach and if the issues lie with suppliers, they can be traced and corrected.
Product quality improvement can be a long process, with multiple iterations and slight changes made before more trials and testing. Using data garnered from warranty management software aids in a concentrated approach toward product improvement, leading to faster turnaround times. New products can be deployed and their feedback monitored for further improvements. Accordingly, warranty data analysis can offer significant advantages in improving the overall quality of products, leading to happier customers, more sales, and fewer warranty claims in the future.
Advantages of Intelli Warranty
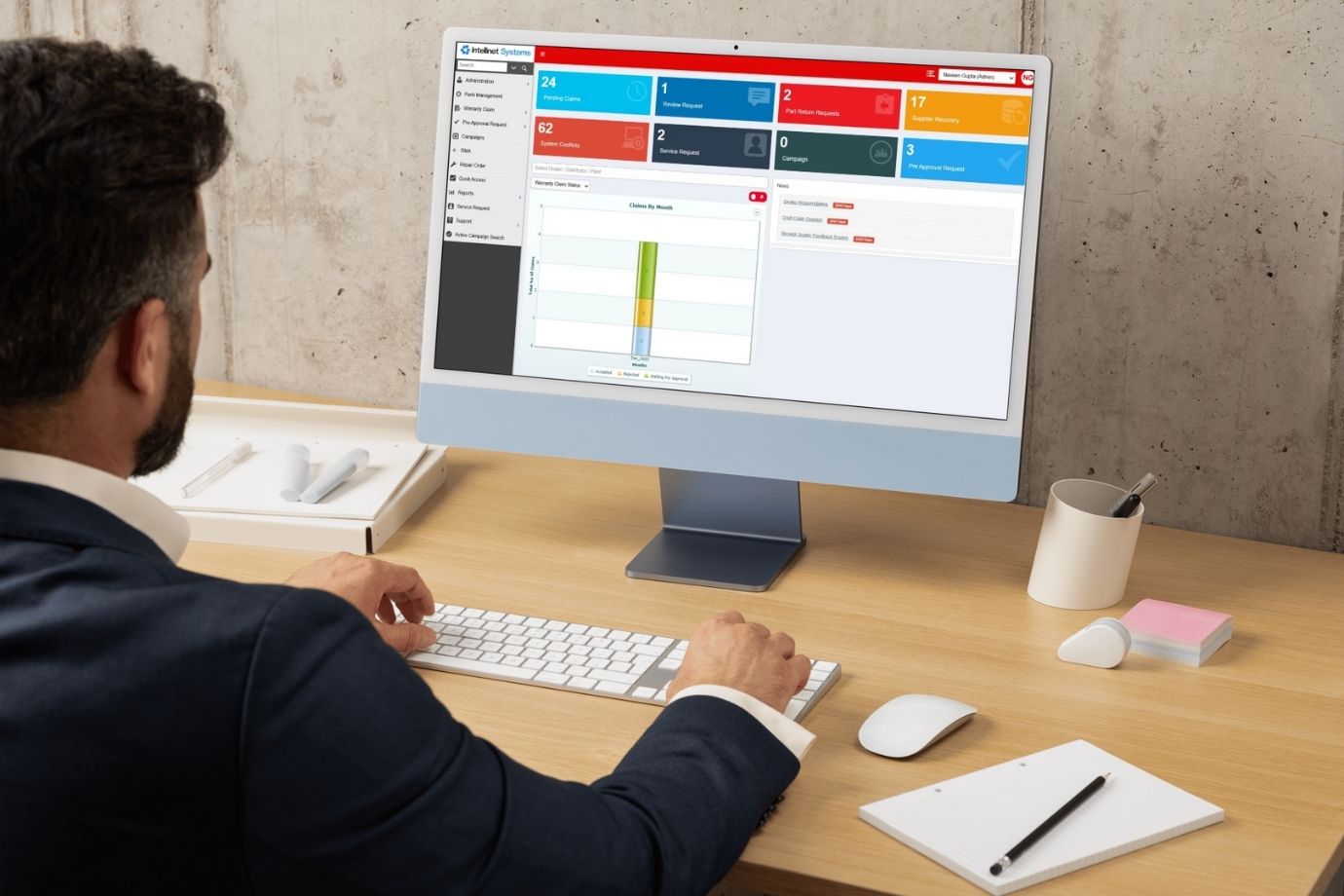
Designed specifically for OEMs, Intelli Warranty is a smart and integrated warranty management system that automates the complete warranty process. Intelli Warranty aids OEMs in managing warranty claims and supplier recovery by streamlining the entire warranty lifecycle, leading to improved operational efficiency and enhanced customer satisfaction.
1. Streamlined Claim Processing
Claims processing is fully streamlined for OEMs and users with Intelli Warranty, supporting easy filing of genuine claims and straightforward processing based on pre-set parameters. Various templates are available for claim creation that can be provided to users, along with requests for uploading of supporting documents, and adherence to verification checks.
Once a claim is successfully filed, the warranty management software can recommend the next steps based on pre-set rules, including direct approval by authorized personnel. The easy claims filing process improves user satisfaction while also reducing warranty claims that do not meet the verification and documentation requirements.
2. Fully Customizable
OEMs may have a similar basic concept, but beyond that, their niche, operating style, and particulars may vary significantly. Intelli Warranty is a fully customizable system for warranty management and can be adapted to suit any specific needs or particulars. These include flexibility in the definition of warranty terms, model versions, component coverage, reimbursement terms, and other parameters. Multiple claim types are supported such as post-sale, OEM PDI, campaign, spare parts, goodwill, and dealer PDI.
The Intelli Warranty system is also customizable in terms of integrations with existing systems. It can seamlessly connect with existing OEM systems such as ERP and DMS through APIs and pre-built connectors so that all systems work cohesively. By integrating systems already used, the warranty management software can aid in real-time analytics, more accuracy in claims processing, and improved collaborations with suppliers and dealers.
3. Lower Operational Costs
With large volumes of claims coming in daily, there are additional overhead costs involved in dealing with them manually. The Work Queue feature of Intelli Warranty deals with claims using an optimized approach, utilizing pre-set rules based on dynamic parameters to quickly deal with claims, thereby reducing warranty costs. Automating the generation of supplier claims based on approval of dealer claims also optimizes the process for supplier recovery, thus increasing recovery amounts.
Simplifying the entire process of claims and fulfillment also aids in improved warranty cost control while also lowering administrative expenses. Validation and verification checks further increase the accuracy of warranty claims processing and minimize the risk of human errors which can become costly in the long run. With optimized warranty management solutions, OEMs can focus their resources on other tasks without lowering the quality of warranty management processes.
4. Enhanced Customer Satisfaction
An easy-to-use interface with clearly specified protocols for filing warranty claims simplifies the claims filing process for customers, thereby boosting customer satisfaction. Moreover, the warranty process optimization capabilities of Intelli Warranty facilitate prompt responses for incoming warranty claims, which boosts the trust of customers. Faster fulfillment rates for standard claims also improve OEM brand reputation and increase customer loyalty.
The warranty analytics provided by Intelli Warranty can have a strong impact on improving customer satisfaction by identifying key ways for OEMs to further improve. This includes product quality improvement as well as general improvements in warranty processes.
Thorough records and tracking of the warranty fulfillment process can identify any potential bottlenecks and also which parts are more commonly a concern. Inventory management can be adjusted accordingly to account for parts facing an increase in warranty claims so that fulfillment can continue to take place in a timely manner. Enhanced customer satisfaction encourages repeat customers and positive recommendations which are effective in boosting profitability in the long-term.
Conclusion
OEMs can significantly reduce warranty costs as well as boost their profitability by utilizing robust warranty management software. A smart software solution for warranty management such as Intelli Warranty can aid in optimizing the overall warranty process, prevent fraud, and aid in product quality improvement. By improving the overall warranty management process, OEMs can reduce overhead expenses, facilitate faster warranty processing, and enhance customer satisfaction.
Warranty management solutions also provide extensive data that can be used in various ways to further improve warranty processes and products overall. A key component of warranty cost reduction strategies, scalable software solutions are designed to grow with the business, supporting the expansion of user bases and warranty offerings. Intelli Warranty is customizable and seamlessly integrates with existing systems to provide a cohesive approach to warranty management.
To learn more about Intelli Warranty and its suitability for your business, reach out to us today for a free demo.