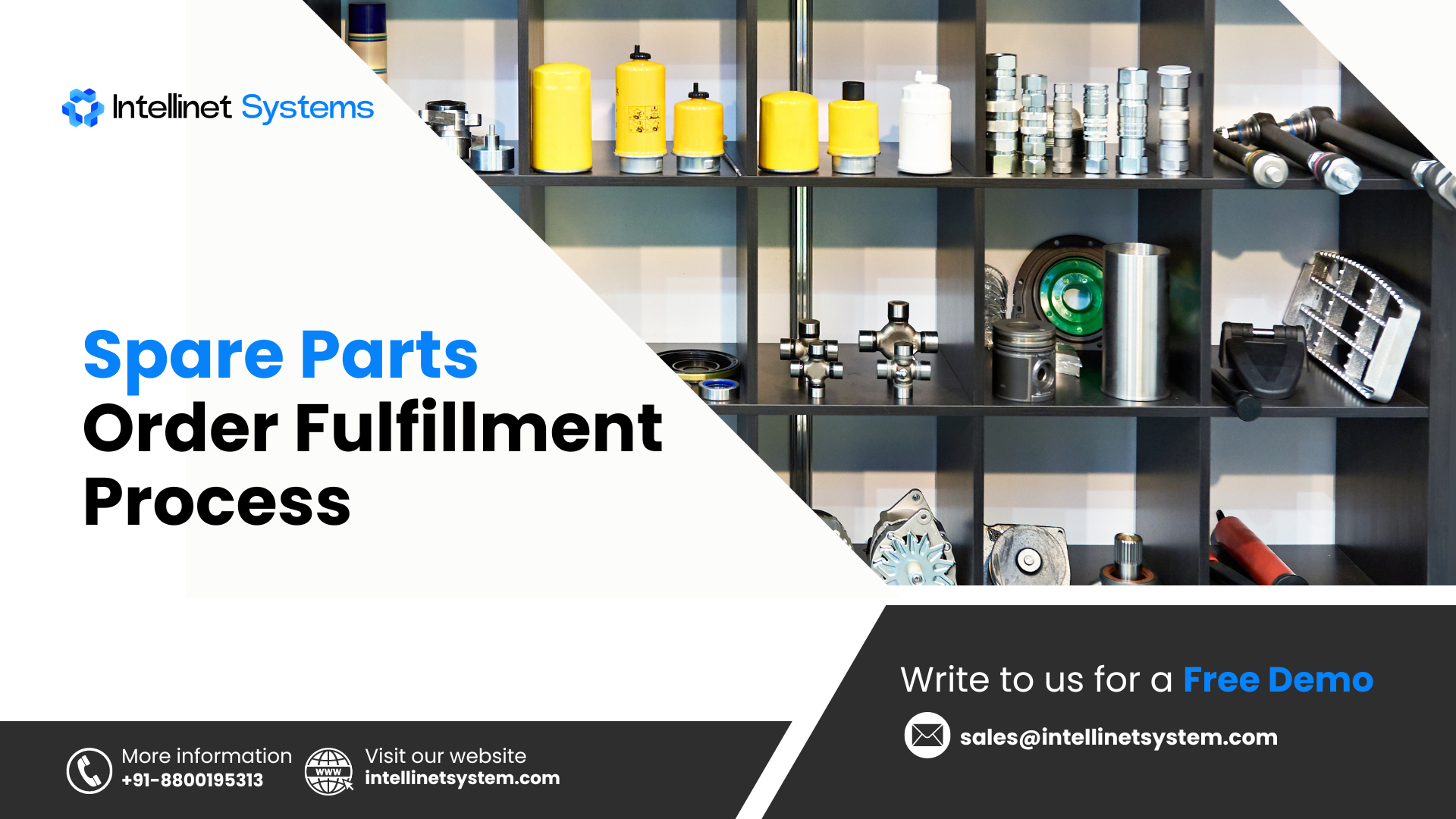
Thousands of parts, multiple locations, and timeliness are key! Have you ever wondered how OEMs and dealers maintain a steady flow of spare parts precisely when their customers need them? A company's reputation depends largely on the services provided to the customers after a purchase is made. The aftermarket industry pays close attention to fulfilling the needs of their customers through various services, including repair, replacement, and warranty.
To maintain the smooth operation of these services, it is essential for OEMs and dealers to have a systematic process in place. Inventory management and parts ordering present some of the biggest challenges faced by the aftermarket industry. Several challenges are associated with inventory management and parts ordering since the traditional methods were outdated and time-consuming.
Through this blog, let us understand the essential changes that digitization has brought to the aftermarket industry and examine how it has improved the spare parts order fulfillment process.
What is Spare Parts Order Fulfillment?
Every manufacturing company has to make sure that their aftermarket services are top notch for customer retention and brand image. Which is why OEMs and dealers have to stay updated with the latest aftermarket solutions to stay relevant. Spare parts order fulfillment is one of the many processes involved in the aftermarket including inventory management, delivery of shipment, replacement services, and much more.
Spare parts order fulfillment is an essential process in inventory management. This is because downtime can cost too much money for industries such as automotive, heavy machinery, aerospace, etc. The availability of the right spare part is crucial in such cases and could determine whether the customer will come back to the same dealership again.
Explained: Spare Parts Order Fulfillment Process
The process of spare parts order fulfillment is closely related to inventory management and includes the involvement of usually more than one distribution system. Let us understand the workings of spare parts order fulfillment to know the importance of the process:
- Managing Inventory
- Storing Inventory
- Processing Order
- Selecting From Warehouse
- Shipping
1. Managing Inventory
The process starts with the basics of keeping track of all the parts available in the inventory and accessing the demand. It is essential to place the order based on the current availability and sale of the particular part. This ensures that the right part is available when needed instead of running out of stock or piling of stocks.
2. Storing Inventory
In this step, most manufacturers or dealerships have integrated software in their systems that allows them to place an order with the suppliers. This order placement detail includes the type of part they require, its model, quantity, and every other detail needed to manage an efficient inventory.
3. Processing Order
Once an order has been placed, the software confirms from the system if the placed parts are available in the inventory. If not, the order is then placed with the manufacturers to maintain the fulfillment of stocks.
4. Selecting From Warehouse
After the order is placed, the staff at the warehouse makes sure that each part is selected and packed carefully to avoid any possible damages during shipment. After the needful preparations are made, the parts are ready to be delivered to dealerships.
5. Shipping
The packed parts are then shipped to different locations depending on the order placed. It is either shipped directly to the customer or to dealerships.
What are the Challenges Faced by OEMs and Dealers in Spare Parts Order Fulfillment?
1. Too-Much or Too-Little Stock
One of the essential challenges faced by both dealerships and OEMs is finding the right balance between too much or too little stock. Having excessive stock in the inventory can tie up the capital through maintenance of excess stock and costs associated with warehouse maintenance.
Having little stock or running out of stock has its own downfalls, including spending more than usual on last-minute shipment, excessive operational costs for last-minute demand, and increased downtime.
Without the right balance, both dealerships and OEMs face the downfall of losing their customer’s trust and any future sales through them.
2. Storage Costs for Excess Stock
Having excess stock of certain parts that do not sell easily or frequently can surely take up a large portion of the warehouse. In most cases of overstocking, businesses have to spend a huge amount of money to invest in additional storage. There are other consequences associated with overstocking too, such as the parts in storage becoming outdated and being sent to scrap.
This not only results in the waste of parts but is also a huge financial loss for the company. For example, in the automotive industry, parts undergo changes frequently due to efficient engineering. This makes the old parts obsolete and a huge waste of investment.
Although, now companies have started to encourage more sustainable practices and introduced methods to reduce carbon footprint. But these outdated parts piling up, in the warehouse might still not be sold for the original price that they were bought for.
3. Time Consumed in Bookkeeping
For a long time, dealerships and OEMs had to tackle the challenges that came with traditional methods of inventory management. This involved manual bookkeeping of inventory and maintaining this in a hardcopy format.
Everything from tracking orders to updating records and stock levels was conducted manually, which was extremely time-consuming and expensive. Operational inefficiency was only one of the problems associated with physically updating, printing, and circulating this updated information about existing stocks.
Here’s How Digitization Has Improved Spare Parts Order Fulfillment Process
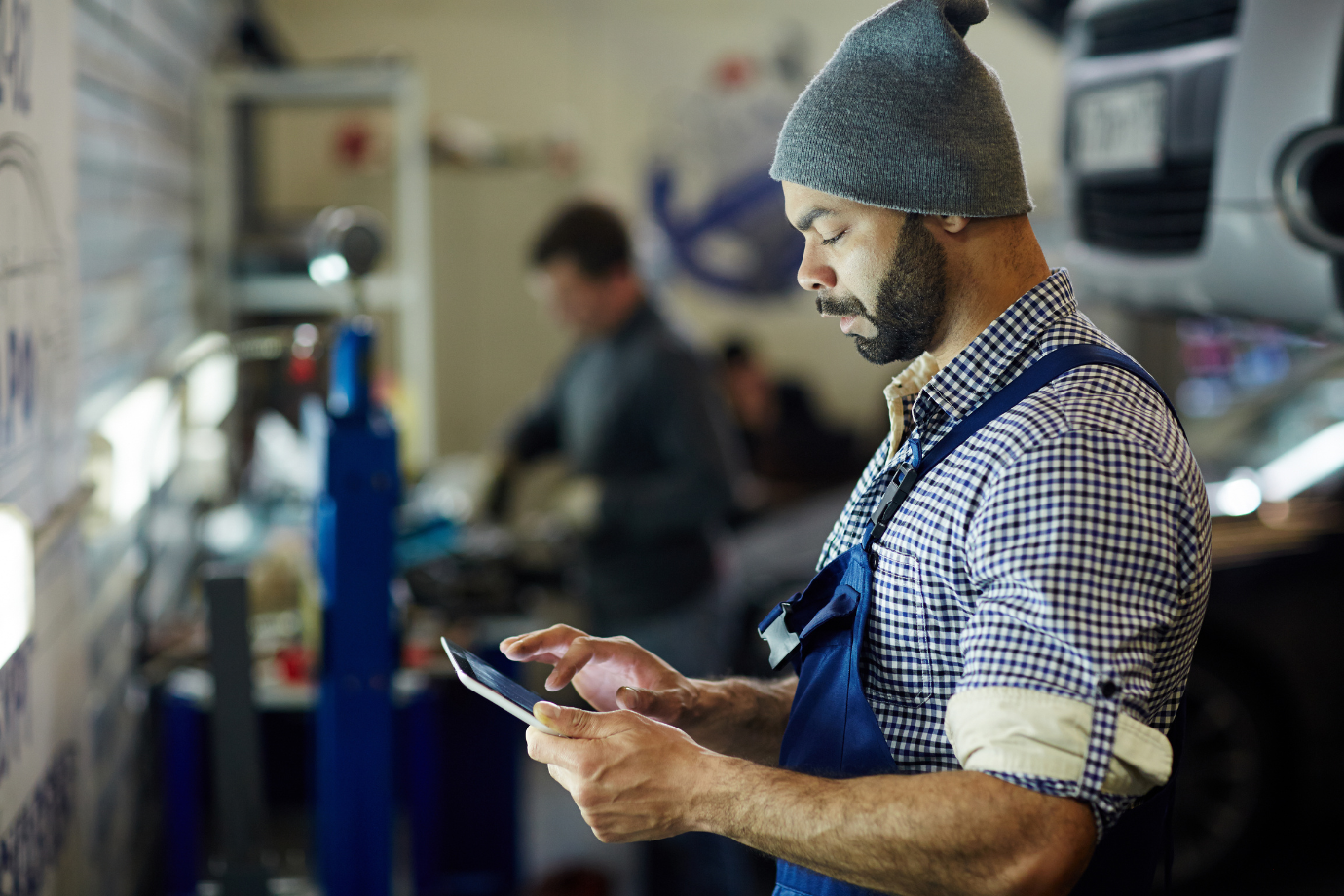
Over the years, the manufacturing industry has inculcated major changes within the aftermarket services to ensure that their existing customers receive the best experience. Here are 6 ways by which digitization has helped in revolutionizing the spare parts ordering and management system.
- Proper Management of Spare Parts
- Accurately Maintaining Bill Of Materials (BOM)
- Invest in the Right Inventory Management Software
- AI & Inventory Forecasting
- Automation of Ordering Process
- Centralized Communication System
1. Proper Management of Spare Parts
Digitization of inventory management has changed the outlook of the aftermarket altogether. With better visibility, efficiency, and accuracy, supply chain management has become more systematic. Efficient spare parts inventory management software integration has helped OEMs as well as dealers with real-time stock updates and an automated and improved parts fulfillment system.
With the help of accurate and real-time stock assessment, companies can consciously make better decisions in less time. With manual methods and constant updating out of the way, dealers can utilize the money for the growth of the company.
Integrating the right digital software with the existing system has helped businesses conveniently find the right parts at the right time. Additionally, advanced search features have reduced the time by half. Both technicians and OEMs can search for any spare part with the help of the model number, VIN number, unique code, etc.
2. Accurately Maintaining Bill of Materials (BOM)
With the presence of BOM, anyone can easily identify the model number, last servicing conducted, etc. Optimizing the BOM requires scheduled updating of the inventory on a frequent basis and in real-time.
This ensures that all departments are informed with the right data at all times. This has helped companies minimize errors associated with accidentally using outdated or incorrect parts. It has also allowed different departments to connect and collaborate with real-time updates for maximum accuracy.
3. Invest in the Right Inventory Management Software
Automated ordering system, real-time updating features, stock level monitoring, and stock prediction are some of the features that have helped in reducing time and saving cost. Switching to digital parts ordering software solutions instead of traditional methods of parts ordering has helped in reducing human error and seamlessly integrating other software for ease of access. Investing in the right software considering your business’s needs is essential for any company. Consider the following before choosing the right software for your business:
- Scalability: Ensure that your software is flexible with your business and adjusts with your future goals.
- User Friendliness: Choose software that is easy to use and can be easily used by your staff.
- Customization: Make sure that your software can be customized to your specific needs and industry requirements.
- Integration Options: Confirm that the software can be integrated easily with the existing software used by the team for different tasks.
- Customer Support: Opt for a solution that has an active customer support service with quick response.
4. AI & Inventory of Standard Work Order Process
Besides making parts ordering procedures smoother and more efficient, AI-driven systems can actively analyze patterns, help in processing through large amounts of data, and provide inventory prediction insights. Predictive analysis of stocks based on demand in the past has been extremely fruitful for both OEMs and dealerships in reducing the cost associated with last-minute shipments.
AI and data-driven software have together minimized the downtime and enhanced the customer experience. Order fulfillment process through AI integration and supply chain management has positively impacted the aftermarket industry with better customer retention as well as brand value.
5. Automation of Ordering Process
Automation of the spare parts ordering process has reduced the risk of human error throughout the process by accurately placing an order when the number of parts reaches a threshold. It has also drastically reduced the time that was invested in manually entering the data, therefore reducing the delays associated with the process.
With the real-time tracking features, all departments can efficiently trigger reordering whenever necessary. Besides making things smoother, it also shortens the time involved in bookkeeping by the employees, therefore freeing up time for experienced staff to work on different tasks.
6. Centralized Communication System
The traditional methods of communication between different teams were slow and inefficient, even after a systematic method was introduced, it did not allow different departments to easily collaborate. With the shift to digitization, all departments can efficiently collaborate, communicate, check real-time stock availability, and make decisions accordingly.
Conclusion
Although the inventory management and parts fulfillment system is much more capable than presenting communication as well as prediction. It has brought in new possibilities for different businesses in terms of goals and flexibility. Digitization of different processes within the business has made it much simpler for a business to consider expansion and branching into other sectors.
A few years ago, manufacturers were rigid to change and were predominantly dependent on manual practices rather than software. As both manufacturing and digital software industries aligned, it took a positive turn, introducing new possibilities. It has brought a new outlook for customers, as they can make better informed decisions.
To transform your company with an efficient parts order fulfillment process, contact us today and get a free demo!