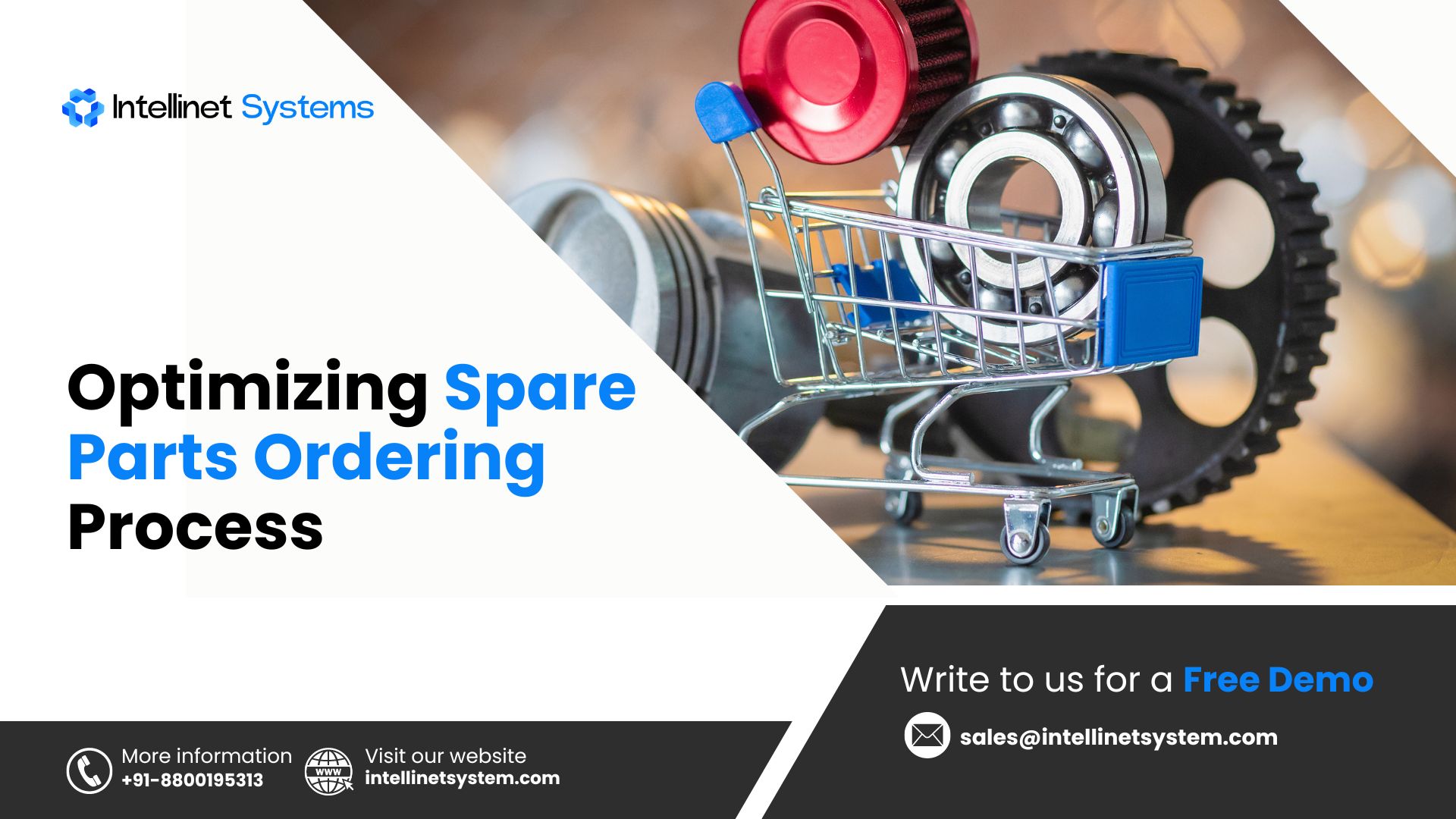
The management of spare parts is crucial for manufacturers in any industry type. Today, it has become essential that manufacturers streamline their spare parts management process to prevent expensive downtimes and improve the lifespan and reliability of the equipment. Spare parts management is a process with a certain set of activities involved such as inventory management, ordering, fulfillment, and more.
The availability of spare parts is directly proportional to customer satisfaction as downtime leads to failure of equipment. Non-availability of spare parts would mean longer times taken for repair or maintenance. For every manufacturing company, the availability of spares is a crucial aspect of service operations. This direct impact on the service and maintenance results in diminished customer satisfaction and costly equipment breakdowns. Manufacturers also have to maintain the service levels and the quality of the spares through an efficient parts ordering process.
Let us now see what strategies to implement to improve the process of spare parts ordering.
What is the Importance of Management of Spare Parts
When we talk about spare parts, it often is symbolic with movement of parts in the supply chain, collaboration between different teams and departments, and also enhancement of customer satisfaction. But, before delving into the intricacies of strategies to implement, let us understand the importance of efficient spare parts ordering management.
• Downtime is Reduced:
When there is optimum availability of spare parts, the repairs and maintenance operations can be done within the stipulated time frame, without any delays. Such a practice will improve customer satisfaction and also enhance the profitability of the business.
• Reduced Costs:
When the inventory is managed optimally, there are little or no chances that there would be challenges in the availability of spares for service and maintenance operations. This results in the avoidance of overstocking and understocking.
• Enhanced Customer Satisfaction:
When the service activities such as repairs or maintenance are done on time and there are no delays in that process, the customer experience is improved which enhances the customer satisfaction. Businesses need to ensure that service levels are met and strategies implemented are customer-centric.
Now that we understand the importance of the management of spare parts and its implications, let’s discuss the strategies to improve the spare parts ordering process.
What Strategies to Implement for Improving the Ordering Process for Spare Parts?
1. Accurate Demand Forecasting:
It becomes necessary for manufacturers to forecast the demand for the next month or quarter. This helps them with the clarity and transparency in terms of what parts are most selling and what needs improvement. This activity would also help them optimally maintain the inventory levels and avoid over or understocking of spares. Let’s see how it can be done:
Analysis of Historical Data:
This helps manufacturers find patterns and trends related to the consumption of spare parts. With historical analysis, one can also get deep insights into the performance of sales of spares and services.
Statistical Analysis Through Modeling:
This method can be used to determine and identify the consumption of spares based on historical data. This gives the clarity of consumption and also offers insights on sales of spares through various channels.
Machine Learning:
Machine learning enables businesses to enhance the forecasting of spares by employing advanced analytics from historical data. By leveraging advanced technology, businesses can ensure the service and parts teams are working in sync and the operations are streamlined.
2. Optimization of Inventory:
To ensure that there are no unplanned or unscheduled downtimes or delays in repairs for customers, businesses should maintain inventory in such a manner that there is no overstocking or understocking. Both these situations would lead to losses incurred for businesses. Diminished customer satisfaction would also harm the profitability of the company. Thus, there needs to be measures implemented to optimize and plan the inventory. This strategy requires analysis and optimization of stock on a real-time basis. There are many spare parts ordering systems available which are enablers in maintaining inventory levels. Let us now see what methods can be utilized in this strategy:
ABC Analysis:
This strategy requires businesses to segregate and categorize the spare parts based on their usage. Such categorization can also have an additional parameter of the value of spare which could help them achieve efficiency in categorization.
Safety Stock:
It is an additional stock maintained in case of any surges in demands. Maintaining the safety stock ensures that there are no gaps in the demand and supply. If there are sudden fluctuations in the demand for any spare parts, the safety stock can cater to this need.
Vendor Managed Inventory:
Businesses can also partner with various suppliers to ensure the demand for spare parts is met and there are no shortages of spares when the need arises.
3. Centralized Spare Parts Management:
Traditional challenges in spare parts management included the non-availability of centralized information about spare parts availability. At every location, these management processes were siloed which resulted in zero transparency in the ordering process. This resulted in gaps between demand and supply and caused delays and complexities in the supply chain. There is a need to improve the visibility in the availability of spare parts which can improve the efficiency of the parts ordering process. Let’s see what strategies can be implemented in this process:
Centralized Database:
This is a crucial aspect of any operation. Maintaining a centralized database ensures that there is visibility and transparency in the operations with better collaboration and synchronization between teams and stakeholders. Maintenance of a centralized database takes into account various parameters such as part numbers, part description, suppliers associated with a particular part, and the level of stock currently maintained.
Standardization of Processes:
While maintaining a centralized database is important, it is also crucial to standardize various activities associated with the parts ordering process. This standardization is done for ordering, receiving, and storing the parts.
Tracking of Inventory in Real-Time:
There are various software in the market that help in maintaining this tracking of inventory. Many businesses have integrated systems with various aftermarket software to ensure that there is transparency and streamlined operations for these spare parts ordering processes.
4. Implementation of Technology:
There are various software available that businesses can utilize to streamline the ordering process for spare parts. This helps them with better management of spare parts and maintaining transparency in operations. Let’s check out these software’s:
Enterprise Resource Planning Software (ERP):
ERP systems come in handy as the management of various processes can happen through a centralized platform. When manufacturers use any dealer management systems or similar products, it can very well be integrated with the ERP to provide an all-around management of processes related to dealer management. Similarly, management of parts ordering processes can also be done through ERP software.
Automated Ordering Systems:
There are many systems and software available in the market that automate the generation of purchase orders. This automation is based on predefined parameters that are defined by the administrators, in this case, the manufacturers, such that if that condition is triggered, the purchase order will be generated automatically.
Mobile Technology:
When performing field service operations, the workforce has to be equipped with software on the mobile to carry out the inspection and identification of the parts that are to be repaired or replaced. During this process, the technicians place orders for the spares to be replaced. Thus, a solution is required for them to present the parts ordering process on the go.
Conclusion
Manufacturers need to optimize their parts ordering process in order to reduce the administrative burden of costs and also ensure that the processes are streamlined. This is a need for various industries and businesses to enhance their operational efficiency significantly through a strategic implementation of technology and software products to manage the ordering of spare parts and also offer a higher degree of transparency into the operations and inventory.
With strategic implementation of technology, businesses can ensure that the customer satisfaction is enhanced. This also results in higher profits and better margins as the costs are significantly reduced. This is an ongoing journey and not just a one-time activity. Businesses need to practice these strategies and the implementation of such measures have to be done company-wide. This would also mean training the workforce on any new systems that are being deployed.
There is a direct impact of such strategies on the growth of organizations and enhancing the profitability of the business.