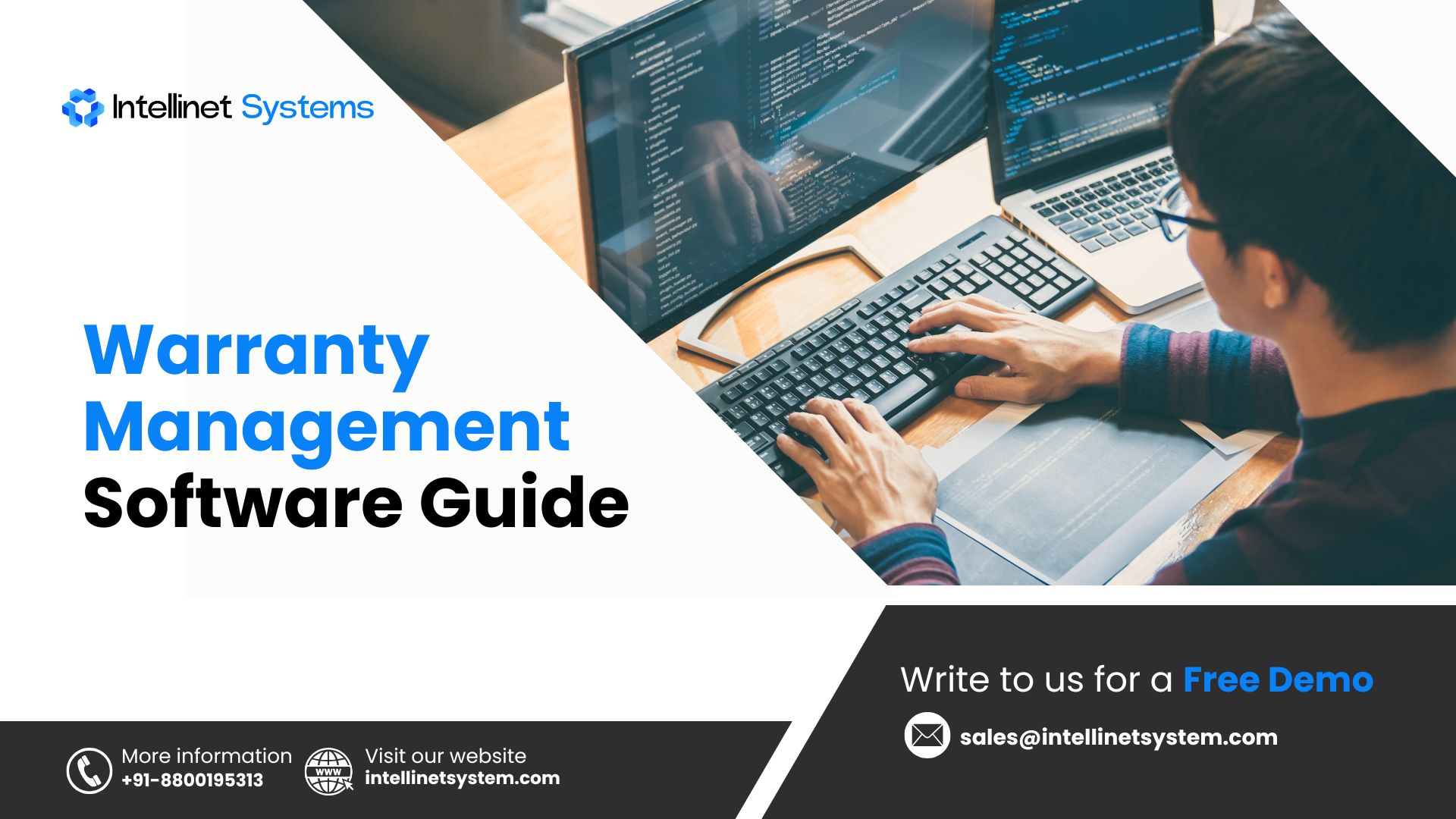
Globally, warranties are an accepted and expected component in the sale of a vast range of products, ranging from automotive and industrial equipment to aerospace and electric vehicles. Consumer goods are also increasingly being equipped with warranties. With the growing demand for machinery and equipment, OEMs are expanding in scale and production capabilities. Accordingly, the volume and complexities of warranties are also on the rise, and the need for effective warranty management solutions.
Warranties may be becoming an integral part of the sales of numerous products; however, increased warranty costs can prove expensive for OEMs, cutting into profitability. Improving the warranty management process and protocols is surging in importance so that OEMs are able to reduce warranty costs without compromising on the quality of service provided to customers. While the long-term goal is most often to improve product quality so that warranties aren’t required, in the short-term, optimizing warranty management can help reduce costs and support product quality improvement.
What is Warranty Management?
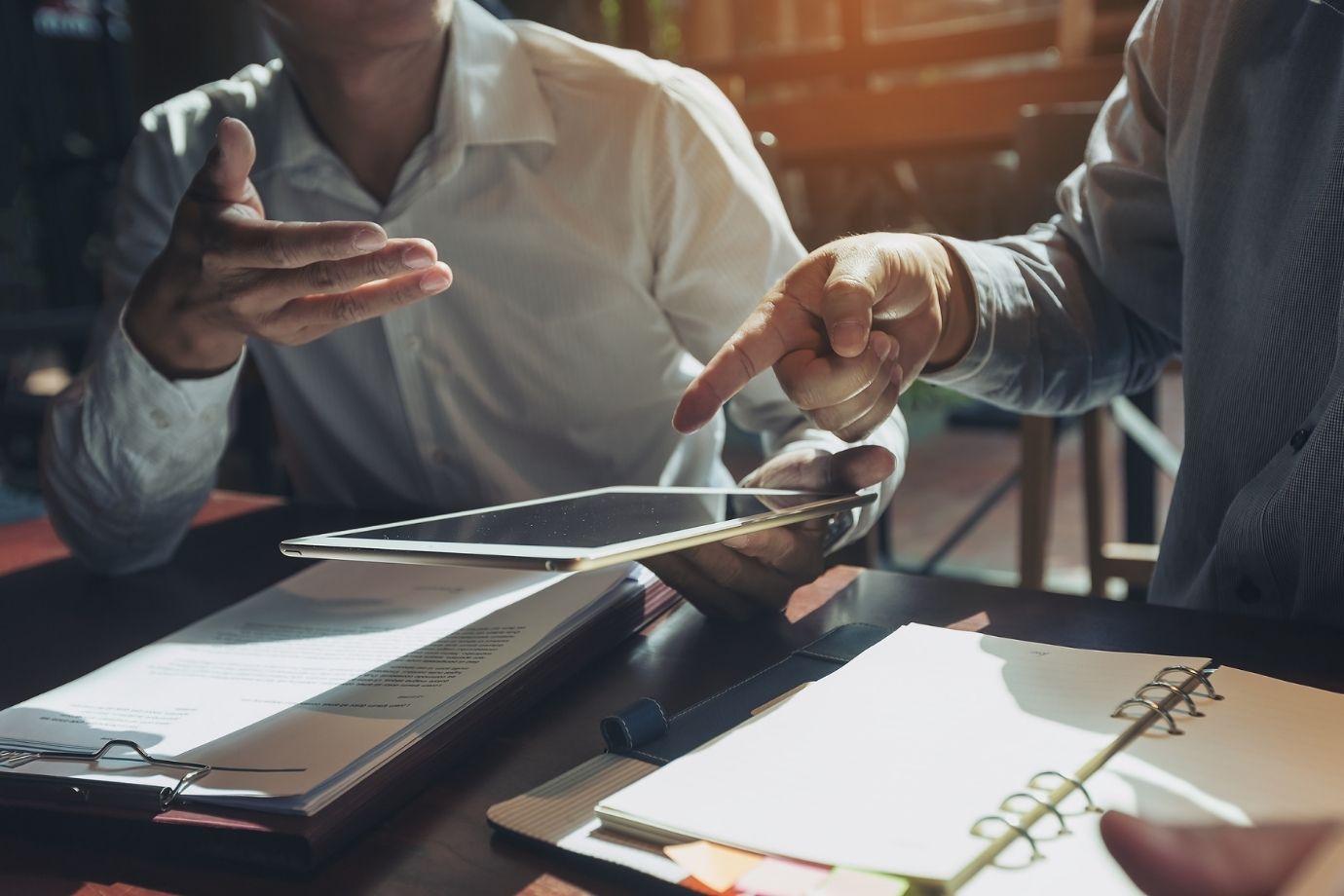
Warranty management is the overall process of creating, registering, administering, approving, tracking, and optimizing warranties. In recent years effective warranty management has gained substantial importance among OEMs due to its capabilities for improving the overall management of warranties. Adequate warranty management is necessary to streamline warranty processes and to deliver customers with warranty-related services in a timely and efficient manner.
There are several ways of managing warranties, including traditional manual modes, or using individual tools for different aspects of the warranty lifecycle. These traditional modes are quickly being overtaken by intelligent warranty management software which automates and streamlines the entire warranty process while also providing insights for long-term improvement.
Digital warranty management offers OEMs multiple advantages, including lower warranty costs, increased cost optimization, improved efficiency, lower risk of warranty fraud, and increased brand trust. While the initial implementation of warranty management software solutions may require some adjustments to a new system, the advantages are substantial. These days warranty management solutions are extensively customizable and can be adapted to suit the specific OEM size, industry, and goals.
Key Challenges in Warranty Management

Although warranty management offers substantial benefits to OEMs, there are also some challenges faced in warranty management, particularly in warranty claims management. These include:
1. Errors and Inefficiencies
Warranty management involves multiple steps throughout the warranty lifecycle, from the filing of initial claims, to review, and resolution. Using traditional or manual processes for warranty management can significantly increase the probability of errors, fraud, inconsistencies, and delays. A single error at any stage in the warranty claim processing can result in a need to review the claim overall and cause financial losses.
Apart from errors, manual processes are also resource intensive as more manpower is required to oversee the warranty claim management, which leads to increased costs. Traditional systems for warranty claims management are also less agile and can pose a challenge to scalable growth. Repair histories can also involve extensive paperwork and documentation which may also be prone to errors.
2. Poor Communication
Depending upon the size of an OEM, multiple departments can be involved in warranty claims management such as internal departments and external suppliers and repair centers. When multiple departments of an OEM are involved in warranty management and claims resolutions, poor communication can cause misunderstandings as well as further delays.
Apart from internally, poor communication with external stakeholders and customers can also negatively affect an OEM by lowering customer satisfaction and trust. Repeated lapses in communication can have long-term negative influences on brand reputation and can cause a loss of customer loyalty.
3. Delayed Updates
Warranty claims processing can take time and unforeseen delays may crop up. While such delays can be inevitable even with the most proficient warranty management systems, keeping customers in the loop is essential. Uninformed delays can be detrimental to brand reputation and customer satisfaction, however, for larger operations with high volumes of warranty claims, informing each customer is also challenging.
Apart from delayed updates to customers, delayed updates on warranty management system operations and insights can be a challenge for OEMs as well. Delayed updates and lack of availability of insights in real-time can hamper the ability to make informed decisions and identify key trends.
4. Missing Feedback Loops
In a traditional warranty management system, valuable feedback from warranty claims and processing can be missed. A missing feedback loop disrupts the flow of information throughout the stages of the warranty lifecycle and product development process. The lack of accurate feedback loops results in reduced flexibility, complexities in inventory management, and lost chances for product improvement.
Without feedback loops, finding the root causes of product failures that are triggering warranty claims can be difficult and the same underlying problem may extend across batches of products. A lack of feedback loops can also reduce supplier accountability as problems with products based on supplier components can be more challenging to identify.
5. Limited Visibility
Particularly for high volumes of warranties, keeping track of all the supported warranties, users, filed warranty claims, and processing statuses can be challenging. Without having clear visibility into all the data related to warranties throughout each stage of warranty claims processing, adequately responding to the claims becomes difficult.
Moreover, a lack of visibility into warranty-related data can pose a challenge for inventory management, resulting in further delays in fulfillment and increased costs on last-minute ordering. Limited visibility can also hamper claim tracking and create bottlenecks while also lowering the supplier recovery rate.
6. Lack of Transparency in Supplier Recovery
Supplier recovery is a key part of OEMs that have integrated suppliers into their warranty process, where OEMs can seek reimbursement from suppliers for defective parts that lead to warranty claims. By recovering costs from suppliers, OEMs can reduce their warranty and operational costs and improve product quality for the future.
A significant challenge for OEMs is the lack of transparency in the supplier recovery process which can lead to a negative impact on operations, supplier relationships, and strategic plans. This lack of transparency can be due to unclear identification of products suited for supplier recovery, and delays and errors in filing supplier recovery claims. Delayed or inaccurate supplier recovery claims have higher rates of rejection which can increase OEM warranty costs and deteriorate their relationship with suppliers.
7. Compliance Issues
Warranties can have extensive requirements for compliance, particularly to meet contractual, regulatory, and legal criteria. Depending upon the industry and region, compliance requirements can govern warranty terms and conditions, processing of warranty claims, customer rights, and even environmental regulations.
Adherence to warranty compliance standards can become challenging without a streamlined system, leading to potential financial and legal risks in warranty claim management. Variances in approval of claims can lead to potential legal complications and customer dissatisfaction.
8. Increased Operational Costs
Traditional warranty processes can lead to increased operational costs for OEMs due to a lengthier and more resource-intensive system for claims processing, thereby negatively impacting profitability. Higher volumes of warranty claims can overwhelm existing resources, delay resolution, and further increase operational costs.
Several factors can contribute to increased operational costs in warranty management, such as inefficiencies in processing warranty claims, inadequate supplier recovery, and inconsistent cost forecasting. As an OEM continues to grow and warranty volumes increase, a traditional warranty management system is at risk of overload, thereby surging operational costs and lowering efficiency.
9. Warranty Fraud
Warranty fraud is a key challenge for OEMs, accounting for anywhere between 3 percent and 15 percent of overall warranty costs. Moreover, instances of warranty fraud tend to increase in frequency and value if initial frauds are not detected and combated. This enables fraudsters to identify potential weak points in the warranty management methods used by an OEM and further exploit those weak points.
The challenge of combating and minimizing warranty fraud can be substantial, as there are different types of fraud possible. Although internal fraud is also possible, where employees are committing fraud, external fraud is considered more common. Warranty fraud can take place in several ways, including by submitting fake information on a warranty claim and intentionally damaging a product to file a warranty claim. Any type of warranty fraud consumes time and resources on an OEM, increasing their overhead and warranty costs.
How to Solve Key Challenges in Warranty Management
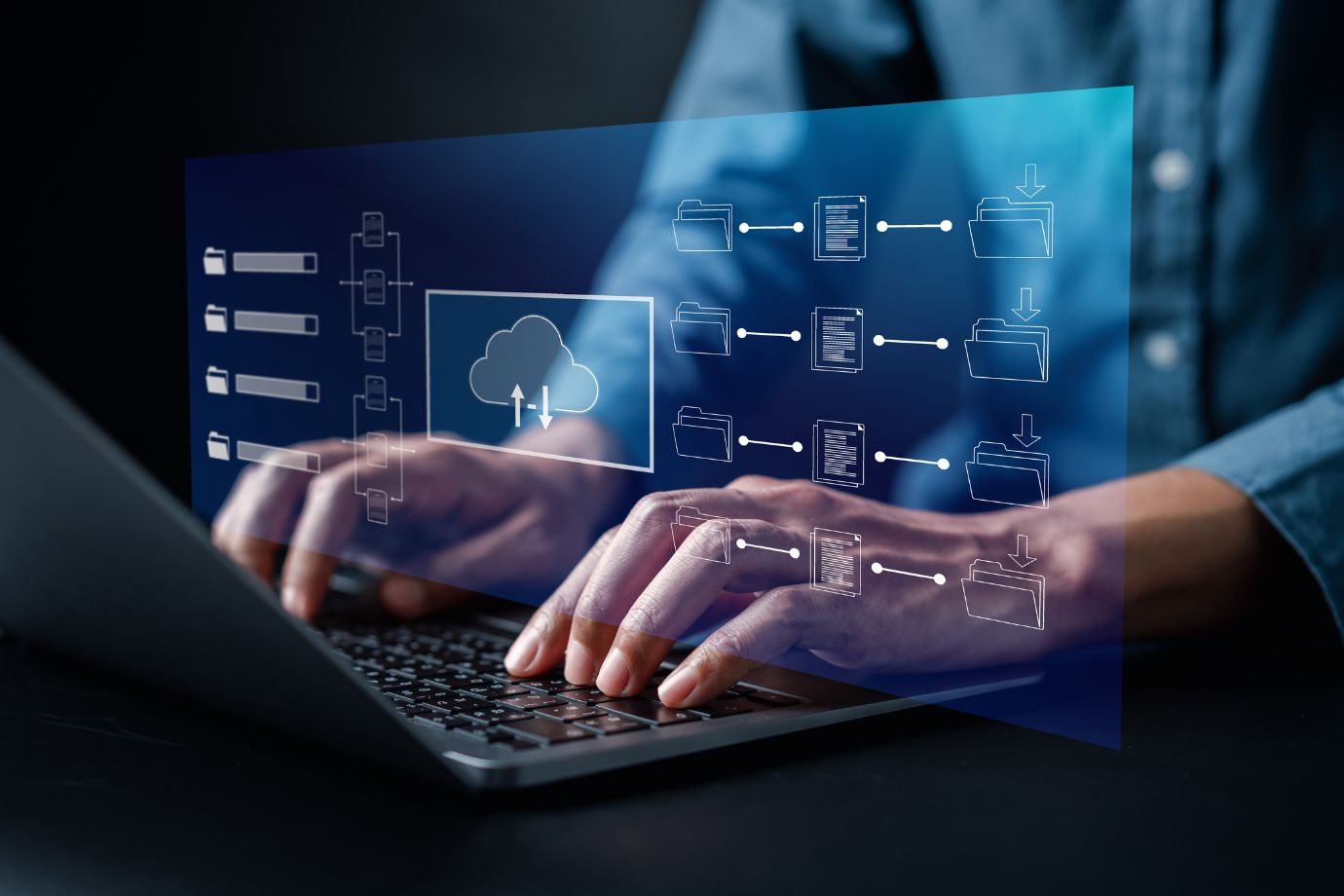
There may be multiple challenges in effective warranty management, however, with advancements in technology, the solution is simplified. Dedicated warranty management software is immensely capable and versatile, and can accurately and efficiently manage the entire warranty process from claim submission to supplier recovery. An automated and effective warranty management solution can streamline the processes involved in warranty claims management, thereby preventing errors and inefficiencies and helping to reduce costs.
The warranty management software can be customized to suit each OEM, and programmed with the specific warranties to be supported and compliance regulations that need to be met. Integrating these details within the warranty management software can ensure that policies are adhered to without any overhead costs or efforts. By adding verification and validation checks, the risk of warranty fraud can be reduced.
Modern warranty management software is also fully transparent with established audit trails, real-time updates, and support for improved communication with multiple stakeholders. Digital warranty management also has capabilities for data and advanced analytics which provide complete feedback loops and insights for improved long-term decision making. Supplier recovery rates can also be increased by implementing an automated claims process for warranty claims that meet specific requirements.
For OEMs with existing systems such as ERP or DMS, the warranty claims management software can be integrated for smooth operations and minimal interruptions. As effective warranty management software is highly flexible, it can be adapted to suit the specific needs of an OEM, catering to OEMs of all sizes and niches. Improving and streamlining the overall warranty claims management reduces labor requirements, administrative costs, and expensive errors, leading to overall lower operational costs.
Who Can Benefit from Warranty Management Software?
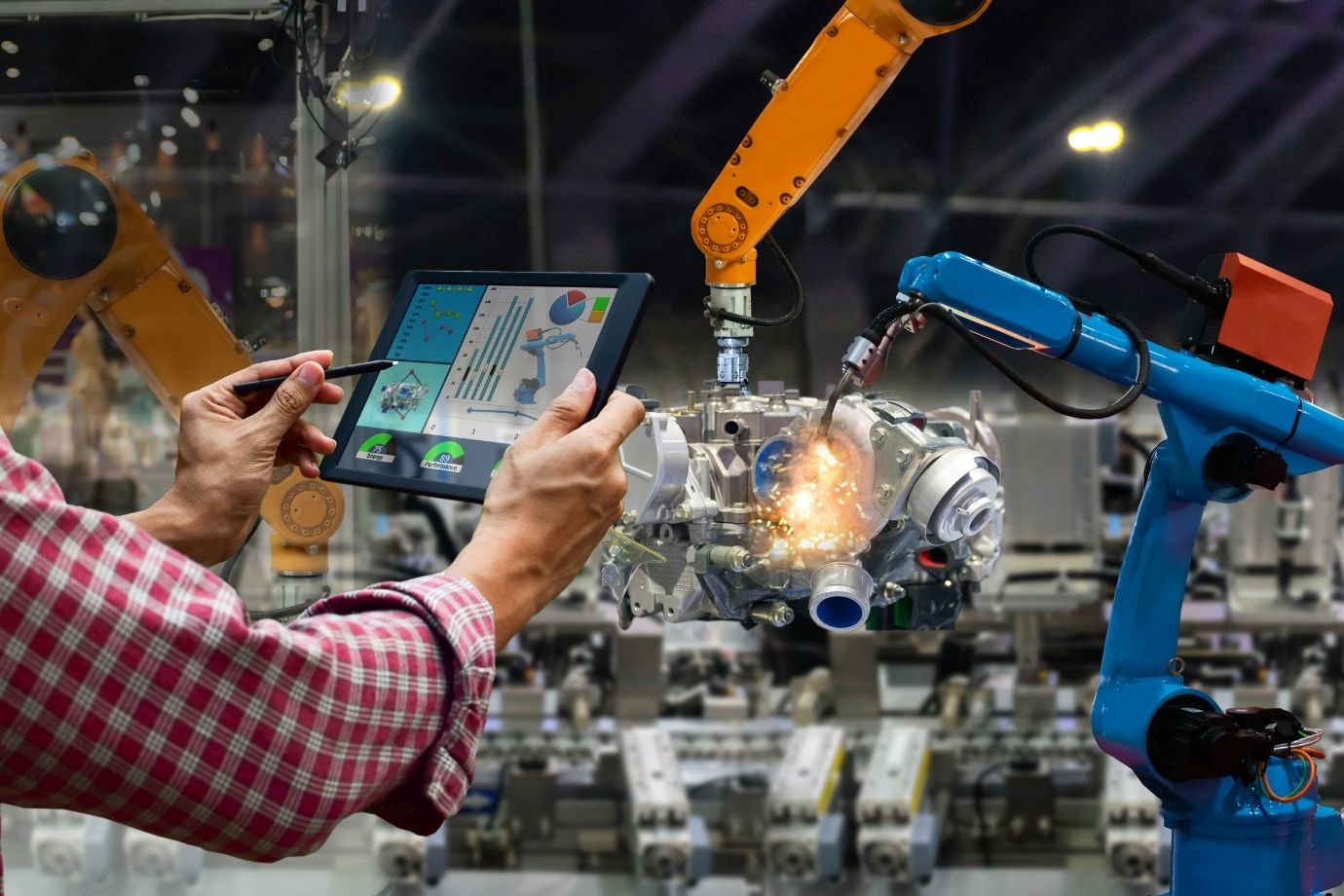
Warranty management software is immensely versatile and can be beneficial for any OEM dealing with warranties. However, some sectors have been early adopters of effective warranty management systems. These include:
1. Automotive
The automotive aftermarket sector is continuing to grow at a steady rate and with multiple parts and components involved in each automotive, there are numerous warranties involved. Warranty management solutions are immensely useful for automotive OEMs as the warranty and return processes can be complex.
With complicated documentation and varied claim types, there is an increased need for transparency throughout the warranty claim management system and improved coordination between stakeholders and OEMs. Warranty management systems can streamline the overall warranty process while providing increased transparency throughout the warranty lifecycle. An optimized warranty management system can aid automotive OEMs in reducing warranty costs and responding promptly to customers, aiding them in improving branding in a highly competitive field.
2. Electric Vehicles
The demand for electric vehicles (EVs) is growing in leaps and bounds as more people turn to EVs over combustion vehicles due to the cost savings they offer and environmental benefits. Governments worldwide are also encouraging the switch to electric vehicles over internal combustion vehicles to further reduce dependence on fossil fuels.
With the technology for electric vehicles continually evolving and the relatively unpredictable nature of electric vehicle breakdowns, warranties for EVs can be complex. OEMs tend to offer a wide range of warranties for electric vehicles, including for separate components and parts. Inefficient processes for warranty claims processing and supplier recovery are key challenges for electric vehicle OEMs. Moreover, delays in the processing of warranty claims can lead to extended downtime of equipment which reduces customer satisfaction and lowers brand image.
A robust and effective warranty management system can aid electric vehicle OEMs in the timely resolution of warranty claims and improve rates of supplier recovery. Advanced analytics from the warranty claim management system can also aid in future product improvement and in predicting trends for improved inventory management.
4. Agriculture Equipment
As more technology and equipment become integral to agricultural and farming activities, there is heightened importance of uninterrupted operations. Delays in the repair of agricultural equipment can have major consequences as they can delay farming activities on a larger scale.
With more complexities in agriculture equipment, OEMs are often dealing with higher volumes of warranties with diverse requirements. Warranty management solutions can aid agriculture equipment OEMs in providing faster resolutions to warranties so that interruptions to operations are minimal.
5. Construction and Mining Equipment
The construction and mining sectors are booming worldwide and with increased construction and mining activities, there is greater pressure on machinery and equipment. Unexpected downtime can cause significant delays in overall construction and mining downtimes and can reflect negatively on an OEM. The warranty process can also be complicated with varying parts and challenges with supplier recovery. Delays in warranty claims processing and supplier recovery can increase warranty costs and overall expenses of OEMs.
Accordingly, warranty management systems are significantly important for construction and mining equipment warranty process. With an adequate warranty management solution in place, OEMs can streamline end-to-end warranty management, simplifying claim initiation by dealers and adequate resolution by OEMs as well as supplier recovery. With multiple stakeholders often involved and equipment breakdowns in remote on-site locations, clear communication and transparency are vital for a positive brand image. Warranty management software improves transparency for all stakeholders, thereby aiding in improving customer trust and minimizing equipment downtime.
6. Aerospace
Aerospace equipment is highly specialized and complex, with minimal room for errors as parts malfunctioning while in the air can have devastating consequences. Accordingly, there are stringent regulations for aerospace products so that the sophisticated machinery is completely safe and secure. Warranties for aerospace OEMs are often thoroughly detailed and can include coverage of specific parts and components.
OEMs in the aerospace sector can benefit from warranty management systems that adapt to their specific warranty requirements and can adhere to all the applicable regulations. Extended warranties common in the aerospace sector can also be taken into account with warranty management software, making processing of delayed claims easier.
By automating warranty claims management, claims can be processed at a much faster rate so that warranties can be fulfilled without unnecessary delays. Since aerospace components and products tend to be high-value and with critical safety implications, having a rigorous system to examine warranty claims aids OEMs in improving supplier recovery rates and keeping warranty costs low.
6. Industrial Equipment
Industrial equipment can be immensely versatile depending upon the specific applications of the equipment and can include numerous individual parts and components. The complex functionality of industrial equipment and the importance of uptime has increased the importance of warranties from OEMs. Depending upon the OEM, additional types of warranties offered can include performance-based warranties and extended warranties.
With a wider range of warranties offered and often large-scale production of industrial equipment, reliable warranty management is essential. Industrial equipment OEMs can leverage warranty management software to offer a comprehensive range of warranties and cater to a vast customer base without sacrificing speed or efficiency in warranty management.
By utilizing smart warranty management systems, industrial equipment OEMs can specify claims processes for dealers and pre-programmed approval criteria for speedy resolutions. Warranty analytics can also be used to indicate future trends so that predictive maintenance can be done and breakdowns are prevented overall.
What is Intelli Warranty?
Intelli Warranty is a comprehensive and smart system designed for OEMs to aid in warranty claim processing and supplier recovery. An intelligent warranty management software, Intelli Warranty streamlines warranty management throughout the process. Adaptable to suit any number of warranties and warranties with different specifications, Intelli Warranty provides an improved experience for users and enhanced management for OEMs and dealers.
Variants of Intelli Warranty
Intelli Warranty is available in three variants, the core Intelli Warranty software, Intelli Warranty Lite, and Intelli Warranty for Consumer Goods OEMs. While all three are built on the same strong foundation as efficient warranty claim management software, there are differences based on the specific applications.
1. Intelli Warranty

The core Intelli Warranty intelligent warranty management software is designed for medium- and large-sized OEMs, offering specific features for seamless operations at scale. By automating the entire process of warranty claims management, OEMs can effectively support high volumes of warranties. The analytics provided are also immensely valuable in improving processes and products further for long-term reduction in warranty costs and increased profitability.
A key differentiation between Intelli Warranty and its variants is that the core Intelli Warranty software is equipped with features related to supplier recovery. The supplier cost recovery process is also automated so that approved claims are directly forwarded to suppliers for relevant reimbursements. There are also three dashboards provided, one for OEM use, one for dealers, and a third for suppliers for an overall streamlined warranty claim management system.
2. Intelli Warranty Lite
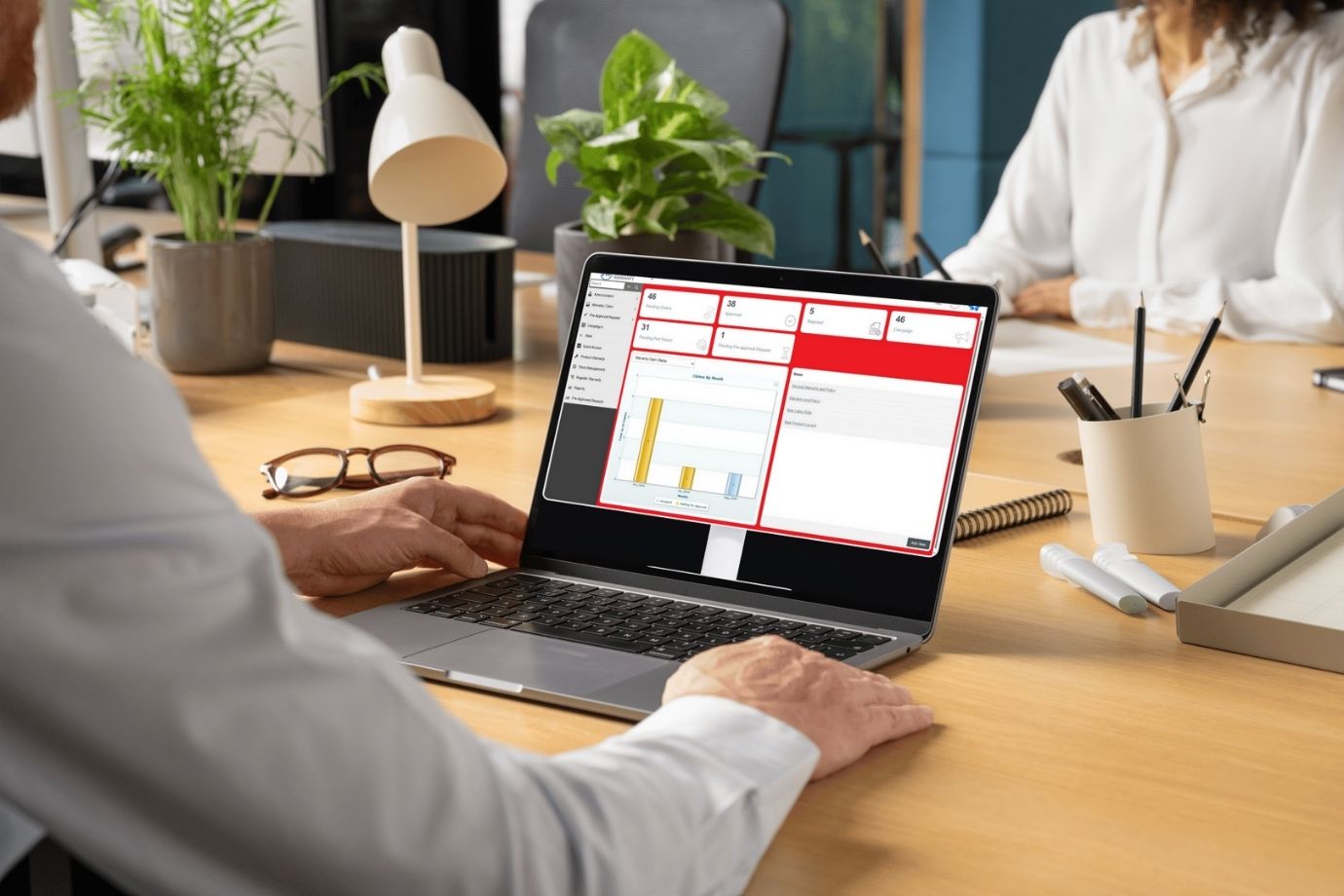
Intelli Warranty Lite is an integrated system to provides an all-in-one solution for streamlining warranty processes while also providing valuable insights for improved decision-making. It standardizes workflows, centralizes data, offers real-time insights, and improves communication thereby improving the overall capabilities for effective warranty management.
Specifically designed for smaller OEMs, keeping in mind their unique needs, Intelli Warranty Lite is flexible and can be customized to suit any industry or niche of products, to aid with digital warranty management. The primary features of Intelli Warranty are supported with Intelli Warranty Lite, along with a bonus feature for barcode and serial number generation. Another difference is the option for approving claims requests with either a replacement or reimbursement, while Intelli Warranty primarily focuses on reimbursements.
3. Intelli Warranty for OEMs in Consumer Goods Manufacturing
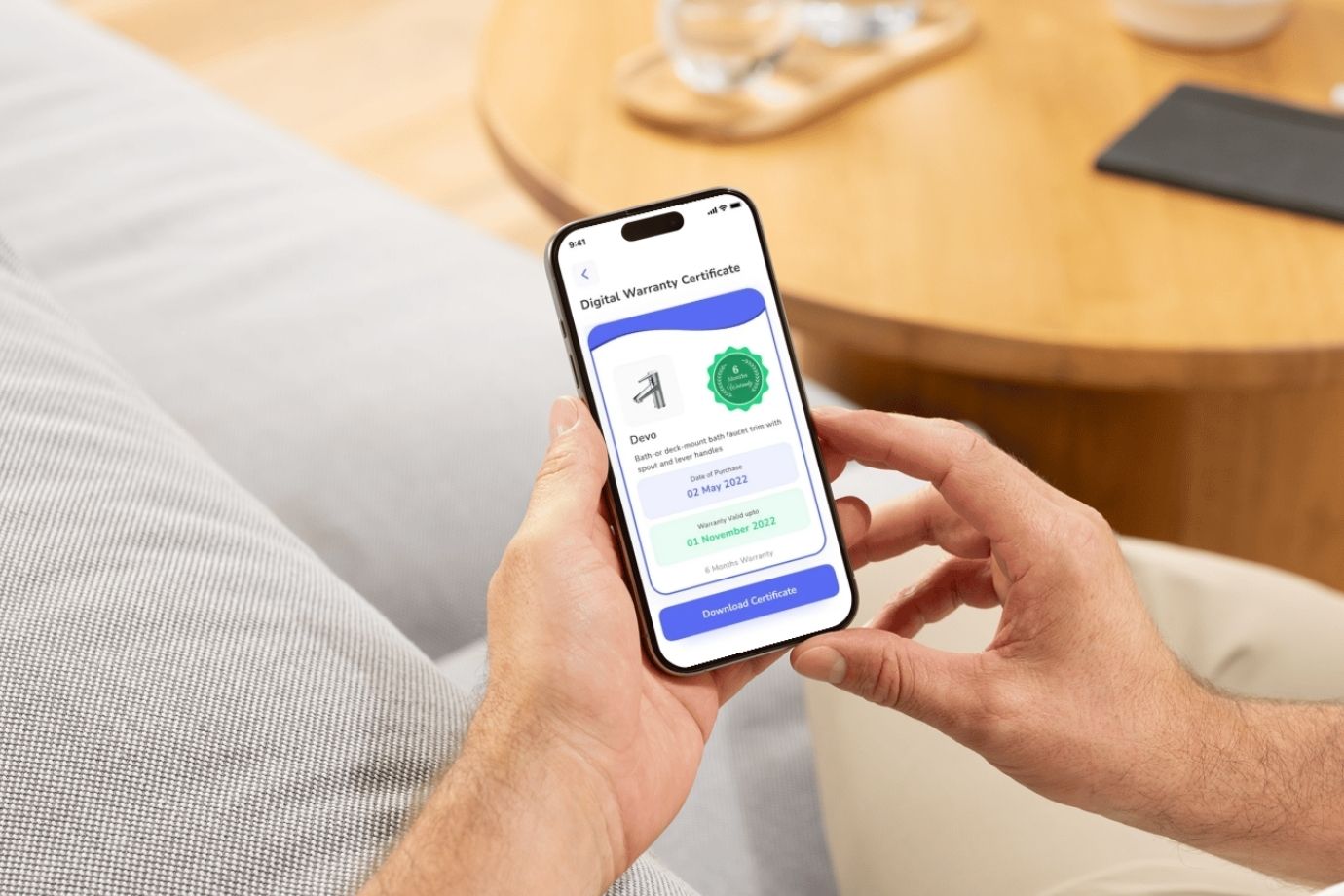
The expansion of the consumer goods market and increasing expectations and tech savviness of consumers are surging the demand for warranty management of consumer goods. Intellinet Systems offers dedicated warranty management software for OEMs dealing with consumer goods, through its Intelli Warranty for Consumer Goods OEMs. This software is designed to meet the complexities of warranty management involved in the sales of consumer goods, particularly through multiple sales channels.
Intelli Warranty for Consumer Goods OEMs facilitates seamless warranty registration, centralized management of complaints, allocation of smart technicians, complete resolution tracking, and streamlined invoicing. The features are designed to improve the customer experience while managing warranties in an efficient manner.
Top Features of Intelli Warranty
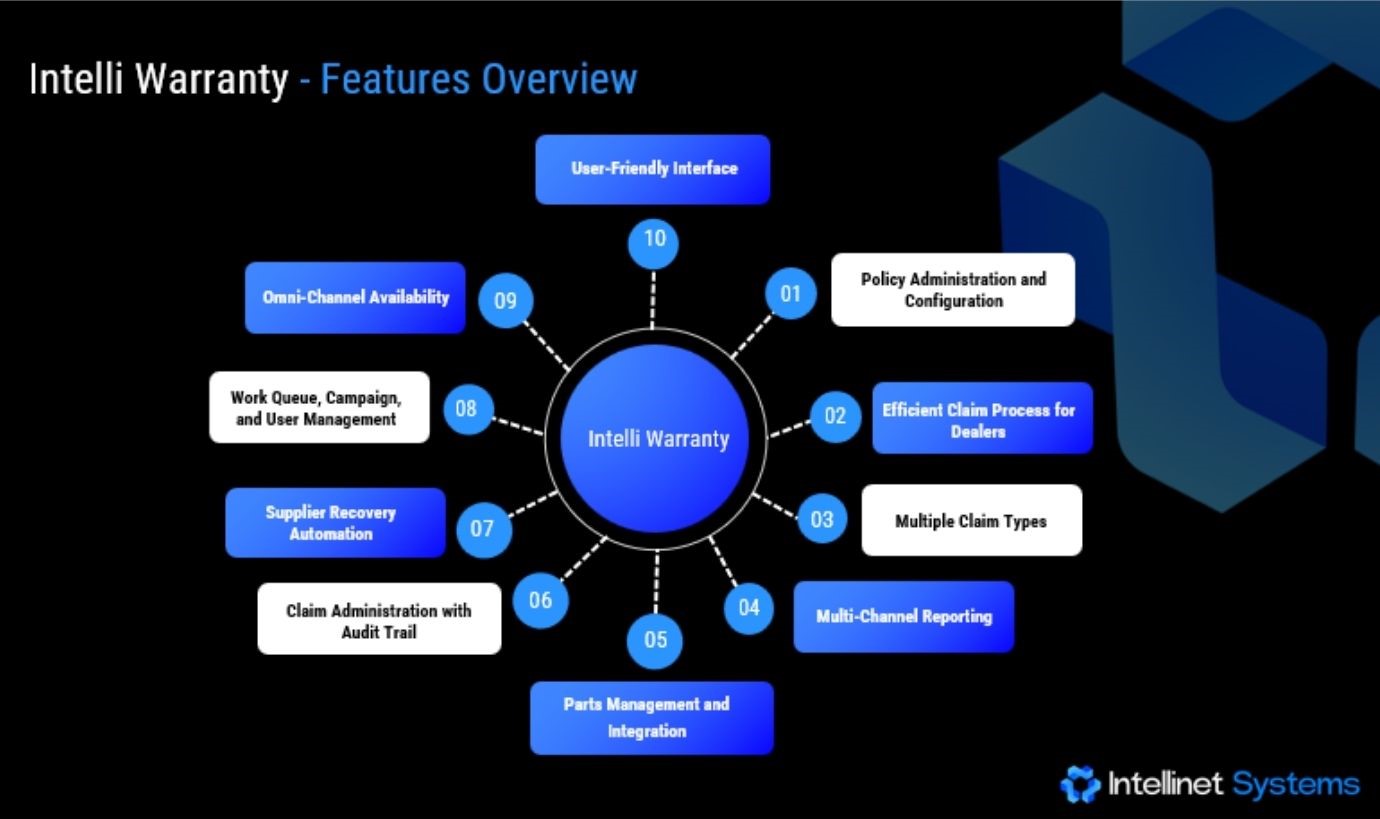
Intelli Warranty enables digital warranty management with a robust set of features that are designed keeping in mind the needs of OEMs. These features include:
1. Policy Administration and Configuration
Warranty terms can vary significantly between OEMs, depending upon a range of factors such as industry, type of products, OEM policies, and supplier connectivity. A standard template for warranty policies is often not suited for every OEM.
Intelli Warranty is an effective warranty management system that offers complete flexibility in policy administration and configuration so that any type of policy and coverage and be managed. Custom parameters that can be configured include component and part coverage, model versions, warranty terms, and payment reimbursement terms, among others.
2. Efficient Claim Process for Dealers
A confusing or lengthy claims process can be a hassle to fill and also increases the chances of errors or missed information, requiring more time to fix or add the required information. Delays in filing claims are inefficient and can add to the warranty processing time duration overall. A weak system for filing claims also increases the risks of warranty fraud as the system can be manipulated and fraudulent claims placed.
The entire claims process for dealers is streamlined with Intelli Warranty through features such as templates for claim creation and integration with existing systems. The option for validation checks and supporting document upload further increases the accuracy and speed of claims processing.
3. Multiple Claim Types
Different OEMs can have diverse needs in warranty management depending upon their industry, types of products, spare parts involved, and general policies. Supporting numerous claim types can be beneficial for boosting customer satisfaction and loyalty, however, managing multiple warranty types can be a hassle. Intelli Warranty offers streamlined management of multiple warranty claim types, including spare parts, campaign, OEM PDI, post-sale, dealer PDI, and goodwill.
Spare parts warranty claims typically cover specific parts for reasons such as defects or damages. Campaign warranty claims are generally in place for OEM-led warranty campaigns such as product updates or recalls. PDI, whether OEM or dealer, refers to pre-delivery inspection (PDI), where defects are identified and replaced before delivery of products to customers.
Post-sale warranties are common and involve manufacturing defects or issues with product or part performance that happen during the warranty period. Goodwill warranties are discretionary and can extend even beyond the formal warranty period. Warranty claims management software is capable of responding to each claim type based on pre-set parameters.
4. Multi-Channel Reporting
Warranty analytics and other data from warranty management systems can be immensely useful for forecasting and gaining insights. With Intelli Warranty, multiple reporting format options are supported, including PDF, Microsoft SSRS, and Excel, so that users can view reports in their preferred format.
Flexibility in reporting formats is particularly useful for OEMs that already use an existing system for viewing and analyzing data. The generated analytics from Intelli Warranty can be easily compared and examined within the warranty management software as well as externally.
5. Parts Management and Integration
To provide timely resolution of warranty claims, robust inventory, and parts management is essential so that when parts are flagged in a warranty claim, they can be processed promptly. For easier parts and warranty claim management and seamless integration, Intelli Warranty can be synced directly with systems such as SAP. This enables easier maintenance of part prices and information on suppliers, as well as specific exceptions.
Integration with EPC can also support direct verification to reduce errors and speed up the process. Intelli Warranty also supports integration with existing systems such as DMS and ERP through APIs and pre-built connectors with a jumper module for instant access to integrated systems. By integrating digital warranty management system with existing systems, there are minimal interruptions to standard operations and familiar interfaces supplemented with added capabilities.
6. Work Queue, Campaign, and User Management
A warranty management system involves a great deal of data of various types, including warranty claims and users. When dealing with large volumes of warranty claims from different sources and new dealers, there are heightened chances of errors and delays in processing, particularly with manual or traditional systems.
Delays and errors in warranty claims processing can reflect badly on an OEM, and result in a loss of customer loyalty in the long-term. Moreover, responding to high volumes of warranty claims traditionally also increases costs as more resources are needed to verify and authorize warranty claims. Intelli Warranty is a warranty management solution that streamlines all incoming claims requests and other data, responding based on rules set for dynamic parameters, through its Work Queue feature.
7. Claim Administration with Audit Trail
Intelli Warranty offers a dedicated claim administration feature that streamlines the entire claims process by supporting programmable parameters for auto-approval and partial approval. Depending upon the parameters set, for example, region or claim amount, claims can be directly approved, rejected, or more information be requested. This enables fast and accurate warranty claim management even in higher volumes, all without requiring added resources to verify individual claims.
The audit trail provided by warranty claim management software offers complete transparency throughout by documenting each stage, aiding in the accurate tracking of individual claims. Generation of an audit trail can prevent miscommunication in warranty processing and also provide detailed history and advanced analytics on warranty specifics on aspects such as users, products, and warranty type.
8. Omni-Channel Availability
Globally, different devices and channels are used for different purposes, such as desktops for fixed working locations, laptops for more flexible full-time working, and smartphones and tablets for on-the-go operations. To support operational flexibility and remote warranty management, Intelli Warranty offers omnichannel availability with its warranty claims management software.
Intelli Warranty can be accessed across a variety of channels and devices including desktop/laptop computers, tablets, and smartphones, with availability on native iOS, native Android, and web platforms. Dedicated Intelli Warranty apps increase the convenience of using warranty claims management software from any location at any time without sacrificing functionality. Mobile apps are particularly useful for dealers, technicians, remote workers, and urgent tasks.
9. User-Friendly Interface
The user-friendly interface across devices and channels makes the Intelli Warranty easy to operate for new users. For an easy transition into using Intelli Warranty, Intellinet Systems provides comprehensive user guides, training materials, and ongoing technical support.
The interface supports intuitive navigation and is equipped with graphical elements including interactive graphs to simplify data interpretation. Dedicated dashboards are provided for key stakeholders in the warranty claim management system such as the OEM, the supplier, and the dealer with access and features depending upon the OEM.
Bonus Feature of Intelli Warranty
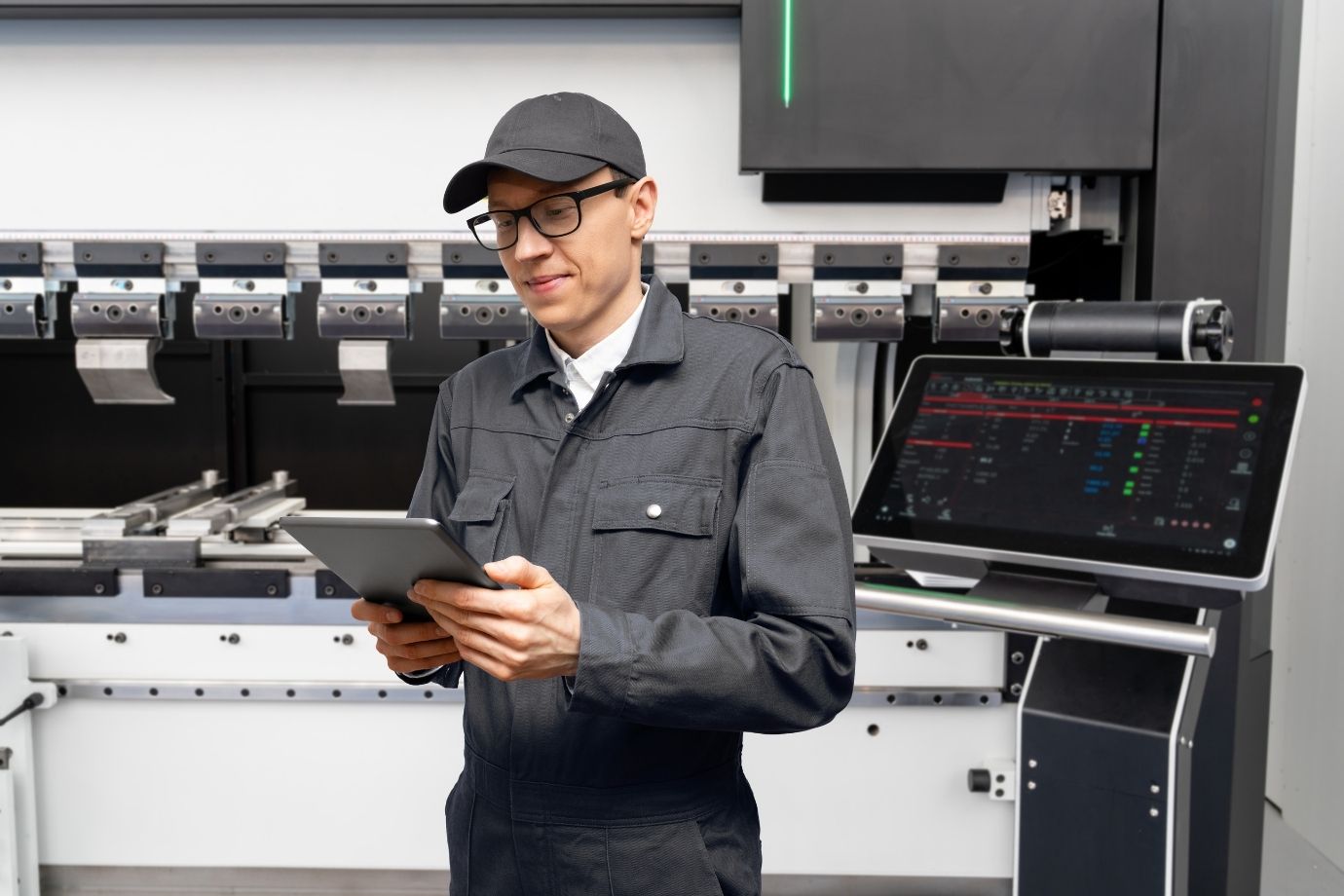
· Supplier Recovery Automation
For mid-size and larger OEMs that support supplier recovery, it is an integral component of warranty management as it can aid in mitigating costs incurred due to poor-quality supplies. However, supplier recovery can be a lengthy process for OEMs as warranty claims have to be evaluated and then identified as suited for supplier recovery. Once a warranty claim has been approved for supplier recovery, the process of filing a claim with the supplier can be lengthy and errors can result in rejection, leading to increased costs for the OEM.
By automating the generation of supplier claims upon approval of dealer claims, supplier recovery rates can be significantly boosted. System identification based on logic and programmed rules with options for manual approval offers increased flexibility and control in filing supplier claims. Incoming claims suited for supplier recovery can be automatically flagged and corresponding supplier claims filed, leading to a more efficient system for supplier recovery overall.
Bonus Feature of Intelli Warranty Lite
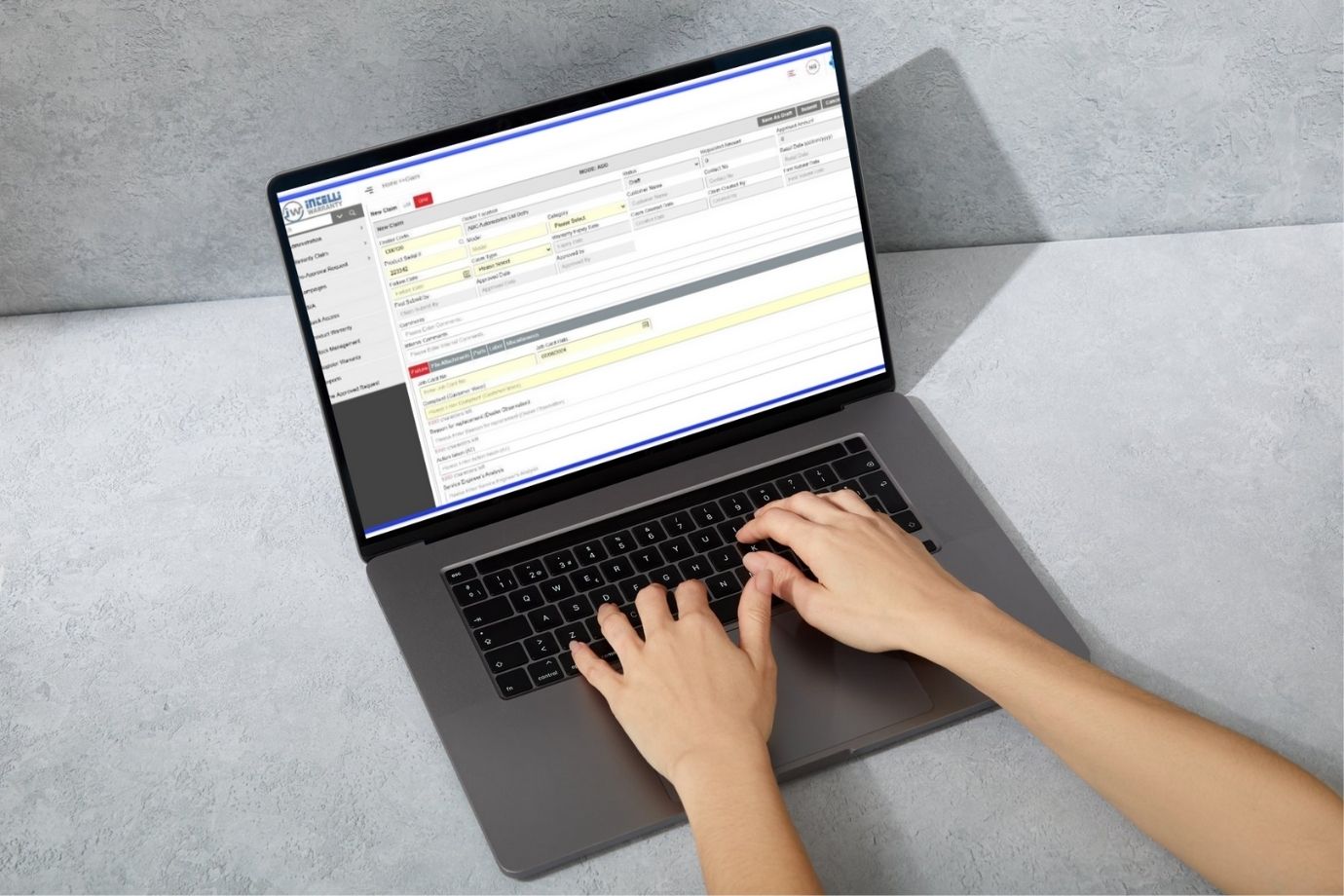
· Barcode and Serial Number Generation
Barcodes and serial numbers are immensely useful in identifying specific parts and they provide several functions. They aid in identifying the part precisely, aiding in tracking throughout the product lifecycle, and verifying product authenticity for warranty coverage. Easy identification of products through serial numbers and scannable bar codes also helps in improved inventory management as the movement of products can be tracked with greater accuracy and ease.
However, in some cases, products may be missing barcodes and/or serial numbers. The Intelli Warranty Lite comes with a specialized feature to generate new serial numbers and barcodes as needed for easier tracking of products. These serial numbers and barcodes are unique and can then be printed and attached to specific products and instantly scanned when needed.
Bonus Feature of Intelli Warranty for Consumer Goods OEMs
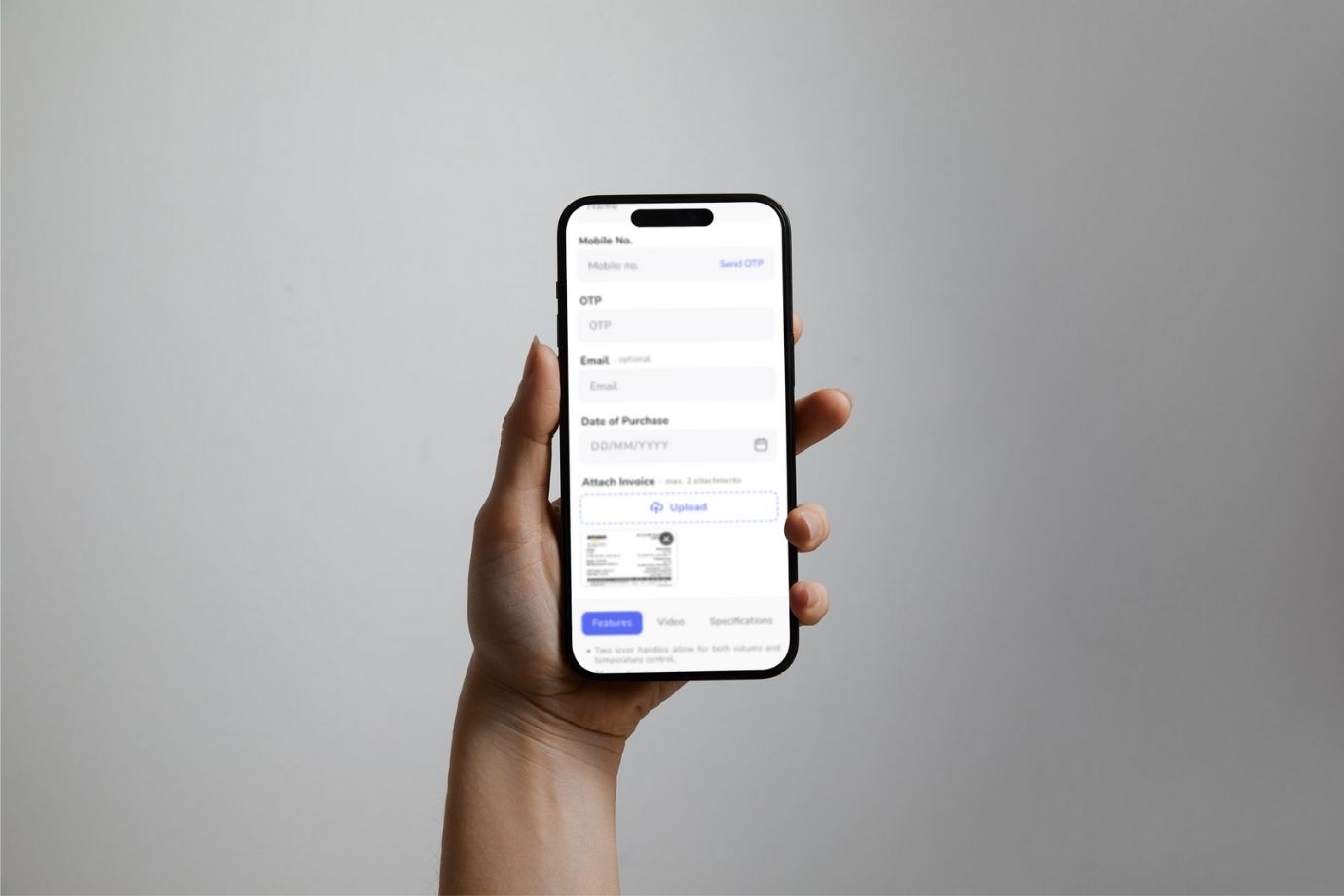
1. QR-Based Warranty Registration
Traditionally, warranties come into effect from the date of sale, however, for consumer goods, often the retailers or consumers do not register the warranty at the time of sale. Complicated registration processes can further delay warranty registration by users, leading to challenges at the time of warranty claims processing and increased complications for OEMs supporting the warranties.
Intelli Warranty for Consumer Goods OEMS supports an easy QR-based warranty registration process where consumers can instantly register their purchased products by scanning the QR code and entering the required details. Products are equipped with two QR codes, one placed inside the packaging, and one on the packaging itself. While the external QR code provides details related to the product and its warranty, the QR code inside the packaging is linked to warranty registration.
2. Centralized Complaint Management
When dealing with direct consumers, the types of complaints can vary substantially. Moreover, depending on the product, consumers may need help with filing accurate warranty claims. To cater to a wide range of customers, Intelli Warranty for Consumer Goods OEMs provides a centralized complaint management system within the warranty claims management software.
Customers can file their complaints through a form on the OEM website or app or call a toll-free number and connect with an operator who would file the complaint. Regardless of the input source, all complaints are compiled into the centralized warranty claim management system so that they can be responded to effectively. After verification of complaint details, technicians can be allocated based on customer location and availability of technicians.
3. Smart Allocation of Technicians
Depending upon the type of products sold, there can be a need to allocate technicians for product servicing under warranty. Coordinating with technicians and allocating tasks and customers can be cumbersome and result in errors which can increase dissatisfaction from customers. Intelli Warranty for Consumer Goods OEMs facilitates easy management of technicians through the smart allocation feature of the warranty claim management software.
A comprehensive dashboard is provided for technicians where they can directly access their assigned tasks and details of respective customers. Technicians can also review product details and service history for customers beforehand for better preparation.
During customer visits, technicians can document their work through the Intelli Warranty dedicated mobile app, including details such as parts replaced, photos of the product before and after service, and detailed service notes. These details help prevent miscommunication and maintain accurate product history for future warranty claims.
4. Streamlined Invoicing
Based on the warranty coverage and additional services incurred, there may be a need for separate invoicing. Managing invoicing manually or through traditional means can be prone to errors and challenging to track long-term.
Intelli Warranty for Consumer Goods OEMs has a built-in system for invoicing for the processing of out-of-warranty services and repairs. Directly through the Intelli Warranty app, when technicians document services performed and parts used, out-of-warranty repairs can also be noted. Technicians can then directly generate invoices for out-of-warranty services as well as corresponding payment links and send them to customers directly through channels such as WhatsApp, further simplifying warranty claim management.
5. Comprehensive Resolution Tracking
Tracking individual resolutions, particularly in large numbers, can be prone to errors, inconsistencies, and delays. Intelli Warranty for Consumer Goods provides real-time tracking for each and every service ticket, enabling accurate monitoring of the status and speed of resolution. OEMs can also access detailed MIS reports which provide detailed insights and advanced analytics into the service operations, aiding in informed and strategic decision-making for improving service operations long-term.
Top Advantages of Intelli Warranty
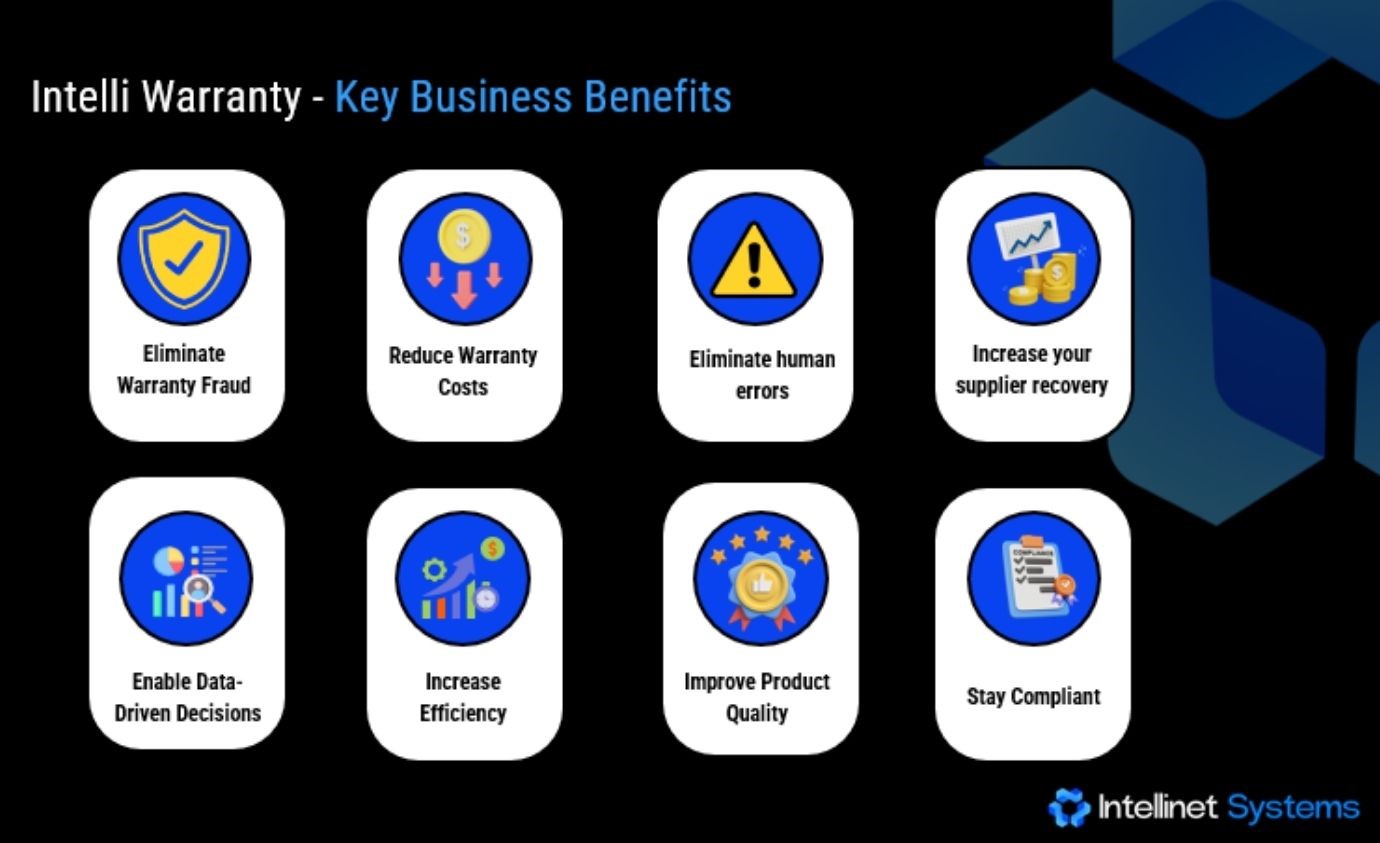
The versatile and robust range of features offered for warranty management solutions by Intelli Warranty and its variants provide several advantages, including:
1. Minimize Warranty Fraud
Warranty fraud is a key concern for OEMs, and Intelli Warranty provides a multi-faceted approach to target and eliminate warranty fraud. With a thorough verification and validation system in the warranty claims management software, there is greater scrutiny of warranty claims at the time of filing. The programmable system to respond to filled warranty claims also aids in flagging suspicious claims. By implementing a rigorous screening protocol, warranty fraud, and financial losses as a result of illegitimate requests can be prevented.
2. Reduce Warranty Costs
Warranty costs can easily add up, reducing the profitability of an OEM. Intelli Warranty enables streamlining of warranty processes and minimizing the need for manual intervention thereby aiding in reduced administrative and labor expenses for overall lower warranty costs. Moreover, the insights provided can aid in improving product quality and reducing warranty expenses in a more effective manner for the long term.
3. Eliminate Human Errors
Human errors are unavoidable and can cause unexpected mistakes and delays in warranty processing. By automating the warranty management process through Intelli Warranty, human errors can be eliminated for more accurate warranty claim processing. The validation checks and audit trails provided also lower the risk of errors in processing and generate accurate records of all warranty-related activities, thereby boosting the precision of the warranty claim management system.
4. Enable Data-Driven Decisions
Intelli Warranty provides comprehensive data and warranty analytics that can be used to improve decision-making for OEMs by enabling data-driven decisions. Warranty analytics examines aspects such as product and warranty performance, based on the overall claims filed in the warranty claim management system, identifying trends and forecasts for the future. OEMs can utilize these trends and forecasts to better plan and prepare for the future and stock accordingly.
5. Increase Efficiency
As a smart warranty management system, Intelli Warranty improves the efficiency overall of warranty claim management through automated processes and streamlined workflows that facilitate faster processing of claims and improved resource optimization. By automating systems, warranty claims can be processed quickly and without error, thereby enhancing the overall warranty management process while reducing costs.
6. Improve Product Quality
Although improving warranty claim management is certainly a priority, the end goal for OEMs is to reduce warranty claims overall. Improving product quality is foundational for reducing warranty claims as with improved products, customers will have no need to file warranty claims. Intelli Warranty aids in improving product quality by providing detailed insights on warranty claims filed which can be used to identify issues with particular parts or products and improve management processes.
Intelli Warranty Process
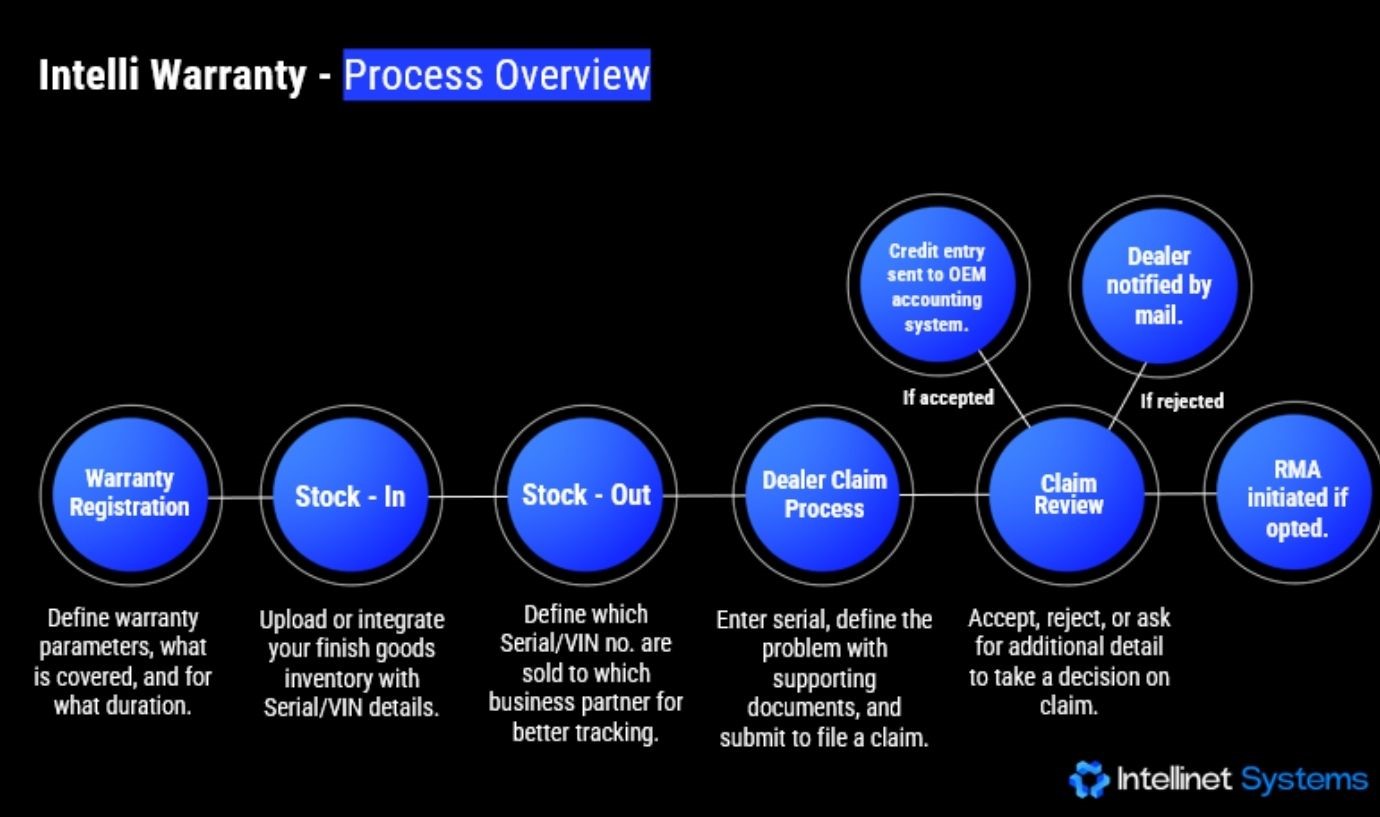
The Intelli Warranty process of warranty claim management is designed to be streamlined and efficient so that claims are processed accurately and quickly while preventing errors, delays, and bottlenecks. The process includes:
1. Warranty Registration and Definition
The first step in the warranty process is to define and register the specific warranty coverage policies for the claims that are to be supported. Particulars to add include parts or products under coverage, type of coverage, duration of coverage, and possible grace period.
2. Stock-In
In the stock-in stage, all the relevant available stock is entered into the warranty claim management software, either through integration with existing ERP or other systems or through an Excel upload. This record of stock can then be used for tracking availability for warranty claims support.
3. Stock-Out
Products or parts already sold to dealers are then integrated into the Intelli Warranty management system at this stage. The sales data can be uploaded through integration with a dealer business system, other systems, or using Excel. Tracking sales data aids in tracking secondary sales and potential warranty recalls.
4. Dealer Claim Processing
A dealer can then submit a claim to the warranty claims management software by selecting the specific product/part, type of claim, defining the customer complaint, and any other parameters as set by the OEM. Next, the supporting data would need to be added such as images, videos, and documents, as required by the OEM, after which the dealers can submit the claim.
5. Claim Review
The persons or teams authorized for processing warranty claims and warranty claims management are notified of new claims filed and can view all pending claims directly on their dashboard. Pre-programmed rules in the warranty claim management software can be used for processing claims based on meeting specific criteria or manually the claims status can be changed to approve, reject, or correction needed requesting additional information.
6. Notification to Supplier
Once a warranty claim has been approved, a notification is sent to the concerned supplier, through the digital warranty management system informing of the claim approval. Accordingly, a request for reimbursement is filed with the supplier for recovery.
Conclusion
Warranty costs may account for a relatively small component of an OEMs overall revenue, however, adequately managing warranties is of significant importance. Beyond reducing warranty costs, robust warranty management can aid in the prevention of warranty fraud, improve efficiencies, provide comprehensive insights, and reduce operational costs. The data and warranty analytics provided by warranty management systems can help improve inventory management, forecast future trends, and prove useful in overall product improvement.
Intellinet Systems offers smart and efficient warranty management software in the form of Intelli Warranty, along with its variants Intelli Warranty Lite, and Intelli Warranty for Consumer Goods OEMs. Fully customizable and equipped with features designed specifically to aid OEMs, Intelli Warranty is a smart and integrated warranty management system for the efficient management of warranty claims.
To learn more about Intelli Warranty and its suitability for your business, reach out to us today for a free demo.