Over the last few decades, manufacturing has almost been revolutionized. In the initial phases, it was all done manually and processes were as good as the people. Back when these sectors were extremely labor-intensive, there were many challenges that a manufacturer would have to face. Intricate assembly lines, reducing manufacturing costs, adopting new technology, etc. These were challenges that seemed very difficult to address, especially the ones on which all employees would have to be trained.
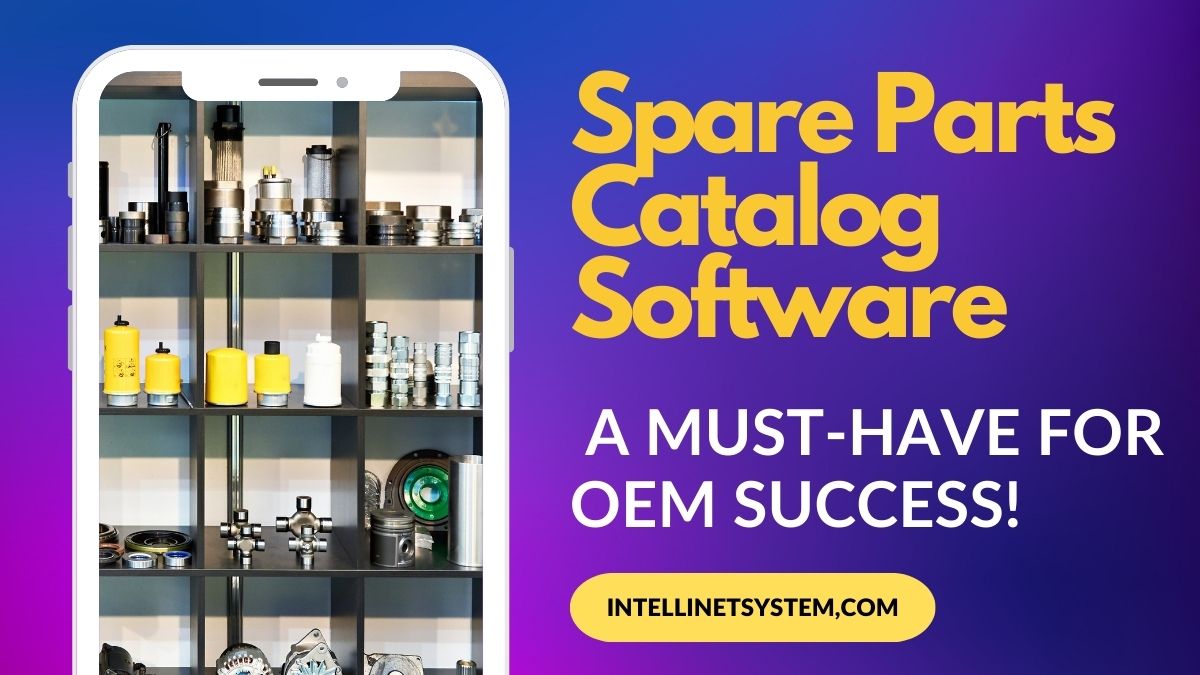
Thankfully, with the passing of time and the implementation of new technology and advanced machinery, these challenges have been catered to. However, there are many OEMs still battling the challenges of efficiently managing operational tasks. These tasks could be spare parts management, maintaining an efficient catalog, etc. These are the challenges that do not seem to be much and have a huge impact on the overall productivity of the OEMs.
In this blog, we will discuss the challenges faced by OEMs that do not use spare parts catalog software and the benefits of employing it.
Challenges faced by OEMs with Manual Parts Catalogs
While we talk about disruptions and the implementation of new technologies and innovation in the automotive sector, one often thinks about a robotic assembly line or maybe a new process to reduce the dependency on labor.
However, here we will talk about the challenges that OEMs face due to manual dependency. Let us see what are the challenges that an automotive OEM faces when they do not employ a spare parts management system:
1. Errors In Order Processing
Manual processes are prone to errors as they are maintained by humans. There could be errors related to part numbers, a minor error in the quantity, or maybe an error in the pricing part of things. This may seem like a minute error but from an organizational perspective, it is a huge loss in terms of revenue and personnel costs. This often leads to delays in order fulfillment, irritates customers leading to a lesser degree of customer satisfaction, and cost-intensive maintenance of such errors.
2. Limited Accessibility
With traditional and manual data systems, often the crucial data is not available. The limitation of the availability of crucial data leads to missed opportunities or delayed responses. The lack of availability of such information leads to OEMs not being responsive enough to changing market conditions. This leads to lost opportunities and loss of potential revenue for OEMs.
3. Lack of Data-Driven Insights
Insights play an important role in any organization. It may be marketing insights or operational insights, but it is always important to study and make relevant changes to your efforts. In this case, when an OEM misses out on the insights into spare parts performance, they are missing out on crucial information like market trends, consumer behavior, and performance of such spare parts. This leads to overlooking the areas and scope of improvement for OEMs further leading to cost-intensive measures to correct these mistakes.
4. Increased Operational Costs
Manually driven processes lead to errors and are sometimes inefficient in handling dynamic market conditions. They require dedicated resources and more time. Inefficient management of inventory, order processing errors, and delayed or poor customer communication can lead to costly overheads for organizations. These together can often hurt the revenues of an organization.
Embracing The Digital Solution: Spare Parts Catalog Management System
In the previous section, we saw the challenges OEMs face with manual processes related to spare parts management. The need of the hour is to embrace a spare parts management system to enhance productivity, reduce costs, and efficiently manage inventory among many other benefits. Adapting new and advanced solutions enables OEMs to better manage their operations and reduce the errors caused due to manual maintenance of processes.
In the ever-changing and dynamic market landscape, businesses need to be agile and quick to adapt to the new normal of global markets. Today, businesses have to rely on efficient and real-time insights in order to be nimble-footed towards managing business functions - be it marketing, operations, or any other business function. Let us now look at the benefits that OEMs can get by adapting this digital solution of spare parts management system.
1. Efficient Inventory Management
An efficient, centralized platform is required to manage inventory seamlessly. With such a solution, businesses can embrace a digital-first approach and facilitate a real-time stock and spare management approach. This not only makes businesses work in a future-forward approach but also reduces the workload on a specific team. This helps in managing inventory better and gaining a deeper insight into the performance of spares.
2. Streamlining Order Processing
Automation of traditional and redundant processes is what makes the business revenues grow further. The advantage of adopting such measures reduces the need to manually manage tasks which further reduces error in order processing. The Spare Parts Management System automates the order processing part of the business and ensures accuracy in processing large orders in one go. Error-free order processing also leads to seamless delivery and enhances customer satisfaction.
3. Enhanced Customer Experience
When a digital solution enables OEMs to provide a transparent, accurate and up-to-date information to customers, it helps in maintaining a degree of trust and loyalty of the customers towards the OEM brand. This in turn helps OEMs maintain and improve customer satisfaction.
4. Data-Driven Decision Making:
The Spare Parts Management System enables OEMs with real-time data and deep insights that enable them to make better decisions as quickly as the market changes. These insights are enablers for OEMs to forecast demand, and gain insights into trends in sales processes and performance of parts in the market. Such an in-depth analysis of spare parts enables OEMs to implement strategies for planning, optimize the pricing, and identify areas where there are scopes of improvement.
5. Cost Savings
We discussed the dependency of multiple resources when handling spare parts management the manual way and how it impacts the revenue of businesses. With the Spare Parts Management System, businesses can automate processes and reduce the dependency on manual intervention to achieve tangible cost savings. With reduced manual labor, minimized errors, streamlined order processing, and optimized inventory, OEMs can experience lesser overhead costs.
6. Regulatory Compliance
In addition to streamlining inventory, reducing costs, and providing deep insights, the spare parts management system also enables OEMs with a better understanding of regulations and compliances that they need to follow. These are industry regulations that need to be adhered to in order to be compliant with industry guidelines and compliance standards. This reduces the risk of non-compliance and ensures businesses work within the legal framework and avoid penalties due to non-compliance.
7. Enhanced Security
When dealing with such crucial information, OEMs need to have an extra layer of security to protect sensitive data. As this data provides such deep insights, it is only obvious that they need to maintain the data integrity and ensure there are no breaches. This information is crucial to businesses as it helps lay the foundation for the future approaches and the strategic plans of OEMs.
8. Improved Supplier Collaboration
Spare Parts Management System enables OEMs to have better collaboration with their suppliers and build a trusted framework. This streamlined framework enables better communication between OEMs and suppliers, leading to a better coordinated and managed system where both parties benefit. This helps build a more efficient supply chain where delays are minimized and has an enhanced reliability of manufacturing processes.
Conclusion
Today’s automotive and mobility industry has reached the current peak of speed, efficiency, and precision where these factors are supreme when one talks of innovation. With the advancement of new technologies and digitally enabled solutions, embracing spare parts management systems is one of the most sought-after software in the current industry.
These digital solutions not only help enable a streamlined inventory management approach but also ensure that the benefits are resonated along the entire spectrum of OEM operations. This enhanced degree of efficiency translates into cost savings, reduced dependency on manual efforts, and real-time accessibility to critical information. Such an advanced solution helps build a transparent and collaborative framework that is critical to both OEMs and their suppliers. This in turn would not only help OEMs but also their suppliers build better customer satisfaction but also a better brand loyalty towards the OEM.
The digital parts catalog software becomes the essence and catalyst for the digital transformation of businesses in today’s time. The adoption of spare parts catalog software becomes a defining moment for OEMs as they position themselves at the vanguards of the mobility revolution!
Intellinet Systems spare parts management system is such a solution where OEMs can benefit from a comprehensive solution towards a future of innovation in mobility.
Come, let us explore how we can- together- lead the transformative journey towards a sustainable future!