White Paper
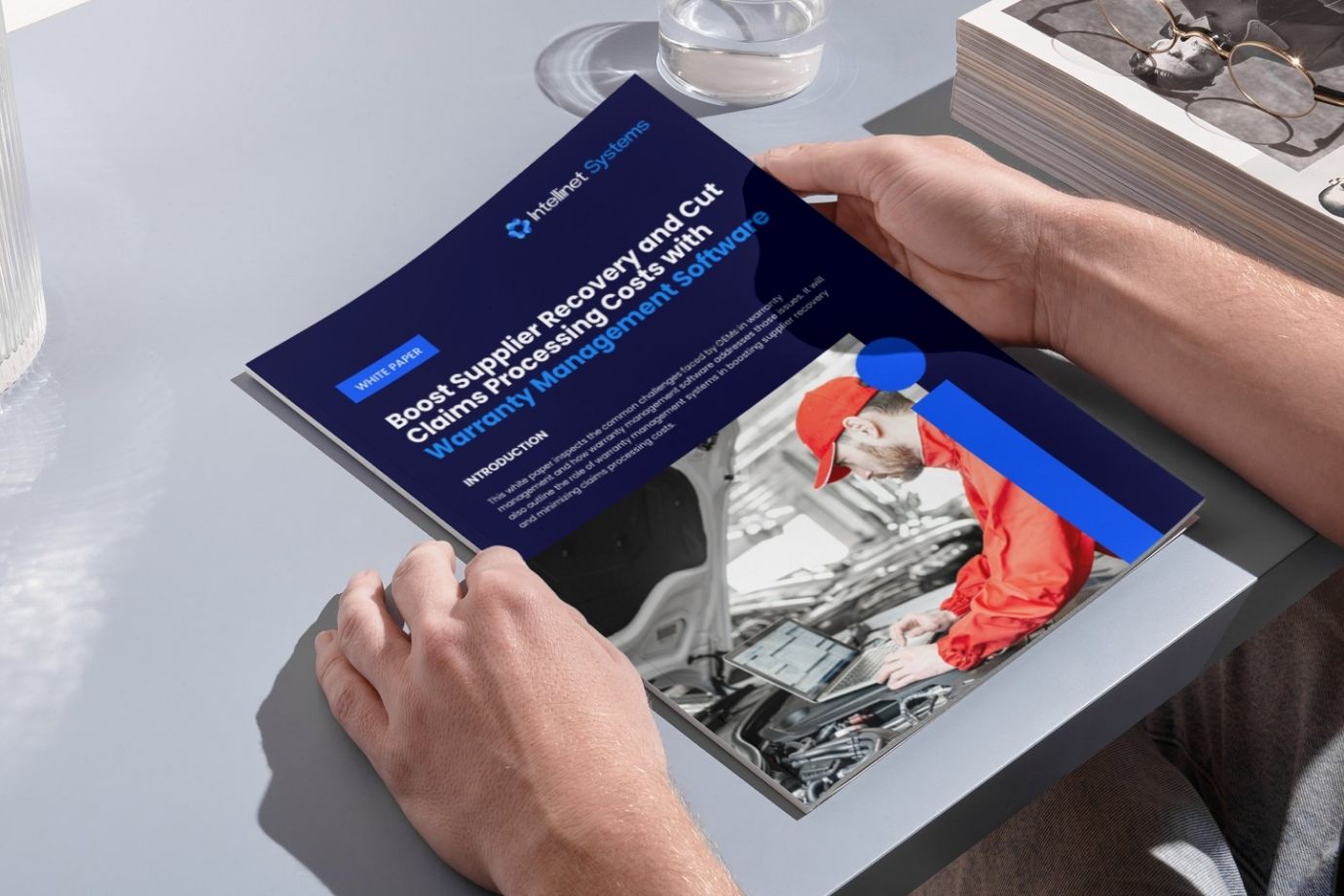
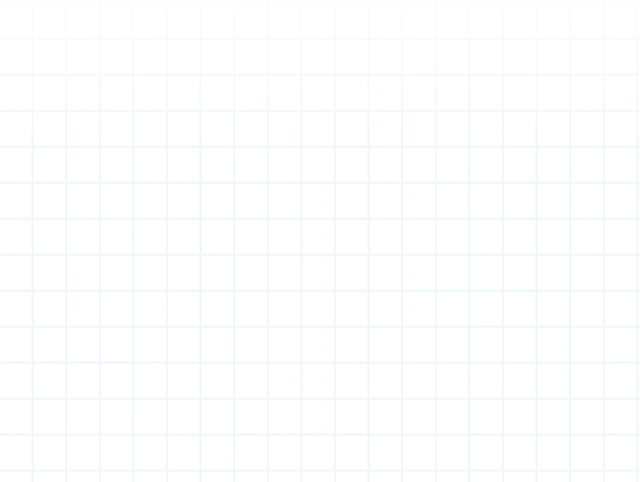
Introduction
This white paper inspects the common challenges faced by OEMs in warranty management and how warranty management software addresses those issues. It will also outline the role of warranty management systems in boosting supplier recovery and minimizing claims processing costs.
Executive Summary
The competitive manufacturing and distribution landscape pressurizes OEMs to manage warranty claims efficiently and recover costs from suppliers. Conventional processes for claims management involved manual intervention, leading to operational inefficiencies, high costs, and tense supplier relationships. These challenges intensify with scarce data visibility and resolution delays, resulting in revenue loss and diminished accountability.
Warranty management software is a robust solution for automating claims processes, streamlining supplier recovery, and enabling data-driven decision-making. Implementing automation and analytics enables OEMs to minimize operational costs, expedite claim resolutions, and enhance supplier collaboration. This results in improved OEM-supplier partnerships, optimize operations, and maximize profitability.
This white paper discovers major challenges allied with ineffective claims management, the benefits of implementing warranty management software, and how OEMs benefit from it.
Defining the Problem
An efficient recovery and warranty claim management process is crucial for OEMs to maximize operational efficiency and profitability. However, most OEMs strive due to outdated processes, making them incapable of catering to the demands of a fast-paced, data-driven market.
Warranty claims management across multiple products and suppliers is a complex process and often results in extended processing times and higher operational costs. Additionally, companies usually have fragmented databases and poor communication channels. This results in frequent challenges to hold suppliers liable for warranty obligations.
These inefficiencies not only affect the OEMs but also tense supplier relationships and customer satisfaction. The need for a robust solution to streamline warranty claims processing and maximize supplier recovery evolves here.
This white paper examines the challenges OEMs face in managing warranty claims and how adopting efficient warranty management software can handle these issues, drawing purposeful business results.
Problem Analysis
Manual processing of warranty claims dispenses various challenges, significantly impacting an OEMs efficiency and profitability. Here are a few crucial pain points:
1. Operational Inefficiencies
Manual intervention in claim tracking and processing requires excessive time and effort, leading to restrictions. Lack of systematic procedures frequently results in inconsistent claim handling.
2. Financial Losses
Managing claims manually incurs high operational costs. It also leads to incomplete information or delays in claim submissions, resulting in missed opportunities for supplier recovery.
3. Data Visibility Issues
Disconnected systems hinder seamless communication, making it difficult to track the claim statuses. This also limits the reporting capabilities, inhibiting the ability to identify trends and optimize processes.
4. Supplier Relationship Challenges
Due to a lack of proper tracking and accountability, suppliers may withstand fulfilling warranty obligations. Distorted channels cause delays in communication, further complicating issue resolution.
These concerns reinforce the need for a solution that streamlines processes, enhances supplier accountability, and reduces operational costs.
Challenges With Lack of Effective Software
Without effective warranty management software, businesses encounter several persistent challenges:
1. Administrative Burden
Claim processing turns resource-intensive and teams have to spend countless hours on manual tasks. It also leads to frequent errors and inconsistencies in claim documentation.
2. Data Silos
Since information related to warranty claims is usually spread across multiple systems, resulting in data fragmentation. Lack of integration among departments further obstructs collaboration and efficiency.
3. Delayed Claim Resolutions
Manual functioning causes restrictions, demanding extended time to process claims. Due to this, customers and suppliers face unnecessary delays.
4. Supplier Accountability Issues
Inconsistent documentation and poor tracking make it difficult to hold suppliers accountable. Additionally, limited visibility into supplier performance reduces the grip on negotiations.
These challenges underline the significance of introducing technology-driven solutions to mutate warranty management processes.
Business Benefits of Warranty Management Software
Implementing warranty management software offers multiple benefits, helping OEMs transform warranty management operations:
1. Automation of Claims Processing
By automating claim submissions, approvals, and follow-ups, warranty management software reduces manual effort. It also minimizes and accelerates processing times.
2. Enhanced Data Visibility
Warranty management software provides a centralized dashboard, furnishing real-time insights into claim statuses. This improves reporting potential, making room for data-driven decision-making.
3. Cost Savings
Automation of processes reduces administrative overhead, cutting operational costs significantly. It also makes resolutions faster, resulting in fewer disputes and better recovery rates.
4. Improved Supplier Relationships
By facilitating transparency in processes, warranty management software promotes trust among suppliers. Streamlined communication also enhances collaboration, improving accountability.
5. Data-Driven Insights
Warranty management software comprises analytics tools, facilitating trend identification, process optimization, and prediction of future warranty claim volumes. By analyzing data, it also provides actionable insights for continuous improvement.
Adopting warranty management software allows OEMs to achieve operational efficiency while saving costs. It also helps in improving communication and building strong supplier partnerships.
Numbers in Action
- Studies show manual claims processing is prone to errors, with error rates reaching 15%.
- Implementing automated warranty management systems reduces these errors to under 2%.
- Faster claim resolution reduces processing time by up to 40%, leading to a 20% increase in overall customer satisfaction scores.
- With real-time data integration, Warranty management tools improve reporting accuracy by over 50%.
- OEMs using advanced analytics in warranty management achieve an ROI increase of 45% over three years.
Explore details to reform your spare parts operations with valuable insights in this white paper.
Explore More White Papers
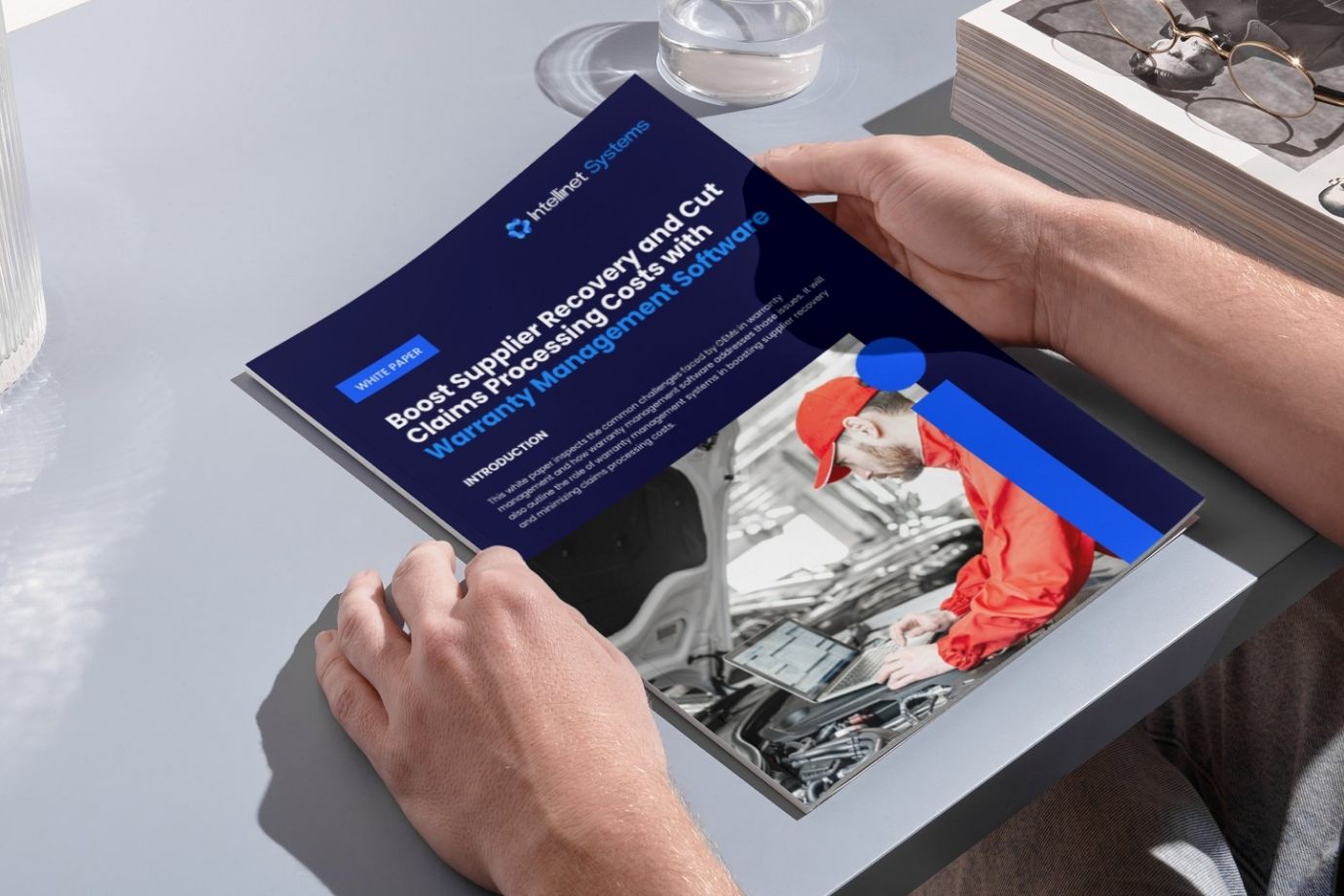
Boost Supplier Recovery and Cut Claims Processing Costs with Warranty Management Software
Explore how warranty management software boosts supplier recovery and cuts claim costs.
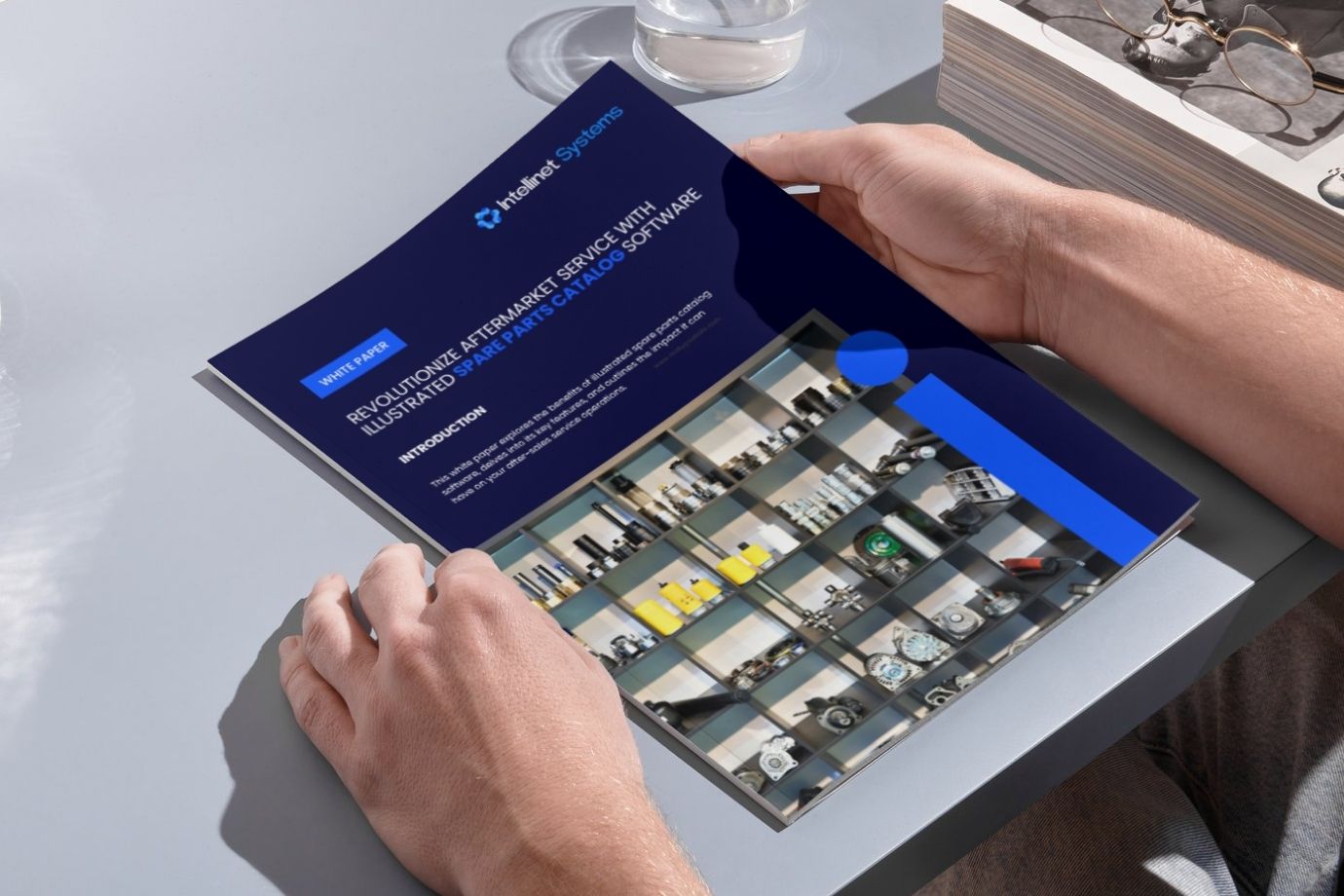
Revolutionize Aftermarket Service with Illustrated Spare Parts Catalog Software
This white paper explores the benefits of illustrated spare parts catalog software, delves into its key features, and outlines the impact it can have on your after-sales service operations.
Schedule a Free Demo, and go live in just 7 days
Our team will get back to you in 24 hours